Download PDF
Hyundai Mobis Leverages Feko for Enhanced EMC Analysis and Shielding Effectiveness Simulation
Technology Category
- Processors & Edge Intelligence - Microcontrollers & Printed Circuit Boards
- Sensors - Level Sensors
Applicable Industries
- Automotive
- Life Sciences
Applicable Functions
- Product Research & Development
Use Cases
- Virtual Prototyping & Product Testing
- Virtual Reality
Services
- Hardware Design & Engineering Services
- System Integration
The Challenge
Hyundai MOBIS, a leading producer of core automotive components, was facing challenges in improving the efficiency and reducing the time taken in the electromagnetic compatibility (EMC) analysis process. The company uses shielding enclosures to protect against external fields and electromagnetic (EM) leakage from electronic products. However, the integrity of these enclosures was often compromised by apertures and slots used for visibility, ventilation, or access to interior components. These openings allowed exterior electric and magnetic fields to penetrate into the interior space, where they could couple to Printed Circuit Boards (PCBs), inducing currents and voltages on interior conductors. Therefore, it was crucial for Hyundai MOBIS to understand the EM shielding effectiveness of shielding enclosures in the presence of these apertures.
About The Customer
Hyundai MOBIS is a key affiliate of Hyundai Motor Group, specializing in the production of core automotive components. The company's extensive product range includes modules (chassis, cockpit, front-end-modules) and numerous automotive parts designed for customer convenience and safety. While Hyundai and Kia companies are the primary recipients of Hyundai MOBIS's modules, the company is also expanding its business to other auto manufacturers globally. Hyundai MOBIS is committed to developing new ultra-light materials to meet requirements for better fuel efficiency, performance, product appeal, reliability, and sustainability.
The Solution
Hyundai MOBIS adopted a comprehensive approach to address the problem, analyzing it from a PCB level to a system level, including the shielding effectiveness for the current design of the Around View Monitor (AVM) housing. At the PCB level, simulations related to signal and power integrity were conducted once the AVM PCB design was available. The analysis of resonances, impedances, characteristic impedances, simultaneous switching noise, and DC IR drops helped identify power issues. Solutions were adopted to fix these issues to meet the required standards and regulations. Some of the solutions involved changing the value of capacitors or altering the structures of the ground planes to reduce loop inductances. A system level analysis was also carried out using FEKO® to analyze the effect of the material of the AVM housing on its shielding effectiveness. The workflow involved importing the near fields around the board into FEKO, creating an equivalent source for the PCB, and performing a 3D analysis and simulation of the shielding factor of the housing used for the AVM.
Operational Impact
Quantitative Benefit
Related Case Studies.
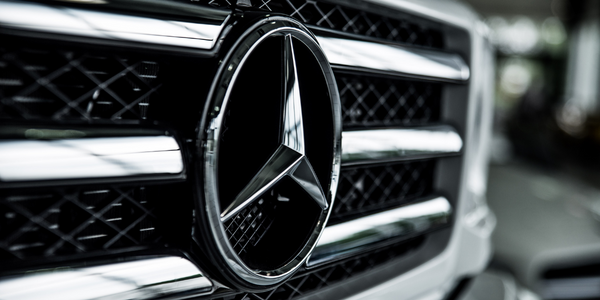
Case Study
Integral Plant Maintenance
Mercedes-Benz and his partner GAZ chose Siemens to be its maintenance partner at a new engine plant in Yaroslavl, Russia. The new plant offers a capacity to manufacture diesel engines for the Russian market, for locally produced Sprinter Classic. In addition to engines for the local market, the Yaroslavl plant will also produce spare parts. Mercedes-Benz Russia and his partner needed a service partner in order to ensure the operation of these lines in a maintenance partnership arrangement. The challenges included coordinating the entire maintenance management operation, in particular inspections, corrective and predictive maintenance activities, and the optimizing spare parts management. Siemens developed a customized maintenance solution that includes all electronic and mechanical maintenance activities (Integral Plant Maintenance).
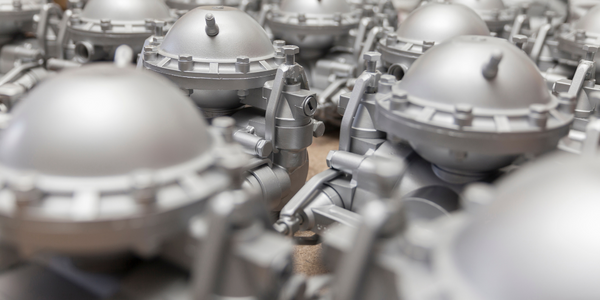
Case Study
Monitoring of Pressure Pumps in Automotive Industry
A large German/American producer of auto parts uses high-pressure pumps to deburr machined parts as a part of its production and quality check process. They decided to monitor these pumps to make sure they work properly and that they can see any indications leading to a potential failure before it affects their process.