Download PDF
Improving Crash Simulations with High-Performance Computing: A Case Study of PSA Peugeot Citroën
Technology Category
- Analytics & Modeling - Digital Twin / Simulation
- Analytics & Modeling - Predictive Analytics
Applicable Industries
- Automotive
- Life Sciences
Applicable Functions
- Product Research & Development
- Sales & Marketing
Use Cases
- Digital Twin
- Virtual Reality
Services
- System Integration
- Testing & Certification
The Challenge
PSA Peugeot Citroën, the second largest carmaker in Europe, faced a significant challenge in meeting increasingly stringent automotive regulations that demanded lower CO2 emission levels. This required the carmaker to decrease the design structure mass by using materials with a higher strength-to-weight ratio. However, introducing new materials into the design process was complex; design rules and numerical tools had to evolve to understand the characteristics of these materials and evaluate potential failures. There was a risk of delaying production awaiting reliable design direction from simulation, or having to redesign a part late in the design cycle. Furthermore, due to the large, nonlinear deformations involved in simulating crash or rupture events, proper material failure criteria were essential to results accuracy. To improve its knowledge in assessing predictive rupture models, and to identify a viable solution for testing ruptures on a massive scale, PSA collaborated with Altair, Ecole Polytechnique Laboratoire de Mécanique des Solides (LMS) and PRACE.
About The Customer
PSA Peugeot Citroën is the second largest carmaker in Europe, recording sales and revenue of €54 billion in 2013. With its world-renowned brands, DS, Peugeot and Citroën, PSA sold 2.8 million vehicles worldwide in 2013, of which 42% were sold outside Europe. PSA is a European leader in terms of CO2 emissions, with an average of 115.9 grams of CO2/km in 2013. The company has sales operations in 160 countries and is also involved in financing activities (Banque PSA Finance) and automotive equipment (Faurecia).
The Solution
Altair engineers ported RADIOSS, the market-leading analysis solver for crash simulation in Altair’s HyperWorks CAE software suite, to Bullxmpi for the Curie supercomputer allocated to the study. This porting included the optimization of the setup of RADIOSS under Bullxmpi to obtain ideal performance. The efficiency of the solution was evaluated and improved using industrial car crash models ranging from 1 to 10 million elements. Two specific models were developed to study rupture of a B-pillar component with mesh size requirement of 75µm element length. Altair had to optimize the code to handle the large simulation models, especially contact treatments inside the very fine mesh part; the project also required optimizing several I/O treatments. In addition, Altair engineers implemented a specific material law and a rupture model in RADIOSS, which was developed through an “Industrial Fracture Consortium” including MIT, Ecole Polytechnique and industrial partners like PSA.
Operational Impact
Quantitative Benefit
Related Case Studies.
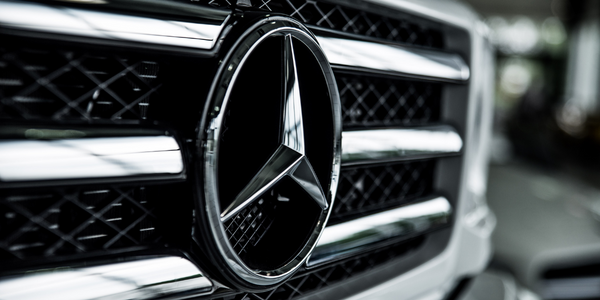
Case Study
Integral Plant Maintenance
Mercedes-Benz and his partner GAZ chose Siemens to be its maintenance partner at a new engine plant in Yaroslavl, Russia. The new plant offers a capacity to manufacture diesel engines for the Russian market, for locally produced Sprinter Classic. In addition to engines for the local market, the Yaroslavl plant will also produce spare parts. Mercedes-Benz Russia and his partner needed a service partner in order to ensure the operation of these lines in a maintenance partnership arrangement. The challenges included coordinating the entire maintenance management operation, in particular inspections, corrective and predictive maintenance activities, and the optimizing spare parts management. Siemens developed a customized maintenance solution that includes all electronic and mechanical maintenance activities (Integral Plant Maintenance).
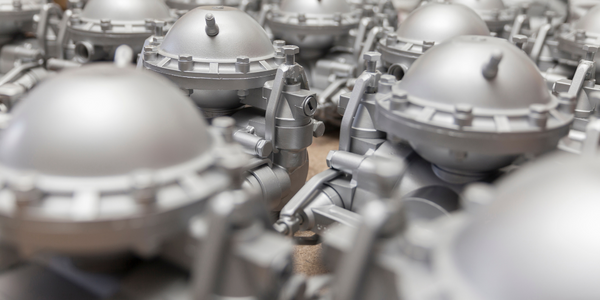
Case Study
Monitoring of Pressure Pumps in Automotive Industry
A large German/American producer of auto parts uses high-pressure pumps to deburr machined parts as a part of its production and quality check process. They decided to monitor these pumps to make sure they work properly and that they can see any indications leading to a potential failure before it affects their process.