IIC Condition Monitoring & Predictive Maintenance Testbed
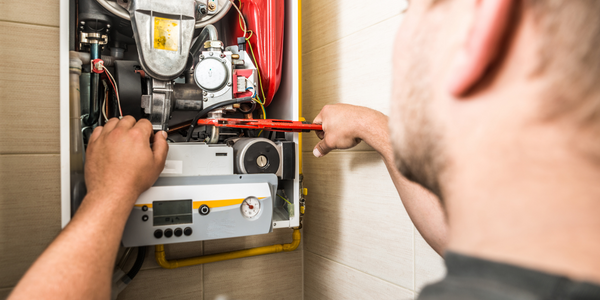
- Analytics & Modeling - Predictive Analytics
- Analytics & Modeling - Real Time Analytics
- Infrastructure as a Service (IaaS)
- Equipment & Machinery
- Discrete Manufacturing
- Predictive Maintenance
The current state of condition monitoring requires manual measurements that are compounded with aging equipment and the retirement of knowledgeable personnel.
*This is an IIC testbed currently in progress.* SUPPORTING MEMBERS IBM, National Instruments, SparkCognition SOLUTION Provide a multi-vendor, cloud-based predictive maintenance solution that proves out new business models. The Condition Monitoring and Predictive Maintenance Testbed will offer continuous online measurements, automated analysis, and balance of plant coverage. TESTBED INTRODUCTION The Condition Monitoring and Predictive Maintenance Testbed (CM/PM) will demonstrate the value and benefits of continuously monitoring industrial equipment to detect early signs of performance degradation or failure. CM/PM will also use modern analytical technologies to allow organizations to not only detect problems but proactively recommend actions for operations and maintenance personnel to correct the problem. Condition Monitoring (CM) is the use of sensors in equipment to gather data and enable users to centrally monitor the data in real-time. Predictive Maintenance (PM) applies analytical models and rules against the data to proactively predict an impending issue; then deliver recommendations to operations, maintenance and IT departments to address the issue. These capabilities enable new ways to monitor the operation of the equipment - such as turbines and generators - and processes and to adopt proactive maintenance and repair procedures rather than fixed schedule-based procedures, potentially saving money on maintenance and repair, and saving cost and lost productivity of downtime caused by equipment failures. Furthermore, combining sensor data from multiple pieces of equipment and/or multiple processes can provide deeper insight into the overall impact of faulty or sub-optimal equipment, allowing organizations to identify and resolve problems before they impact operations and improve the quality and efficiency of industrial processes. Through this testbed, the testbed leaders IBM and National Instruments will explore the application of a variety of analytics technologies for condition monitoring and predictive maintenance. The testbed application will initially be deployed to a power plant facility where performance and progress will be reported on, additional energy equipment will be added and new models will be developed. It will then be expanded to adjacent, as yet to be determined, industries.
Related Case Studies.
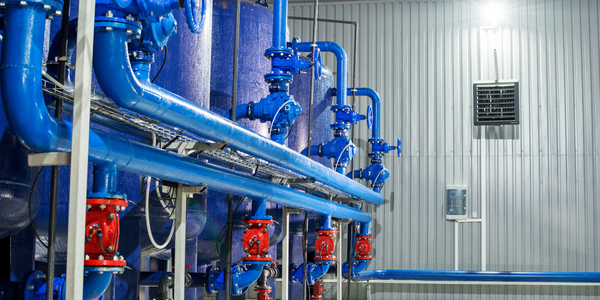
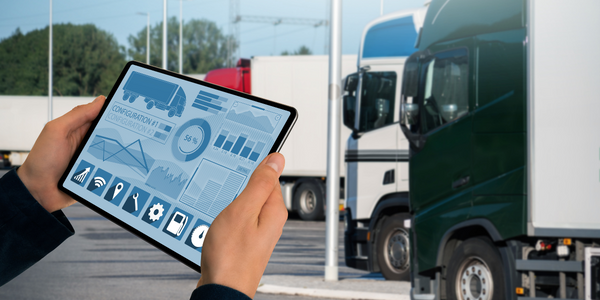
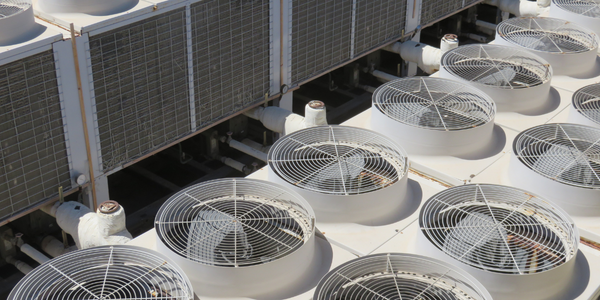
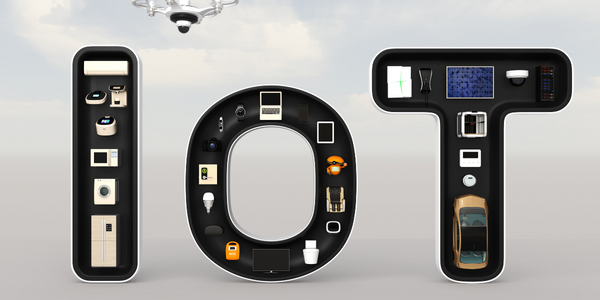
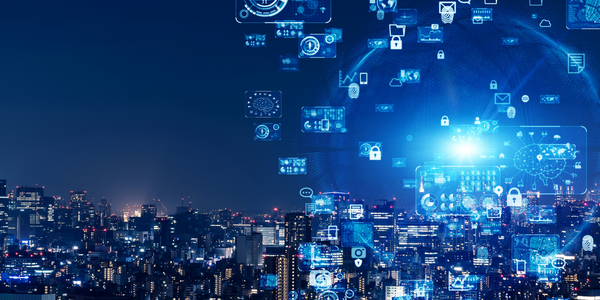
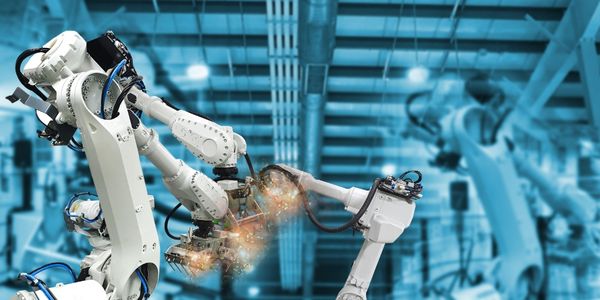