Download PDF
Leveraging IoT in Formula SAE Contests: A Case Study of Cal Poly Pomona Formula SAE Team
Technology Category
- Networks & Connectivity - Ethernet
- Sensors - Autonomous Driving Sensors
Applicable Industries
- Automotive
- Life Sciences
Applicable Functions
- Product Research & Development
Use Cases
- Smart Parking
- Vehicle-to-Infrastructure
Services
- Testing & Certification
The Challenge
The Cal Poly Pomona Formula SAE (CPPFSAE) team, a student-run team participating in the Formula SAE® contests, faced a significant challenge in their quest to be among the best in the competition. Each year, the team sought to apply new materials and technologies to improve their race cars. However, the introduction of new materials such as composites created new requirements and design and development challenges. The team's goal was to leverage the advantages of each material, such as lightweight design or stiffness potential, but each material had to be designed individually. A specific challenge arose when the team decided to design and optimize a new wheel shell. They needed a software tool that would allow them to create a composite laminate design. They encountered difficulties in getting the carbon fiber laminate prepreg to conform to their mold, which they attempted to solve by increasing the number of debulking cycles and switching to hot debulk. A post machining process on the wheel was also necessary.
About The Customer
The Cal Poly Pomona Formula SAE (CPPFSAE) team is a student-run team that competes in the Formula SAE, an international collegiate design competition. The competition is one of the largest of its kind worldwide, attracting students from dozens of countries. The CPPFSAE team members invest hundreds of hours in hands-on engineering as they design, build, and test their race car from scratch, all while being full-time students at Cal Poly Pomona. The team interacts with industry professionals and competes against top international teams. With over 20 years of competition experience and more than 30 team members, CPPFSAE is one of the top teams in the world. The experience gained by team members makes them highly sought after employees in many of the world's top automotive companies.
The Solution
The CPPFSAE team chose Altair's HyperWorks suite for the design and development of the new wheel shell. The software offered robust features for designing and analyzing laminates, making it an ideal tool for their project. The team began the design process by creating the geometry in their standard CAD system, which served as a mold. They then imported the CAD model into HyperWorks and generated a surface mesh of the model, including special areas where they planned to use carbon fiber. The team created the laminate on top of the mesh and used the OptiStruct solver to run a finite element analysis. They then varied parameters, layers, and the orientation of the layers based on the results OptiStruct delivered. The team's design optimizations were based on minimizing the number of layers needed to achieve approximately a 10 percent increase in stiffness. HyperWorks allowed them to go straight into manufacturing a virtually final product.
Operational Impact
Quantitative Benefit
Related Case Studies.
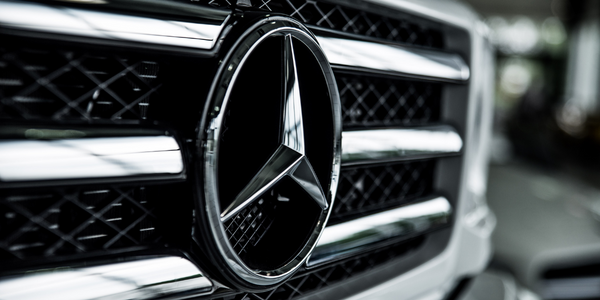
Case Study
Integral Plant Maintenance
Mercedes-Benz and his partner GAZ chose Siemens to be its maintenance partner at a new engine plant in Yaroslavl, Russia. The new plant offers a capacity to manufacture diesel engines for the Russian market, for locally produced Sprinter Classic. In addition to engines for the local market, the Yaroslavl plant will also produce spare parts. Mercedes-Benz Russia and his partner needed a service partner in order to ensure the operation of these lines in a maintenance partnership arrangement. The challenges included coordinating the entire maintenance management operation, in particular inspections, corrective and predictive maintenance activities, and the optimizing spare parts management. Siemens developed a customized maintenance solution that includes all electronic and mechanical maintenance activities (Integral Plant Maintenance).
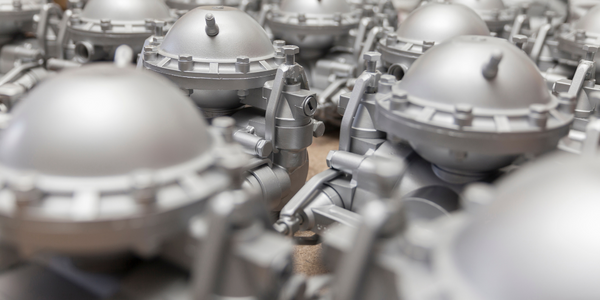
Case Study
Monitoring of Pressure Pumps in Automotive Industry
A large German/American producer of auto parts uses high-pressure pumps to deburr machined parts as a part of its production and quality check process. They decided to monitor these pumps to make sure they work properly and that they can see any indications leading to a potential failure before it affects their process.