Download PDF
Helping A Major Auto Manufacturer Improve On-Time Delivery to the Just-In-Time Assembly Line
Technology Category
- Analytics & Modeling - Predictive Analytics
- Functional Applications - Fleet Management Systems (FMS)
- Sensors - GPS
Applicable Industries
- Automotive
- Transportation
Applicable Functions
- Logistics & Transportation
Use Cases
- Fleet Management
- Predictive Maintenance
- Track & Trace of Assets
Services
- System Integration
- Training
The Challenge
Averitt Express, a leading provider of freight transportation and supply chain management, was tasked with ensuring precise, on-time delivery of an automotive component to a specific point in a car manufacturer's just-in-time assembly line. The challenge was to maintain high accuracy and visibility for multiple daily runs between the component manufacturer’s facility and the assembly line. Inaccurate or delayed tracking data could disrupt the supply chain and impact Averitt’s ability to meet customer commitments.
About The Customer
Averitt Express is a prominent freight transportation and supply chain management company with a global reach extending to over 100 countries. The company is driven by values that emphasize continuous improvement and exceeding customer expectations. Averitt has a long-standing relationship with a leading car manufacturer, which relies on Averitt for the precise, on-time delivery of automotive components to its just-in-time assembly line. This partnership underscores Averitt's commitment to delivering high-quality service and maintaining strong customer relationships.
The Solution
Averitt partnered with FourKites to enhance visibility and ensure precise delivery. FourKites' platform was the only solution capable of recognizing each run as a separate load, which was crucial for Averitt's operations. The platform's advanced geofencing capabilities allowed for precise tracking to specific locations within the assembly line, rather than just a central loading dock. FourKites' product team quickly understood Averitt's needs and demonstrated superior functionality. They used a proven integration process and dedicated onboarding team to seamlessly bring Averitt’s loads onto the platform. Additionally, FourKites provided training to ensure Averitt’s teams could operate the platform autonomously.
Operational Impact
Quantitative Benefit
Related Case Studies.
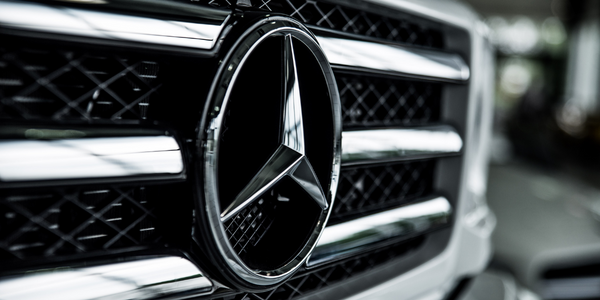
Case Study
Integral Plant Maintenance
Mercedes-Benz and his partner GAZ chose Siemens to be its maintenance partner at a new engine plant in Yaroslavl, Russia. The new plant offers a capacity to manufacture diesel engines for the Russian market, for locally produced Sprinter Classic. In addition to engines for the local market, the Yaroslavl plant will also produce spare parts. Mercedes-Benz Russia and his partner needed a service partner in order to ensure the operation of these lines in a maintenance partnership arrangement. The challenges included coordinating the entire maintenance management operation, in particular inspections, corrective and predictive maintenance activities, and the optimizing spare parts management. Siemens developed a customized maintenance solution that includes all electronic and mechanical maintenance activities (Integral Plant Maintenance).
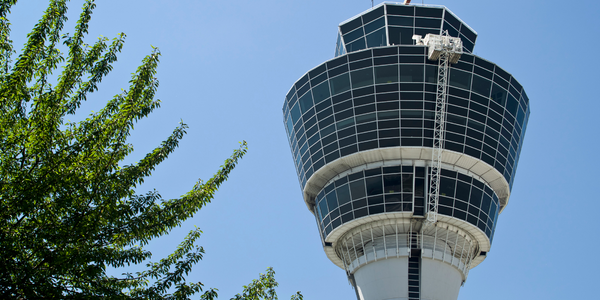
Case Study
Airport SCADA Systems Improve Service Levels
Modern airports are one of the busiest environments on Earth and rely on process automation equipment to ensure service operators achieve their KPIs. Increasingly airport SCADA systems are being used to control all aspects of the operation and associated facilities. This is because unplanned system downtime can cost dearly, both in terms of reduced revenues and the associated loss of customer satisfaction due to inevitable travel inconvenience and disruption.
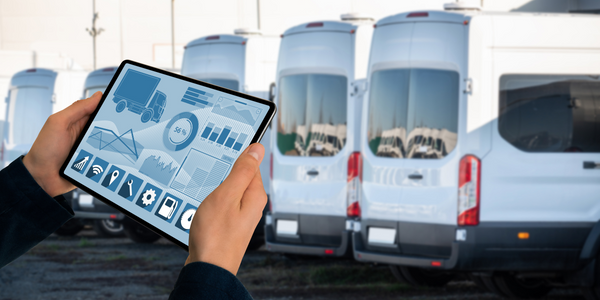
Case Study
IoT-based Fleet Intelligence Innovation
Speed to market is precious for DRVR, a rapidly growing start-up company. With a business model dependent on reliable mobile data, managers were spending their lives trying to negotiate data roaming deals with mobile network operators in different countries. And, even then, service quality was a constant concern.
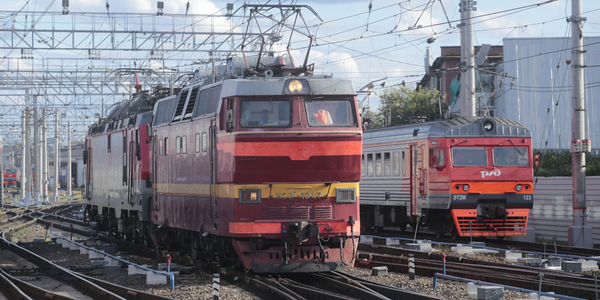
Case Study
Digitize Railway with Deutsche Bahn
To reduce maintenance costs and delay-causing failures for Deutsche Bahn. They need manual measurements by a position measurement system based on custom-made MEMS sensor clusters, which allow autonomous and continuous monitoring with wireless data transmission and long battery. They were looking for data pre-processing solution in the sensor and machine learning algorithms in the cloud so as to detect critical wear.