Download PDF
Ford Battery Group's Adoption of RADIOSS Cut Methodology for Enhanced Simulation Performance
Technology Category
- Other - Battery
- Robots - Autonomous Guided Vehicles (AGV)
Applicable Industries
- Automotive
- Packaging
Applicable Functions
- Procurement
- Product Research & Development
Use Cases
- Transportation Simulation
- Vehicle Performance Monitoring
The Challenge
Ford's battery core team was faced with a challenge when working in tandem with vehicle development. The vehicle electrification engineering teams required a highly detailed CAE model of the battery arrays, including each cell and various packaging configurations considered in the design. This detailed model was necessary to predict the robustness of the battery structure using CAE simulation. However, the detailed model, which could grow to several million elements, needed to be significantly simplified when data was passed to full vehicle teams. The combination of a detailed battery model with the complexity of a full vehicle model significantly slowed the cycle time and hindered the ability to run optimization and design exploration for both teams.
About The Customer
The customer in this case study is Ford's battery core team. This team works in tandem with the vehicle development team and is responsible for creating detailed CAE models of battery arrays. These models include each cell and various packaging configurations that are considered in the design. The team's goal is to predict the robustness of the battery structure using CAE simulation. However, they also need to simplify these models when passing data to full vehicle teams, which presents a significant challenge.
The Solution
To resolve the conflicting requirements, Ford's battery core group adopted the cut methodology (sub-modeling option) in RADIOSS. They ran a full vehicle simulation after selecting a zone that included and surrounded the battery structure as a sub-model. This zone also contained a common interface to the full vehicle model. The full vehicle analysis was simulated using a generic simplified representation of the battery, which provided a quick turnaround time. The displacement and force history was imposed on the submodel boundaries, and this time history data was then extracted at the common interface that was selected previously. Subsequent analysis of a much more detailed battery model used the interface files as input produced from the sub-model analysis.
Operational Impact
Quantitative Benefit
Related Case Studies.
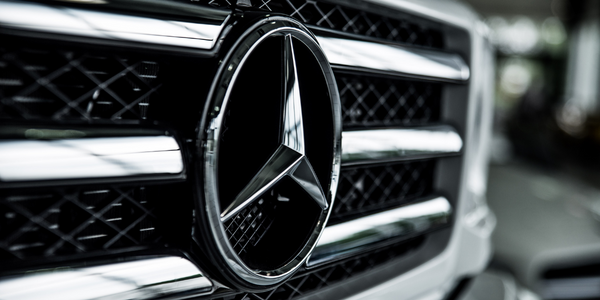
Case Study
Integral Plant Maintenance
Mercedes-Benz and his partner GAZ chose Siemens to be its maintenance partner at a new engine plant in Yaroslavl, Russia. The new plant offers a capacity to manufacture diesel engines for the Russian market, for locally produced Sprinter Classic. In addition to engines for the local market, the Yaroslavl plant will also produce spare parts. Mercedes-Benz Russia and his partner needed a service partner in order to ensure the operation of these lines in a maintenance partnership arrangement. The challenges included coordinating the entire maintenance management operation, in particular inspections, corrective and predictive maintenance activities, and the optimizing spare parts management. Siemens developed a customized maintenance solution that includes all electronic and mechanical maintenance activities (Integral Plant Maintenance).
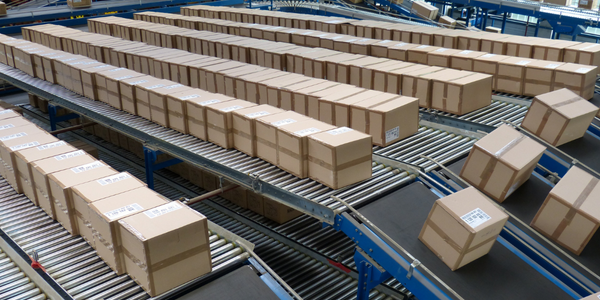
Case Study
IoT Data Analytics Case Study - Packaging Films Manufacturer
The company manufactures packaging films on made to order or configure to order basis. Every order has a different set of requirements from the product characteristics perspective and hence requires machine’s settings to be adjusted accordingly. If the film quality does not meet the required standards, the degraded quality impacts customer delivery causes customer dissatisfaction and results in lower margins. The biggest challenge was to identify the real root cause and devise a remedy for that.
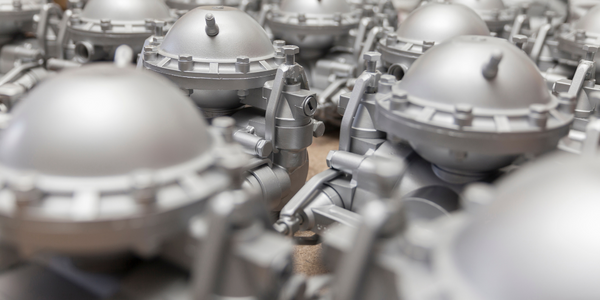
Case Study
Monitoring of Pressure Pumps in Automotive Industry
A large German/American producer of auto parts uses high-pressure pumps to deburr machined parts as a part of its production and quality check process. They decided to monitor these pumps to make sure they work properly and that they can see any indications leading to a potential failure before it affects their process.