Download PDF
Mario Levi Increases Production and Agility with Lectra
Technology Category
- Functional Applications - Manufacturing Execution Systems (MES)
- Analytics & Modeling - Predictive Analytics
Applicable Industries
- Automotive
Applicable Functions
- Process Manufacturing
- Quality Assurance
Use Cases
- Manufacturing System Automation
- Predictive Maintenance
- Process Control & Optimization
Services
- System Integration
- Training
The Challenge
Mario Levi needed to transform its production processes in order to meet market demands for production flexibility and faster time to market. The productivity levels of their die press system were not sufficient to keep pace with the increase in demand. The die press system required constant monitoring, leading to longer processes and delays in fulfilling orders. The team was looking for a solution to boost productivity, improve material use, and accelerate time to market while being flexible enough to handle growing demand from an expanding market.
About The Customer
Founded in 1946, Mario Levi manufactures and supplies leather components for car interiors. Headquartered in Turin, the automotive capital of Italy, it assists automotive suppliers and car manufacturers as a service provider and partner in product development, from the earliest concept phase to standard mass production. The Group has several operations, in Italy and abroad, to manage all the manufacturing stages, from raw material processing to the finished product. Over the past four years, Mario Levi has experienced a steady increase in the acquisition of new contracts and customers.
The Solution
Based on previous experiences and industry expertise, Lectra was Mario Levi’s first choice once they decided to equip their mass-production plants with automated cutting technology. Integrating Versalis into the production process introduced a major change from the die press system Mario Levi had been using. Lectra experts collaborated with the executive team from Mario Levi to organize its processes around the new solution. The Lectra team worked with Mario Levi to understand their operations, analyze their processes, and identify where improvements could be made. Additionally, Lectra delivered a Lean Manufacturing consulting project to optimize production processes.
Operational Impact
Quantitative Benefit
Related Case Studies.
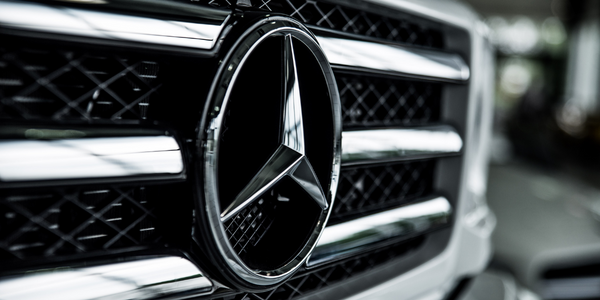
Case Study
Integral Plant Maintenance
Mercedes-Benz and his partner GAZ chose Siemens to be its maintenance partner at a new engine plant in Yaroslavl, Russia. The new plant offers a capacity to manufacture diesel engines for the Russian market, for locally produced Sprinter Classic. In addition to engines for the local market, the Yaroslavl plant will also produce spare parts. Mercedes-Benz Russia and his partner needed a service partner in order to ensure the operation of these lines in a maintenance partnership arrangement. The challenges included coordinating the entire maintenance management operation, in particular inspections, corrective and predictive maintenance activities, and the optimizing spare parts management. Siemens developed a customized maintenance solution that includes all electronic and mechanical maintenance activities (Integral Plant Maintenance).
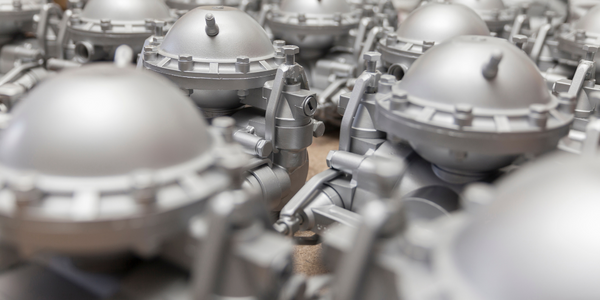
Case Study
Monitoring of Pressure Pumps in Automotive Industry
A large German/American producer of auto parts uses high-pressure pumps to deburr machined parts as a part of its production and quality check process. They decided to monitor these pumps to make sure they work properly and that they can see any indications leading to a potential failure before it affects their process.