Download PDF
Fully Automated Identification for Alping Italia
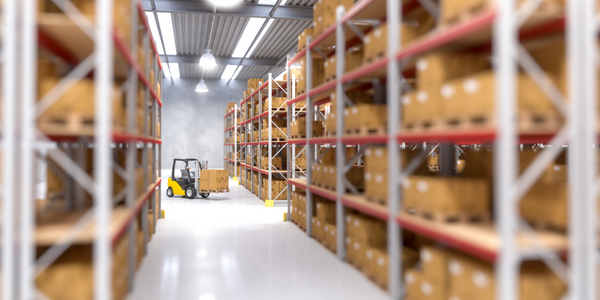
Technology Category
- Functional Applications - Remote Monitoring & Control Systems
- Networks & Connectivity - RFID
- Wearables - Tags & Patches
Applicable Functions
- Process Manufacturing
Use Cases
- In-process Traceability
The Challenge
Full material traceability ensures process reliability in production and it is a major building block for the economic success of manufacturing companies. To optimise production management, automated identification systems with tags which have barcodes printed on them are now increasingly used in production facilities and warehouses. This ensures full control from the receipt of raw materials to the finishing of the products and shipping.
The steel industry in particular, is a difficult environment and the labels and tags that ensure full material traceability have to withstand extreme conditions. Raw materials and products have rough surfaces. In addition, the data carriers are exposed to enormous heat and heavy soiling. And last but not least, the whole identification process always has to be carried out under time pressure.
The Customer
Alping Italia
About The Customer
Alping Italia was set up in 1998. Its core business is the
development of bespoke systems in the field of industrial automation. The founders of this innovative company had already been working as consultants for ten years. Alping Italia employs around 30
The Solution
For such a challenging environment, GRAPHIPLAST® labels
and tags proved to be the ideal solution. A robot which is controlled by special software welds a pin to the steel using a stud welder, attaching the barcode-printed tag. This is all done within 8-10 seconds which is well-within the time requirement stipulated by Alping Italia.
This fully automated identification system has been especially developed for the requirements of the steel industry. Requirements such as resistance to extreme heat, heavy soiling and the shorter production times in the individual phases of steel manufacture were incorporated into the concept and resolved.
and tags proved to be the ideal solution. A robot which is controlled by special software welds a pin to the steel using a stud welder, attaching the barcode-printed tag. This is all done within 8-10 seconds which is well-within the time requirement stipulated by Alping Italia.
This fully automated identification system has been especially developed for the requirements of the steel industry. Requirements such as resistance to extreme heat, heavy soiling and the shorter production times in the individual phases of steel manufacture were incorporated into the concept and resolved.
Operational Impact
Related Case Studies.

Case Study
IoT Gateway Enables Faurecia to Improve Traceability for Customers
While Faurecia has a long track record of providing its customers with exemplary products, the increasing need to provide customers traceability for the parts it was producing motivated the company to further support these efforts. The large automotive OEMs expected Faurecia to be able to both track the process of operations and production and to make that information available on demand. For example, customers wanted to know which airbags were added to which cars, as well as detailed data characteristics about how each airbag was installed, including torque and angle of installation.
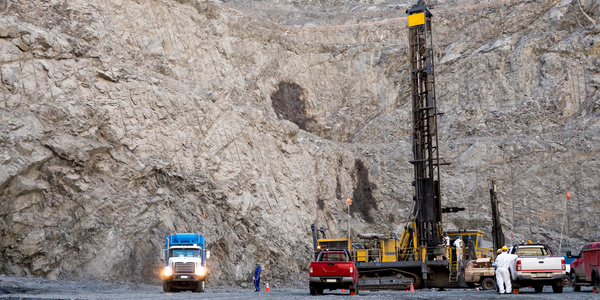
Case Study
Tray Identification at the Kennametal Drill Plant
Kennametal's high quality drill bits along with their associated aluminium trays where they are arranged go through a thorough cleaning process involving ultrasound, damp and vacuum cleaning processes after machining is performed. Before entering this washing facility, the order documents and the tray are separated and then re-allocated after cleaning. A work step that involves a risk as analyses have shown that, on occasion, trays and order documents were allocated incorrectly after cleaning. Drills went through coating processes that were supposed to be used for a different order. Hence, there was a need to eliminate mix-ups altogether.
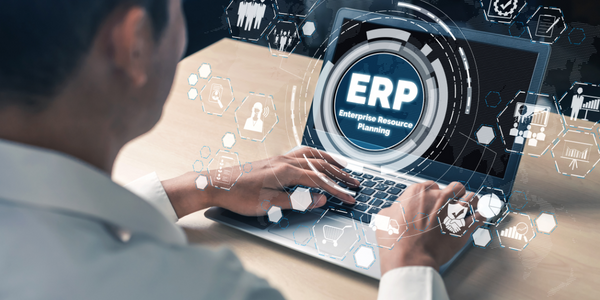
Case Study
Tripling Sales with Deacom ERP: A Case Study on Copps Industries
Since 1979, Copps Industries has been a global provider of epoxy resins to various markets. However, the company faced challenges in scaling to meet market demand due to outdated technology and manual workarounds to fill in process gaps. The company relied heavily on people to deliver scalable and repeatable processes, which limited the volume of SKUs manageable by their small team. Copps was also burdened with an outdated disk-operating system (DOS) that no longer supported its business needs, and employees struggled with managing a paper trail of documents. The retirement of two 20+ year veterans further complicated matters, leading to issues with process control and onboarding new employees. Copps Industries needed a solution that would tighten process control, scale with its business, and centralize information for easy access.
Case Study
Advantech Industry 4.0 Solutions, Excellence in Pharmaceutical Manufacturing
União Química, one of the biggest players in Brazil’s burgeoning pharmaceutical industry, was being held back by its reliance on outdated production methods. The firm’s managers found their production lines hampered by a low productivity and a lack of efficient quality monitoring, as well as a lack of remote connectivity enabling easy access to critical production line data. One key distinguishing feature in drug manufacturing is the necessity of carefully documenting each step of the production process for compliance. These strict requirements led pharmaceutical manufacturers to store production information in paper records for future reference, but this approach also made it difficult for production managers to make process improvements.
Case Study
Mirriad Delivers Next-Generation Ad Tech Using AWS
Mirriad, a London-based company, delivers next-generation advertising solutions by using its computer vision technology to naturally place brands in premium video content across TV, online, and mobile channels. The challenge for Mirriad was achieving this intelligent insertion of ads at scale. The company was initially using physical data centers, which proved to be a bottleneck when it came to onboarding big businesses. In addition to fast access to compute capacity, another vital requirement for the company was the ability to use NVIDIA GPUs across multiple regions worldwide.
Case Study
SimData Manager: Centralizing and Standardizing CAE Data for Global Collaboration
The case study highlights three main challenges faced by companies in managing their Computer-Aided Engineering (CAE) data. The first challenge is the need for a central location where all CAE users can manage their data within an enterprise for easy retrieval and full traceability from CAD to CAE, and all versions of CAE to the final report. The second challenge is the lack of standardization in methods used by different engineers, the loss of knowledge when employees leave, and the manual nature of the processes. The third challenge is the difficulty in tracking versions of CAD and CAE models and distributing project data globally, especially for companies with multiple development organizations in different geographic locations.