Download PDF
Menegotti conquers ISO/TS 16949 using SoftExpert solutions
Technology Category
- Functional Applications - Product Lifecycle Management Systems (PLM)
Applicable Industries
- Automotive
- Metals
Applicable Functions
- Product Research & Development
- Quality Assurance
Use Cases
- Predictive Quality Analytics
- Process Control & Optimization
- Regulatory Compliance Monitoring
Services
- System Integration
- Training
The Challenge
To be a supplier of the automotive segment, the Menegotti Cast Products business unit, also known as MENFUND, required adequate management of its development and sample approval process, before ISO/TS 16949 implementation. The use of APQP-PPAP tools demanded more efficient controls, not fulfilled by manual options, created in Word and Excel tools, requiring excessive time and resources.
About The Customer
Founded in 1940, Menegotti offers an extensive product and service line in cast iron parts for the industry in general. The company operates in more than 40 countries that recognize the quality of the products produced by this company. Menegotti produces cast iron parts for the most diverse applications in industry, standing out for its automotive industry performance, for its agricultural machinery and implements, valves and industrial machinery and equipment components, among others.
The Solution
By adopting the SE APQP-PPAP solution, Menegotti, world leader in the manufacture of machinery and equipment for the building industry as well as manufacturing vehicle parts, has increased the productivity and reliability of its productive processes. This result guaranteed the company's success in gaining ISO/TS 16949. The SoftExpert solution was conceived to fulfill all the requirements described in the APQP-PPAP procedures, created by AIAG, ensuring a structured and automated method for the complete management of product development and alteration processes. The system guarantees a high quality product able to meet deadlines, reduce costs and waste and eliminate failures, through preventive and corrective action plans, while speeding up information documentation as well as data recovery, when necessary.
Operational Impact
Quantitative Benefit
Related Case Studies.
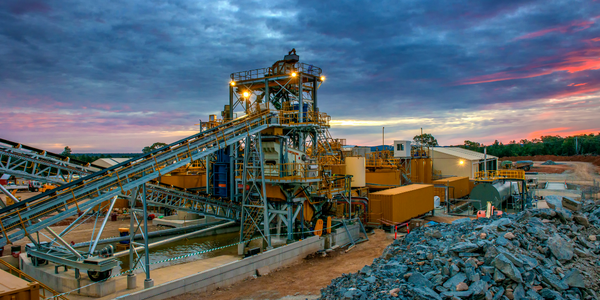
Case Study
Goldcorp: Internet of Things Enables the Mine of the Future
Goldcorp is committed to responsible mining practices and maintaining maximum safety for its workers. At the same time, the firm is constantly exploring ways to improve the efficiency of its operations, extend the life of its assets, and control costs. Goldcorp needed technology that can maximize production efficiency by tracking all mining operations, keep employees safe with remote operations and monitoring of hazardous work areas and control production costs through better asset and site management.
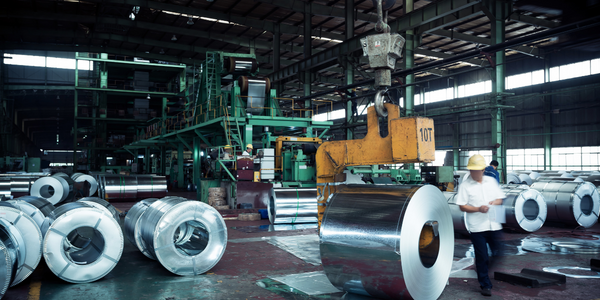
Case Study
KSP Steel Decentralized Control Room
While on-site in Pavlodar, Kazakhstan, the DAQRI team of Business Development and Solutions Architecture personnel worked closely with KSP Steel’s production leadership to understand the steel production process, operational challenges, and worker pain points.
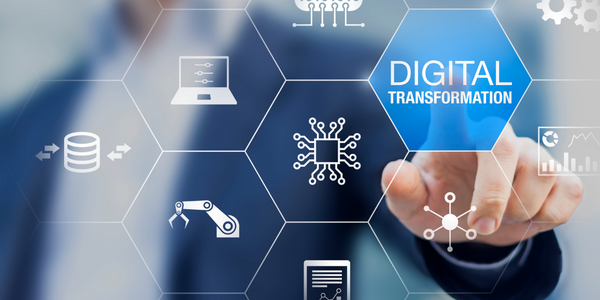
Case Study
Bluescope Steel on Path to Digitally Transform Operations and IT
Increasing competition and fluctuations in the construction market prompted BlueScope Steel to look toward digital transformation of its four businesses, including modern core applications and IT infrastructure. BlueScope needed to modernize its infrastructure and adopt new technologies to improve operations and supply chain efficiency while maintaining and updating an aging application portfolio.
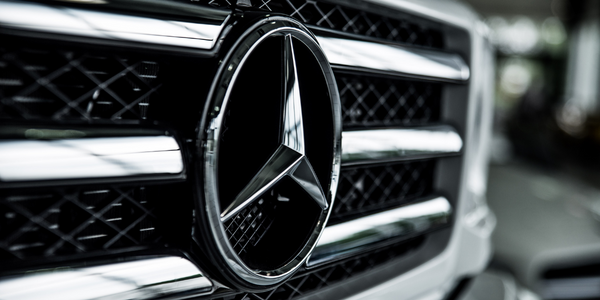
Case Study
Integral Plant Maintenance
Mercedes-Benz and his partner GAZ chose Siemens to be its maintenance partner at a new engine plant in Yaroslavl, Russia. The new plant offers a capacity to manufacture diesel engines for the Russian market, for locally produced Sprinter Classic. In addition to engines for the local market, the Yaroslavl plant will also produce spare parts. Mercedes-Benz Russia and his partner needed a service partner in order to ensure the operation of these lines in a maintenance partnership arrangement. The challenges included coordinating the entire maintenance management operation, in particular inspections, corrective and predictive maintenance activities, and the optimizing spare parts management. Siemens developed a customized maintenance solution that includes all electronic and mechanical maintenance activities (Integral Plant Maintenance).
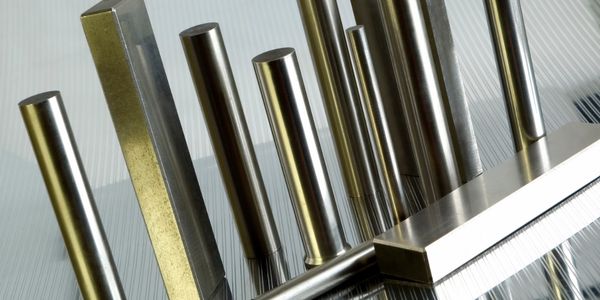
Case Study
RobotStudio Case Study: Benteler Automobiltechnik
Benteler has a small pipe business area for which they produce fuel lines and coolant lines made of aluminum for Porsche and other car manufacturers. One of the problems in production was that when Benteler added new products, production had too much downtime.