Download PDF
Innovative Industrial Design Services by Pininfarina Extra
Technology Category
- Cybersecurity & Privacy - Identity & Authentication Management
Applicable Industries
- Automotive
Applicable Functions
- Product Research & Development
- Quality Assurance
Use Cases
- Virtual Prototyping & Product Testing
- Visual Quality Detection
Services
- Testing & Certification
The Challenge
Pininfarina Extra, a company known for its elegance, essentiality, and innovation in the automotive industry, faced the challenge of extending these values to sectors outside the automotive industry. The company aimed to bring its unique design philosophy to everyday products, focusing on an elegant, essential style that places human needs at the center. The challenge was not only to understand the continuous evolution of modern life but also to interpret different cultures and social paradigms. This required a multicultural and cross-disciplinary team capable of comprehending and adapting to the changing dynamics of the world.
About The Customer
Pininfarina Extra is an industrial design company that uses advanced aspects of scientific and engineering research in combination with the aesthetic dimension seen in everyday products. The company places man and his needs at the center of its design philosophy, which is characterized by an elegant, essential style. Pininfarina Extra employs an international team of designers who work together to comprehend the continuous evolution of modern life and interpret different cultures and social paradigms. The company serves clients of all sizes, from small companies to the world's most prestigious brands.
The Solution
Pininfarina Extra employed a multicultural and cross-disciplinary team and used solidThinking tools to address the challenge. The design process began with a research and analysis phase to define user needs, target market, competition, available resources, and technology. The concept phase followed, where innovative ideas and opportunities were born. The design phase involved defining the idea and turning it into reality through renderings and research activities. The engineering stage defined all parts and components of the object in terms of size and technology. Prototyping was done to check the aesthetics and ergonomics of the product. Finally, a communication strategy was determined for launching the new object onto the market. The use of 3D and high-quality photorealistic rendering helped identify technical issues and present designs to clients.
Operational Impact
Quantitative Benefit
Related Case Studies.
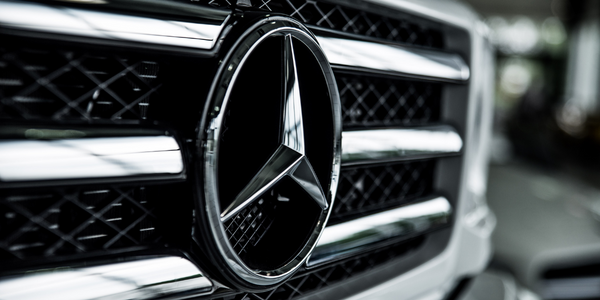
Case Study
Integral Plant Maintenance
Mercedes-Benz and his partner GAZ chose Siemens to be its maintenance partner at a new engine plant in Yaroslavl, Russia. The new plant offers a capacity to manufacture diesel engines for the Russian market, for locally produced Sprinter Classic. In addition to engines for the local market, the Yaroslavl plant will also produce spare parts. Mercedes-Benz Russia and his partner needed a service partner in order to ensure the operation of these lines in a maintenance partnership arrangement. The challenges included coordinating the entire maintenance management operation, in particular inspections, corrective and predictive maintenance activities, and the optimizing spare parts management. Siemens developed a customized maintenance solution that includes all electronic and mechanical maintenance activities (Integral Plant Maintenance).
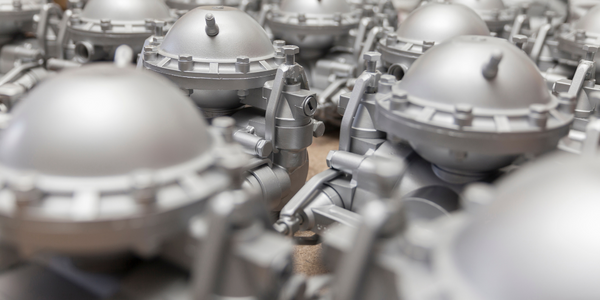
Case Study
Monitoring of Pressure Pumps in Automotive Industry
A large German/American producer of auto parts uses high-pressure pumps to deburr machined parts as a part of its production and quality check process. They decided to monitor these pumps to make sure they work properly and that they can see any indications leading to a potential failure before it affects their process.