Download PDF
Maximizing ROI in Mining Operations with IoT: A Case Study of Los Pelambres Copper Mine

Technology Category
- Networks & Connectivity - Cellular
- Networks & Connectivity - Global Navigation Satellite System (GNSS)
Applicable Industries
- Mining
- Transportation
Applicable Functions
- Logistics & Transportation
- Maintenance
Use Cases
- Tank Level Monitoring
- Vehicle Telematics
Services
- System Integration
The Challenge
Los Pelambres, a copper mine located in Salamanca, Chile, faced a significant challenge in its operations. The mine, which is the seventh largest producer of copper in the world, relied on 55 Komatsu mining trucks for the transportation of copper. In an effort to maximize asset utilization, the mine adopted a fast refueling system that reduced refueling time from 25 to approximately 5 minutes. However, this initiative led to a series of unexpected issues. The factory-installed fuel sensors ruptured due to the pressure from the fast refueling system. Without a working fuel sensor, drivers had to guess when to refuel and how much fuel to add back into the tank. This led to frequent under or overfilling of the tanks, causing operational delays and increased downtime. The mine needed a solution that could withstand the pressure from the fast refueling system, relay fuel level and truck location data back to a centralized application, and include a user-friendly interface for monitoring.
The Customer
Los Pelambres
About The Customer
Los Pelambres is a copper mine located in Salamanca, Chile, and is partly owned by Antofagasta Minerals. The mine is the seventh largest producer of copper in the world and is situated at an elevation of over 3,000 meters above sea level in the Andes Mountains. The mine covers 50 square kilometers of uneven terrain and transports more than 365,000 tons of copper every year. The mine's operations heavily rely on 55 Komatsu mining trucks, which are known for their reliability and are often used in remote and difficult applications.
The Solution
The solution was developed by Tarco LTDA, a Chilean integrator specializing in custom tracking and monitoring solutions for the mining industry. The PCR 1000—Tarco’s state-of-the-art remote fuel monitoring system—constantly monitors tank levels and transmits tank-level data as well as other vehicle telematics data back to a centralized application in real-time using ORBCOMM’s IDP-782 terminal. The IDP-782 transmits data over the cellular network when available and automatically switches to a satellite data service when cellular is down for uninterrupted connectivity. The ruggedized, fuel monitoring system is capable of withstanding extreme environmental conditions. The IDP-782 dual-mode terminal continuously collects, processes, and transmits data from the truck, identifying user-defined thresholds and sending only relevant information over the air to minimize data transmission costs. The PCR 1000 remote fuel monitoring system gives the control center complete visibility into refueling operations and an easy-to-use interface that displays truck location and tank levels in real-time.
Operational Impact
Quantitative Benefit
Related Case Studies.
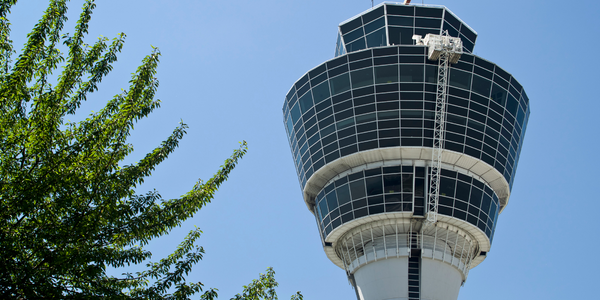
Case Study
Airport SCADA Systems Improve Service Levels
Modern airports are one of the busiest environments on Earth and rely on process automation equipment to ensure service operators achieve their KPIs. Increasingly airport SCADA systems are being used to control all aspects of the operation and associated facilities. This is because unplanned system downtime can cost dearly, both in terms of reduced revenues and the associated loss of customer satisfaction due to inevitable travel inconvenience and disruption.
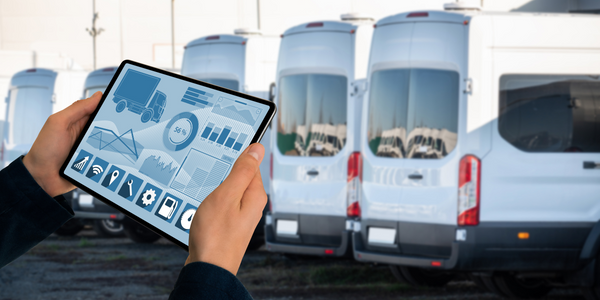
Case Study
IoT-based Fleet Intelligence Innovation
Speed to market is precious for DRVR, a rapidly growing start-up company. With a business model dependent on reliable mobile data, managers were spending their lives trying to negotiate data roaming deals with mobile network operators in different countries. And, even then, service quality was a constant concern.
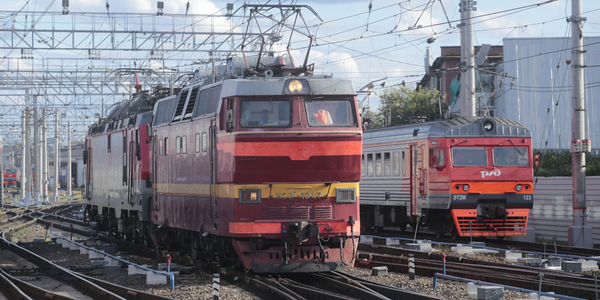
Case Study
Digitize Railway with Deutsche Bahn
To reduce maintenance costs and delay-causing failures for Deutsche Bahn. They need manual measurements by a position measurement system based on custom-made MEMS sensor clusters, which allow autonomous and continuous monitoring with wireless data transmission and long battery. They were looking for data pre-processing solution in the sensor and machine learning algorithms in the cloud so as to detect critical wear.

