Download PDF
HyperWorks' Impact on Subsea Oil and Gas Industry: A Duco Case Study
Technology Category
- Sensors - Haptic Sensors
- Sensors - Utility Meters
Applicable Industries
- Buildings
- Equipment & Machinery
Applicable Functions
- Product Research & Development
- Quality Assurance
Use Cases
- Mesh Networks
- Visual Quality Detection
Services
- Testing & Certification
The Challenge
Duco, a major subsea engineering design, manufacturing, and testing facility, faced significant challenges in improving their Computer-Aided Engineering (CAE) model generation and analysis procedures for their bespoke products. These products, known as subsea 'umbilicals', are complex structures designed to withstand extreme pressure, temperature conditions, and adverse weather in hydrocarbon fields at water depths beyond 3,000 meters. The umbilicals connect the topside platform or vessel with seabed equipment, including pumping stations with electricity and hydraulic pressure. Duco's challenge was to speed up the analysis time for these structures, which had to endure demanding fatigue load cases. They were also experiencing issues with mesh quality with their incumbent pre-processor, prompting the need for a change.
About The Customer
Duco is a part of the Technip Group and is a significant player in the subsea engineering design, manufacturing, and testing industry. Duco's engineers are tasked with developing equipment capable of withstanding the extreme pressure and temperature conditions of hydrocarbon fields at water depths beyond 3,000 meters. The company primarily focuses on designing subsea 'umbilicals' that connect the topside platform or vessel and equipment installed on the seabed, including pumping stations with electricity and hydraulic pressure.
The Solution
Duco chose HyperMesh, a pre-processor from HyperWorks, as their mesh generation tool to address their challenges. HyperMesh allowed Duco to significantly improve their models by providing direct control of the mesh output and enabling continuous mesh quality checks to ensure consistency throughout the model. The tool proved faster than Duco's incumbent tool in model generation and allowed the use of model symmetry. This meant that only a section of the umbilical required manual meshing, which could then be propagated across the entire model. Custom scripts even facilitated automatic meshing and extrusion of the spiraling internal cabling. Furthermore, HyperWorks' commitment to an open architecture ensured that the output files were fully compatible with Duco's existing solver codes.
Operational Impact
Quantitative Benefit
Related Case Studies.
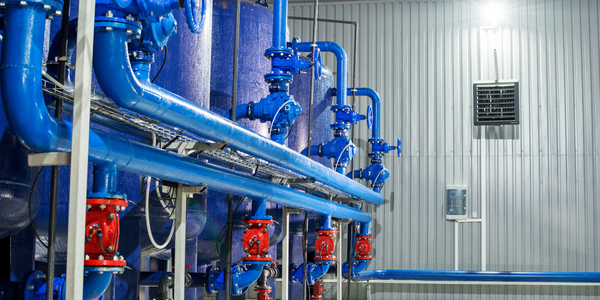
Case Study
Smart Water Filtration Systems
Before working with Ayla Networks, Ozner was already using cloud connectivity to identify and solve water-filtration system malfunctions as well as to monitor filter cartridges for replacements.But, in June 2015, Ozner executives talked with Ayla about how the company might further improve its water systems with IoT technology. They liked what they heard from Ayla, but the executives needed to be sure that Ayla’s Agile IoT Platform provided the security and reliability Ozner required.
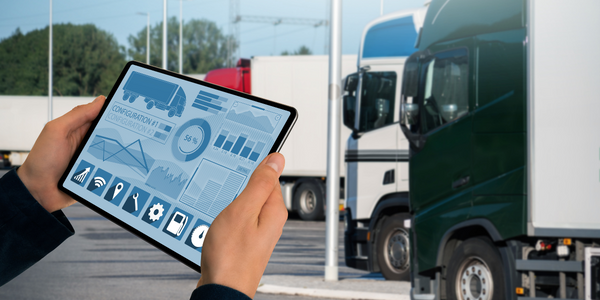
Case Study
IoT enabled Fleet Management with MindSphere
In view of growing competition, Gämmerler had a strong need to remain competitive via process optimization, reliability and gentle handling of printed products, even at highest press speeds. In addition, a digitalization initiative also included developing a key differentiation via data-driven services offers.
