Download PDF
HyperWorks Application for Global Engineering Design Instruction at Brigham Young University
Technology Category
- Robots - Autonomous Guided Vehicles (AGV)
- Robots - Collaborative Robots
Applicable Industries
- Automotive
- Education
Applicable Functions
- Product Research & Development
Use Cases
- Manufacturing Process Simulation
- Vehicle Performance Monitoring
Services
- Hardware Design & Engineering Services
- Training
The Challenge
The Department of Mechanical Engineering at Brigham Young University (BYU) was faced with the challenge of reworking an advanced engineering design course, ME 471, which had been taught for over 30 years. The course, which consisted of classroom and laboratory components, emphasized theoretical concepts and practical CAE skills. The objective for reworking the course was to add the ability to network design projects so that term projects could be completed collaboratively by teams from various global engineering universities. The main challenge in course networking was to globalize the student learning experience by adding intercultural competency requirements. These included providing experience with working in or directing a team of ethnic or cultural diversity, understanding cultural influences on product design and manufacturing, and comprehending how cultural differences affect how engineering tasks are performed.
About The Customer
The Department of Mechanical Engineering at Brigham Young University (BYU) places a strong emphasis on educating mechanical engineering students to become leaders in applying advanced design techniques to develop new and innovative products. A key component of the department curriculum to meet these objectives is providing instruction that focuses on principles and procedures of multi-physical computer-aided-engineering (CAE). Dr. Greg Jensen, Fulton College Professor of Global Engineering, has led the department to develop innovative CAE instruction. His work has focused on the development of next generation, multi-user, collaborative cloud-based CAE tools and methods. Today a critical success factor for industrial product development is the ability of international companies to collaborate and communicate with a large network of technology providers, inventors, vendors, and manufacturers worldwide.
The Solution
The ME 471 course was globalized by forming international teams representing universities that were members of the PACE (Partners for the Advancement of Collaborative Engineering Education) Program. The course was modified by integrating new technologies (HyperWorks, Teamcenter Community, Google Docs, Video Conferencing Hardware) to support the work of the virtual student teams. New laboratory exercises were also developed to teach the new virtual collaboration technologies and design simulation methods. In addition to the course modifications, logistical infrastructure upgrades at BYU and partner universities were also completed. These included integration of classroom, CAE lab, and team meeting room video conferencing hardware. A term project assignment given to each team consisted of the architecture/chassis of an actual vehicle, which the team was directed re-design. Project tasks included CAD/CAE modeling of all vehicle components, subsystems, and final assembly based on the team engineering analysis.
Operational Impact
Quantitative Benefit
Related Case Studies.
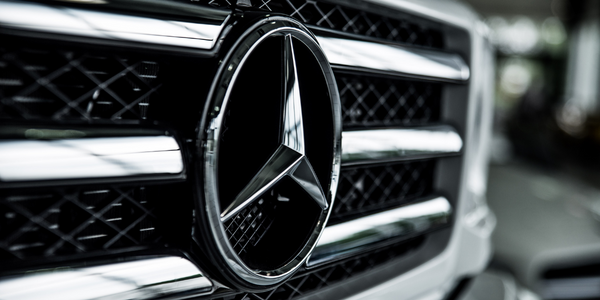
Case Study
Integral Plant Maintenance
Mercedes-Benz and his partner GAZ chose Siemens to be its maintenance partner at a new engine plant in Yaroslavl, Russia. The new plant offers a capacity to manufacture diesel engines for the Russian market, for locally produced Sprinter Classic. In addition to engines for the local market, the Yaroslavl plant will also produce spare parts. Mercedes-Benz Russia and his partner needed a service partner in order to ensure the operation of these lines in a maintenance partnership arrangement. The challenges included coordinating the entire maintenance management operation, in particular inspections, corrective and predictive maintenance activities, and the optimizing spare parts management. Siemens developed a customized maintenance solution that includes all electronic and mechanical maintenance activities (Integral Plant Maintenance).
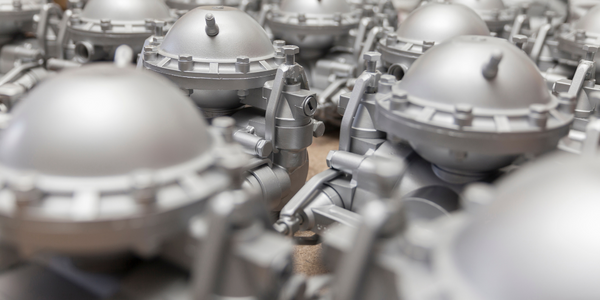
Case Study
Monitoring of Pressure Pumps in Automotive Industry
A large German/American producer of auto parts uses high-pressure pumps to deburr machined parts as a part of its production and quality check process. They decided to monitor these pumps to make sure they work properly and that they can see any indications leading to a potential failure before it affects their process.