Download PDF
Frozen Food Supplier Enhances Operational Efficiency with Tulip
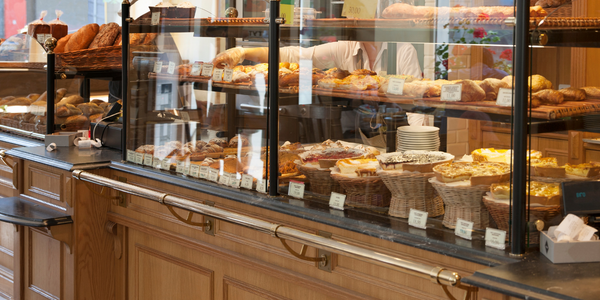
Technology Category
- Analytics & Modeling - Real Time Analytics
- Cybersecurity & Privacy - Identity & Authentication Management
Applicable Industries
- Equipment & Machinery
- Food & Beverage
Applicable Functions
- Facility Management
- Maintenance
Use Cases
- Real-Time Location System (RTLS)
- Supply Chain Visibility
The Challenge
The frozen food supplier, a leading provider of bakery solutions, was grappling with two major challenges. Firstly, the company was heavily reliant on paper-based processes to record machine downtime and the reasons for it. This method was often inaccurate and difficult to aggregate, leading to a lack of visibility into the plant's metrics. Consequently, line supervisors and plant management lacked the critical information needed to prioritize and address issues impacting throughput. Secondly, the company had to perform cumbersome and time-consuming audits to comply with the stringent requirements of the food and beverage industry. These audits ranged from PPE audits, pre-production checks on equipment, and periodic checks on the metal detector. The combination of these problems resulted in a lack of visibility into the plant's performance and the issues that needed to be mitigated.
The Customer
This company is a leading supplier of frozen bakery solutions
About The Customer
The customer in this case study is a leading supplier of frozen bakery solutions to the food service and in-store bakery business segments. The company combines advanced bakery technologies with a collaborative business approach to create and manufacture on-trend bakery concepts for leading global, national, and regional customers. Operating in the food and beverage industry, the company has to comply with stringent HSE regulations. The high-throughput nature of the plant makes it critical to keep machines running efficiently. The company was facing challenges with paper-based processes and a lack of visibility into plant metrics.
The Solution
To address these challenges, the company implemented Tulip, a digital machine monitoring solution. Tulip starts recording information on machine errors or malfunctions that cause downtime either when machines output a fault code via the OPC UA server or when an operator manually stops a machine. This triggers a downtime state within Tulip, alerting operators and allowing them to swiftly address and fix the problem. The solution also enables team members to report scrap whenever material fails to meet quality standards. All this information is aggregated into visual and real-time dashboards that line supervisors and plant managers can use for data-driven decision-making. For audits, the team built digital audits that can be performed from tablets. These apps are composed of intuitive and user-friendly checklists that can be performed on predefined schedules. The data is synced in real-time, alerts are sent to teams when areas have been released, and all past audits are securely stored for future reference.
Operational Impact
Related Case Studies.
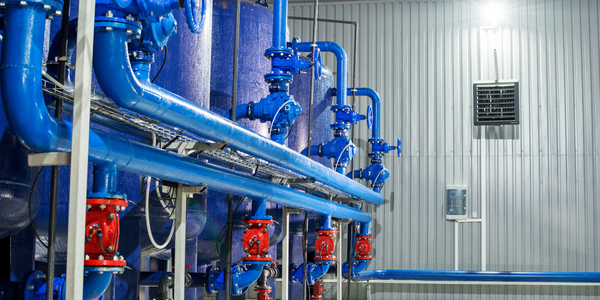
Case Study
Smart Water Filtration Systems
Before working with Ayla Networks, Ozner was already using cloud connectivity to identify and solve water-filtration system malfunctions as well as to monitor filter cartridges for replacements.But, in June 2015, Ozner executives talked with Ayla about how the company might further improve its water systems with IoT technology. They liked what they heard from Ayla, but the executives needed to be sure that Ayla’s Agile IoT Platform provided the security and reliability Ozner required.