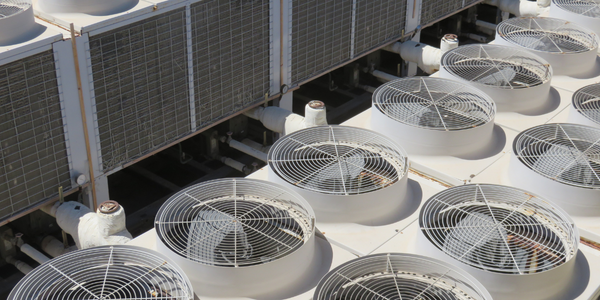
Case Study
Predictive Maintenance for Industrial Chillers
For global leaders in the industrial chiller manufacturing, reliability of the entire production process is of the utmost importance. Chillers are refrigeration systems that produce ice water to provide cooling for a process or industrial application. One of those leaders sought a way to respond to asset performance issues, even before they occur. The intelligence to guarantee maximum reliability of cooling devices is embedded (pre-alarming). A pre-alarming phase means that the cooling device still works, but symptoms may appear, telling manufacturers that a failure is likely to occur in the near future. Chillers who are not internet connected at that moment, provide little insight in this pre-alarming phase.
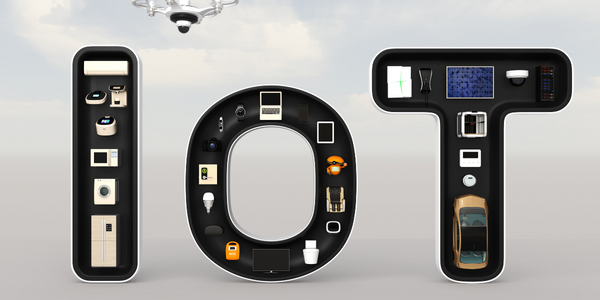
Case Study
Premium Appliance Producer Innovates with Internet of Everything
Sub-Zero faced the largest product launch in the company’s history:It wanted to launch 60 new products as scheduled while simultaneously opening a new “greenfield” production facility, yet still adhering to stringent quality requirements and manage issues from new supply-chain partners. A the same time, it wanted to increase staff productivity time and collaboration while reducing travel and costs.
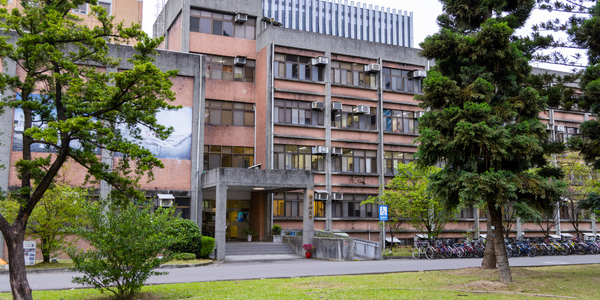
Case Study
Energy Saving & Power Monitoring System
Recently a university in Taiwan was experiencing dramatic power usage increases due to its growing number of campus buildings and students. Aiming to analyze their power consumption and increase their power efficiency across 52 buildings, the university wanted to build a power management system utilizing web-based hardware and software. With these goals in mind, they contacted Advantech to help them develop their system and provide them with the means to save energy in the years to come.
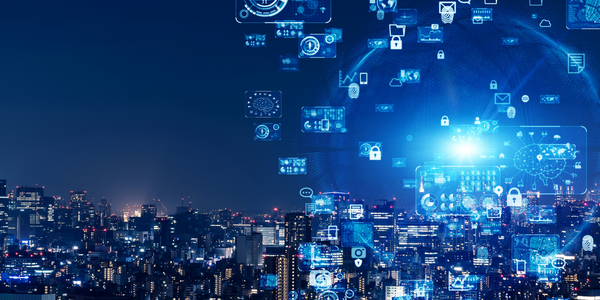
Case Study
Integration of PLC with IoT for Bosch Rexroth
The application arises from the need to monitor and anticipate the problems of one or more machines managed by a PLC. These problems, often resulting from the accumulation over time of small discrepancies, require, when they occur, ex post technical operations maintenance.