Download PDF
Integration Drives Ordering Success for Major Car Manufacturer
Technology Category
- Application Infrastructure & Middleware - API Integration & Management
- Platform as a Service (PaaS) - Connectivity Platforms
Applicable Industries
- Automotive
Applicable Functions
- Sales & Marketing
- Logistics & Transportation
Use Cases
- Supply Chain Visibility
- Inventory Management
Services
- System Integration
The Challenge
The Chinese automobile manufacturer was facing pressure for improved sales forecasting, better manufacturing logistics and after-sales service, and a necessity to centralize data from multiple systems. The company was also dealing with growing customer expectations relating to specifications and services. The company planned to bring in a new Distributor Management System (DMS) to better manage its sales, logistics, and after-sales claims. However, the company faced challenges with data validity and timeliness from distributors. Data was also spread across numerous disparate platforms, creating data management headaches. In March 2017, the company faced the monumental challenge of integrating all of the old DMS’s whopping 744 modules into the new-generation DMS.
About The Customer
The customer is a Chinese automobile manufacturer that operates as a multinational joint venture representing a multi-billion-dollar investment in new, first-class manufacturing facilities in China. The manufacturer boasts a production capacity approaching 2 million cars annually. With adherence to quality in all aspects of the business and a focus on providing customers with the best quality of service, the company has built a modern sales and service network across the country and introduced many innovative features to the delight of its customers.
The Solution
The company decided to use Software AG’s webMethods, a world-leading integration platform for application systems. This solution could simplify complicated multi-module combinations, which was exactly what the business needed. The solution provided smooth resolutions to interface issues and actually started to speed up the development of the company’s DMS platform. The company’s next-generation DMS is now faster and easier for distribution partners to use. After customers submit their orders to a 4S store, the factory begins producing a vehicle to their specifications. Vehicle order information, including color, model, production date and other order details from distributors, can now be accessed and used in real time—enabling the company to reliably deploy order-based production.
Operational Impact
Related Case Studies.
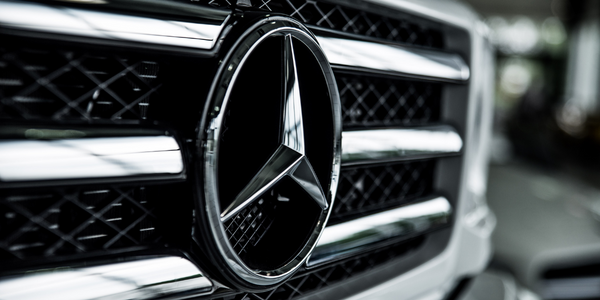
Case Study
Integral Plant Maintenance
Mercedes-Benz and his partner GAZ chose Siemens to be its maintenance partner at a new engine plant in Yaroslavl, Russia. The new plant offers a capacity to manufacture diesel engines for the Russian market, for locally produced Sprinter Classic. In addition to engines for the local market, the Yaroslavl plant will also produce spare parts. Mercedes-Benz Russia and his partner needed a service partner in order to ensure the operation of these lines in a maintenance partnership arrangement. The challenges included coordinating the entire maintenance management operation, in particular inspections, corrective and predictive maintenance activities, and the optimizing spare parts management. Siemens developed a customized maintenance solution that includes all electronic and mechanical maintenance activities (Integral Plant Maintenance).
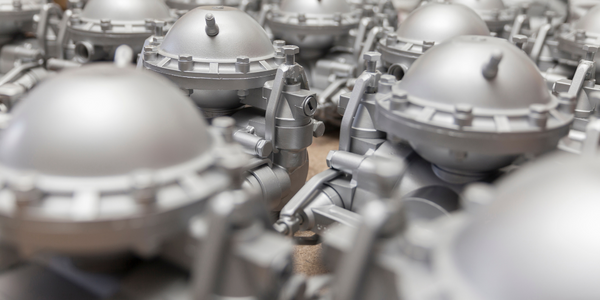
Case Study
Monitoring of Pressure Pumps in Automotive Industry
A large German/American producer of auto parts uses high-pressure pumps to deburr machined parts as a part of its production and quality check process. They decided to monitor these pumps to make sure they work properly and that they can see any indications leading to a potential failure before it affects their process.