Case Study
Cold Chain Transportation and Refrigerated Fleet Management System
1) Create a digital connected transportation solution to retrofit cold chain trailers with real-time tracking and controls. 2) Prevent multi-million dollar losses due to theft or spoilage. 3) Deliver a digital chain-of-custody solution for door to door load monitoring and security. 4) Provide a trusted multi-fleet solution in a single application with granular data and access controls.
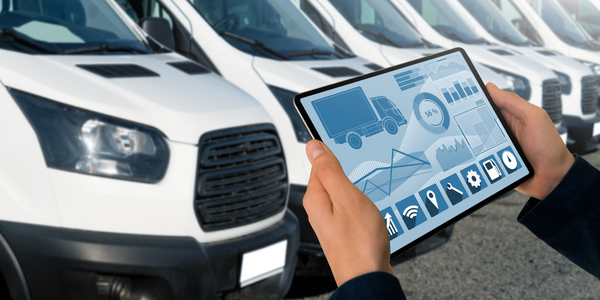
Case Study
Vehicle Fleet Analytics
Organizations frequently implement a maintenance strategy for their fleets of vehicles using a combination of time and usage based maintenance schedules. While effective as a whole, time and usage based schedules do not take into account driving patterns, environmental factors, and sensors currently deployed within the vehicle measuring crank voltage, ignition voltage, and acceleration, all of which have a significant influence on the overall health of the vehicle.In a typical fleet, a large percentage of road calls are related to electrical failure, with battery failure being a common cause. Battery failures result in unmet service agreement levels and costly re-adjustment of scheduled to provide replacement vehicles. To reduce the impact of unplanned maintenance, the transportation logistics company was interested in a trial of C3 Vehicle Fleet Analytics.

Case Study
3M Gains Real-Time Insight with Cloud Solution
The company has a long track record of innovative technology solutions. For example, 3M helps its customers optimize parking operations by automating fee collection and other processes. To improve support for this rapidly expanding segment, 3M needed to automate its own data collection and reporting. The company had recently purchased the assets of parking, tolling, and automatic license plate reader businesses, and required better insight into these acquisitions. Chad Reed, Global Business Manager for 3M Parking Systems, says, “With thousands of installations across the world, we couldn’t keep track of our software and hardware deployments, which made it difficult to understand our market penetration.” 3M wanted a tracking application that sales staff could use to get real-time information about the type and location of 3M products in parking lots and garages. So that it could be used on-site with potential customers, the solution would have to provide access to data anytime, anywhere, and from an array of mobile devices. Jason Fox, Mobile Application Architect at 3M, upped the ante by volunteering to deliver the new app in one weekend. For Fox and his team, these requirements meant turning to the cloud instead of an on-premises datacenter. “My first thought was to go directly to the cloud because we needed to provide access not only to our salespeople, but to resellers who didn’t have access to our internal network,” says Fox. “The cloud just seemed like a logical choice.”