Download PDF
Gestamp Information Running Smoothly Due to QlikView
Technology Category
- Analytics & Modeling - Data-as-a-Service
Applicable Industries
- Automotive
Applicable Functions
- Discrete Manufacturing
- Procurement
Use Cases
- Manufacturing System Automation
- Supply Chain Visibility
Services
- Data Science Services
The Challenge
Gestamp Automoción, an international group dealing in the development and manufacture of components and metal assemblies for motor vehicles, was facing a challenge with its data management. The company had a large amount of information, a large number of users, and disparate, international information coming from eight different enterprise resource planning systems (ERPs) across its production plants. The information wasn’t unified and there was no way to achieve this automatically with the legacy system. Reports were prepared using macros and in presentations or spreadsheets. Gestamp Automoción needed a complete, efficient reporting system. The company was looking for an application to complete its FULLSTEP GS purchasing platform and integrate information from that platform with data from the company’s various ERPs.
About The Customer
Gestamp Automoción in Spain is an international group dealing in the development and manufacture of components and metal assemblies for motor vehicles. Gestamp Automoción and Grupo Gonvarri, specialising in flat steel service centre activities since the end of the 1950s, constitute the two main lines of business of the Gestamp Corporation. Today Gestamp Automoción based in Abadino, Spain, has a presence in 18 countries, with 57 production plants, and 13 research and development centres employing a total of more than 13,500 people. Its principal customers are the major automotive industry manufacturers including companies such as Volkswagen, Renault-Nissan, Peugeot-Citroen, Daimler, GM, Ford, and Chrysler. Gestamp Automoción has invested in high calibre staff committed to providing its customers with products that ensure weight and pollution reduction in motor vehicles, together with safety improvements for both automobiles and passengers.
The Solution
Gestamp Automoción decided to implement QlikView to unify its information. The deployment began in 2007, starting with a scorecard for the purchasing department. Following its success, it was decided to deploy QlikView in other business units: the human resources department in 2008 to monitor travel expenses as well as telephone use. And in 2009, it was extended to the quality control department for incident control. QlikView Server was deployed, providing instant access to information from anywhere in the world for any authorised user. And the “zero footprint” and Windows client were selected to provide access for anyone in the company with only the need for occasional use of the system. The Multi-idioma (multi-language), MultiERP, and MultiDivisa (multi-currency) functions that Sand implemented in the QlikView scorecard was of great benefit to the company.
Operational Impact
Quantitative Benefit
Related Case Studies.
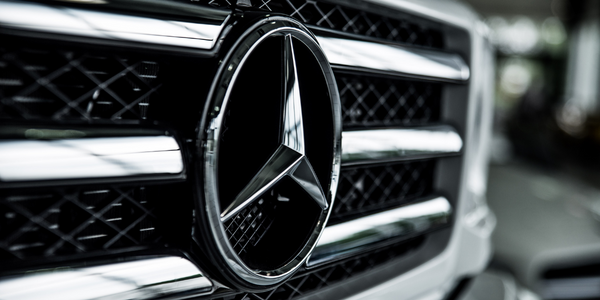
Case Study
Integral Plant Maintenance
Mercedes-Benz and his partner GAZ chose Siemens to be its maintenance partner at a new engine plant in Yaroslavl, Russia. The new plant offers a capacity to manufacture diesel engines for the Russian market, for locally produced Sprinter Classic. In addition to engines for the local market, the Yaroslavl plant will also produce spare parts. Mercedes-Benz Russia and his partner needed a service partner in order to ensure the operation of these lines in a maintenance partnership arrangement. The challenges included coordinating the entire maintenance management operation, in particular inspections, corrective and predictive maintenance activities, and the optimizing spare parts management. Siemens developed a customized maintenance solution that includes all electronic and mechanical maintenance activities (Integral Plant Maintenance).
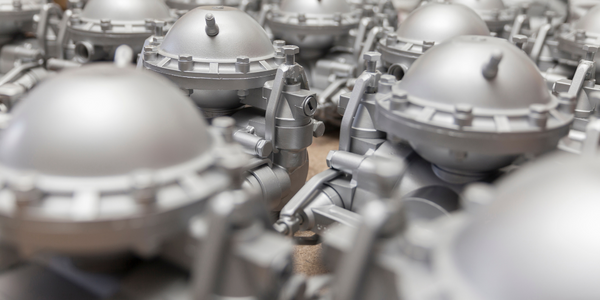
Case Study
Monitoring of Pressure Pumps in Automotive Industry
A large German/American producer of auto parts uses high-pressure pumps to deburr machined parts as a part of its production and quality check process. They decided to monitor these pumps to make sure they work properly and that they can see any indications leading to a potential failure before it affects their process.