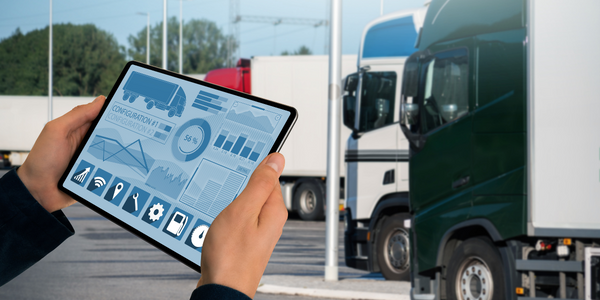
Case Study
IoT enabled Fleet Management with MindSphere
In view of growing competition, Gämmerler had a strong need to remain competitive via process optimization, reliability and gentle handling of printed products, even at highest press speeds. In addition, a digitalization initiative also included developing a key differentiation via data-driven services offers.
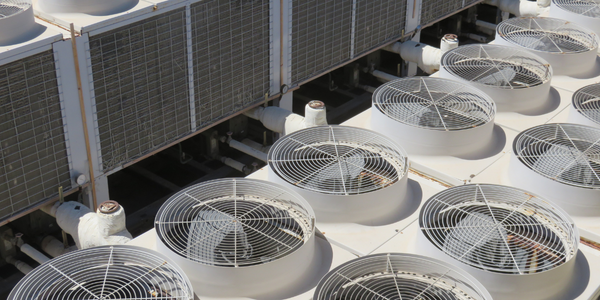
Case Study
Predictive Maintenance for Industrial Chillers
For global leaders in the industrial chiller manufacturing, reliability of the entire production process is of the utmost importance. Chillers are refrigeration systems that produce ice water to provide cooling for a process or industrial application. One of those leaders sought a way to respond to asset performance issues, even before they occur. The intelligence to guarantee maximum reliability of cooling devices is embedded (pre-alarming). A pre-alarming phase means that the cooling device still works, but symptoms may appear, telling manufacturers that a failure is likely to occur in the near future. Chillers who are not internet connected at that moment, provide little insight in this pre-alarming phase.
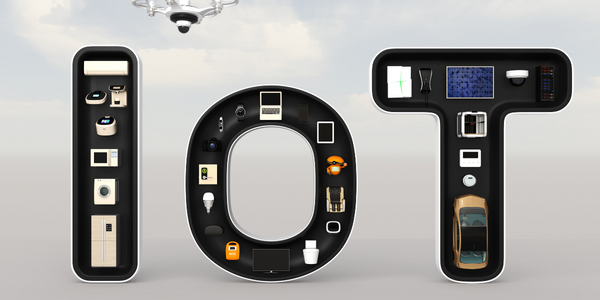
Case Study
Premium Appliance Producer Innovates with Internet of Everything
Sub-Zero faced the largest product launch in the company’s history:It wanted to launch 60 new products as scheduled while simultaneously opening a new “greenfield” production facility, yet still adhering to stringent quality requirements and manage issues from new supply-chain partners. A the same time, it wanted to increase staff productivity time and collaboration while reducing travel and costs.
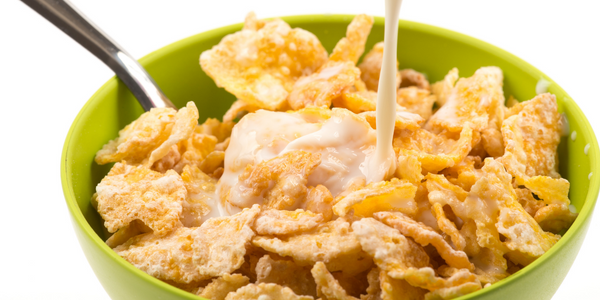
Case Study
The Kellogg Company
Kellogg keeps a close eye on its trade spend, analyzing large volumes of data and running complex simulations to predict which promotional activities will be the most effective. Kellogg needed to decrease the trade spend but its traditional relational database on premises could not keep up with the pace of demand.
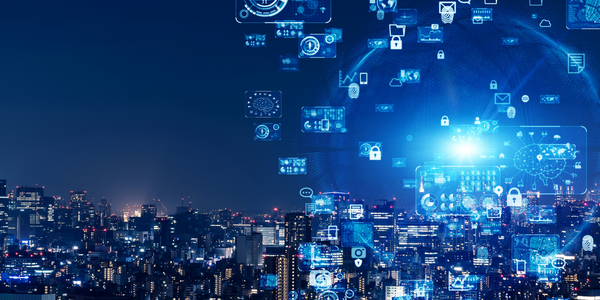
Case Study
Integration of PLC with IoT for Bosch Rexroth
The application arises from the need to monitor and anticipate the problems of one or more machines managed by a PLC. These problems, often resulting from the accumulation over time of small discrepancies, require, when they occur, ex post technical operations maintenance.