Download PDF
Making plants more productive with Cumulocity IoT
Technology Category
- Platform as a Service (PaaS) - Connectivity Platforms
- Analytics & Modeling - Real Time Analytics
Applicable Functions
- Discrete Manufacturing
- Maintenance
Use Cases
- Predictive Maintenance
- Factory Operations Visibility & Intelligence
Services
- System Integration
- Data Science Services
The Challenge
CodeWrights, a German technology company, specializes in integrating devices in industrial manufacturing for its customers. They bridge connections from sensors and actuators used in process automation to higher-level control systems and asset management systems. However, they faced challenges in increasing access to equipment data and analysis through a centralized platform. They wanted to optimize automation using the IoT and offer improved operational efficiency and overall factory health. The company’s deep expertise in writing device drivers lets its customers in industrial manufacturing connect sensors and actuators to pull off incredible feats of automated manufacturing efficiency. But in today’s competitive market, if you only access this basic data from your devices, you’re leaving serious efficiency, and dollars, on the table.
About The Customer
CodeWrights is a German technology company founded in 2002 and is a growing leader of integrating devices in industrial manufacturing for its customers. CodeWrights bridges connections from sensors and actuators used in process automation to higher level control systems, and asset management systems. Its IIoT platform runs applications installed on edge-based gateways accessible via the cloud. The company’s deep expertise in writing device drivers lets its customers in industrial manufacturing connect sensors and actuators to pull off incredible feats of automated manufacturing efficiency.
The Solution
CodeWrights teamed up with Software AG and its Cumulocity IoT platform to unleash a fluid flow of actionable industrial IoT data to CodeWrights’ customers. The new solution autonomously collects everything from device ID, manufacturing date, operational parameters and beyond—driving predictive maintenance, worker safety and the bottom line improvements for large industrial customers. The Cumulocity IoT-powered solution allows CodeWrights’ customers—and their end customers—to manage industrial devices with newly accessible data. Now plant operators can literally see everything about all their connected devices in customizable dashboards on-premises or in the cloud. A gateway running the solution detects devices automatically once it’s installed and configured. No manual steps needed.
Operational Impact
Quantitative Benefit
Related Case Studies.
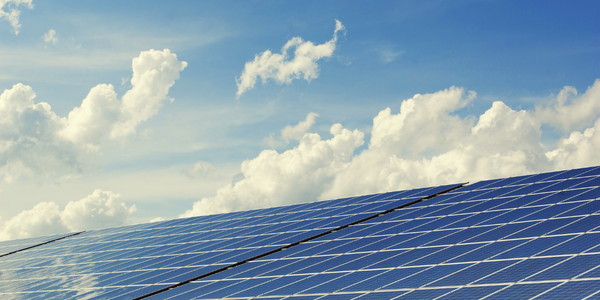
Case Study
Remote Monitoring & Predictive Maintenance App for a Solar Energy System
The maintenance & tracking of various modules was an overhead for the customer due to the huge labor costs involved. Being an advanced solar solutions provider, they wanted to ensure early detection of issues and provide the best-in-class customer experience. Hence they wanted to automate the whole process.
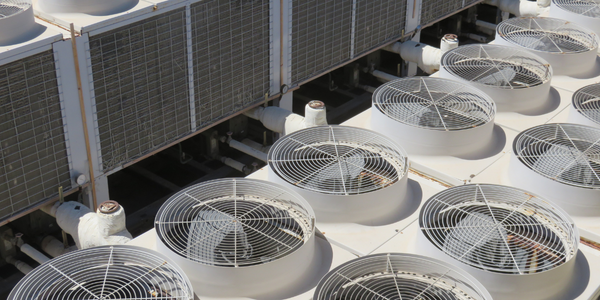
Case Study
Predictive Maintenance for Industrial Chillers
For global leaders in the industrial chiller manufacturing, reliability of the entire production process is of the utmost importance. Chillers are refrigeration systems that produce ice water to provide cooling for a process or industrial application. One of those leaders sought a way to respond to asset performance issues, even before they occur. The intelligence to guarantee maximum reliability of cooling devices is embedded (pre-alarming). A pre-alarming phase means that the cooling device still works, but symptoms may appear, telling manufacturers that a failure is likely to occur in the near future. Chillers who are not internet connected at that moment, provide little insight in this pre-alarming phase.
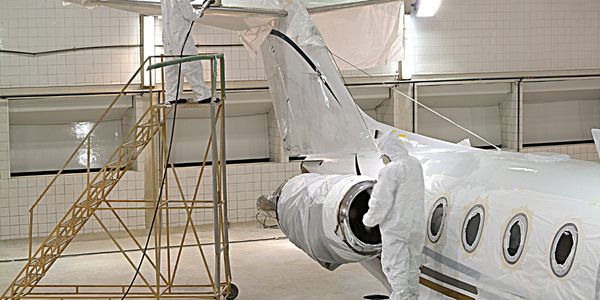
Case Study
Aircraft Predictive Maintenance and Workflow Optimization
First, aircraft manufacturer have trouble monitoring the health of aircraft systems with health prognostics and deliver predictive maintenance insights. Second, aircraft manufacturer wants a solution that can provide an in-context advisory and align job assignments to match technician experience and expertise.
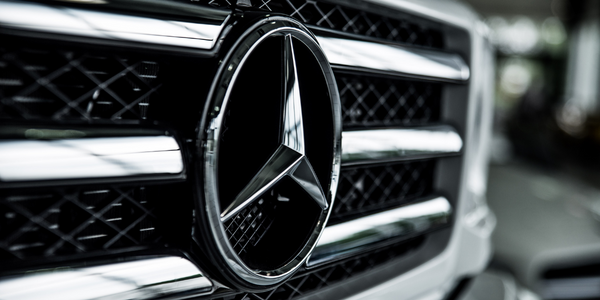
Case Study
Integral Plant Maintenance
Mercedes-Benz and his partner GAZ chose Siemens to be its maintenance partner at a new engine plant in Yaroslavl, Russia. The new plant offers a capacity to manufacture diesel engines for the Russian market, for locally produced Sprinter Classic. In addition to engines for the local market, the Yaroslavl plant will also produce spare parts. Mercedes-Benz Russia and his partner needed a service partner in order to ensure the operation of these lines in a maintenance partnership arrangement. The challenges included coordinating the entire maintenance management operation, in particular inspections, corrective and predictive maintenance activities, and the optimizing spare parts management. Siemens developed a customized maintenance solution that includes all electronic and mechanical maintenance activities (Integral Plant Maintenance).

Case Study
Asset Management and Predictive Maintenance
The customer prides itself on excellent engineering and customer centric philosophy, allowing its customer’s minds to be at ease and not worry about machine failure. They can easily deliver the excellent maintenance services to their customers, but there are some processes that can be automated to deliver less downtime for the customer and more efficient maintenance schedules.