Download PDF
McLaren Racing Leverages IoT for Enhanced Performance and Efficiency
Technology Category
- Analytics & Modeling - Predictive Analytics
- Sensors - Autonomous Driving Sensors
Applicable Industries
- Automotive
- Cement
Applicable Functions
- Product Research & Development
- Quality Assurance
Use Cases
- Smart Parking
- Vehicle-to-Infrastructure
Services
- Testing & Certification
The Challenge
McLaren Racing, a globally recognized sports entity, has a rich heritage of innovation and success in Formula 1 racing. However, with over 20 race weekends in the Formula 1 calendar, each generating 1.5 TB of data, the ability to collect, process, and act on that data is crucial. The challenge was to make data-driven decisions at tremendous speed to improve performance both on and off the track. The team needed to analyze data from 300 telemetry sensors on each race car, generating 100,000 data parameters. Furthermore, the introduction of a strict budget cap of $145M by the governing body for world motor sport, the FIA, added another layer of complexity. The team needed to control operating costs while driving performance enhancements.
About The Customer
McLaren Racing is a globally recognized sports entity with a successful racing heritage. The company has achieved 20 Formula 1 World Championships, 182 Grand Prix victories, and now employs over 800 people. McLaren's success has been driven by a relentless desire to innovate, and they have consistently led the way in the development of groundbreaking technologies. They engage in strategic technology partnerships to improve performance. The team operates in three key verticals: design, build, and race, all of which are completely data-driven. The company is also subject to a strict budget cap enforced by the governing body for world motor sport, the FIA.
The Solution
McLaren Racing turned to the Alteryx Analytics Automation Platform to accelerate strategic decision-making. The platform provided powerful insights across design, build, and race stages, enabling the team to make fast data-led enhancements. It required no prior coding knowledge, allowing teams across the business to use data to make an impact regardless of their coding background. Alteryx automated the collection and processing of varied data sets to accurately track production inventory and performance of parts. It also enabled the team to combine physical, virtual, and race world data to create optimal efficiency and build the most performant race-car possible. Furthermore, the predictive analytics capabilities in Alteryx allowed the team to form a predictive picture on how much attrition they were likely to incur under certain conditions or on certain types of tracks, helping them decide how many spares to manufacture.
Operational Impact
Quantitative Benefit
Related Case Studies.
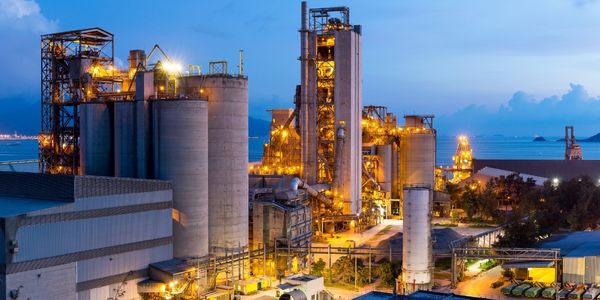
Case Study
System 800xA at Indian Cement Plants
Chettinad Cement recognized that further efficiencies could be achieved in its cement manufacturing process. It looked to investing in comprehensive operational and control technologies to manage and derive productivity and energy efficiency gains from the assets on Line 2, their second plant in India.
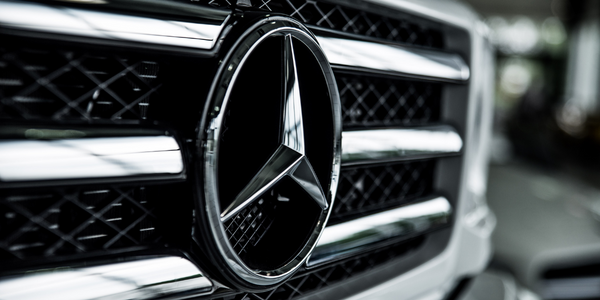
Case Study
Integral Plant Maintenance
Mercedes-Benz and his partner GAZ chose Siemens to be its maintenance partner at a new engine plant in Yaroslavl, Russia. The new plant offers a capacity to manufacture diesel engines for the Russian market, for locally produced Sprinter Classic. In addition to engines for the local market, the Yaroslavl plant will also produce spare parts. Mercedes-Benz Russia and his partner needed a service partner in order to ensure the operation of these lines in a maintenance partnership arrangement. The challenges included coordinating the entire maintenance management operation, in particular inspections, corrective and predictive maintenance activities, and the optimizing spare parts management. Siemens developed a customized maintenance solution that includes all electronic and mechanical maintenance activities (Integral Plant Maintenance).
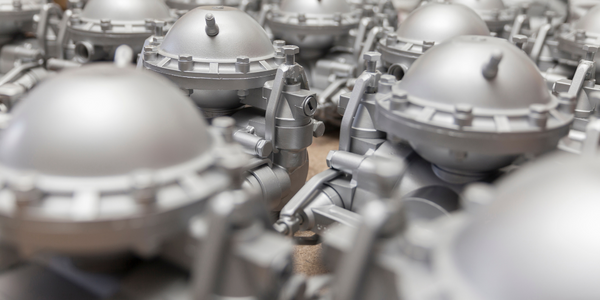
Case Study
Monitoring of Pressure Pumps in Automotive Industry
A large German/American producer of auto parts uses high-pressure pumps to deburr machined parts as a part of its production and quality check process. They decided to monitor these pumps to make sure they work properly and that they can see any indications leading to a potential failure before it affects their process.