Download PDF
Merck KGaA: Cloud-based social business solution used to inspire collaboration and innovation
Technology Category
- Platform as a Service (PaaS) - Connectivity Platforms
Applicable Industries
- Pharmaceuticals
- Chemicals
Applicable Functions
- Product Research & Development
Use Cases
- Collaborative Robotics
- Predictive Maintenance
Services
- Cloud Planning, Design & Implementation Services
The Challenge
Merck KGaA, a global pharmaceutical and chemical company based in Germany, needed to foster innovation to remain competitive. The company needed to capitalize on the collective intelligence of its workforce by uniting the widely distributed and functionally distinct competencies of its employees. The company sought a practical way to energize its personnel to use social business technologies to share observations, knowledge, and expertise.
About The Customer
Founded in 1668 in Darmstadt, Germany, Merck KGaA is the world’s oldest pharmaceutical and chemical company, operating under the Merck brand worldwide except in the United States, where it is known as Emanuel Merck Darmstadt (EMD). The company employs more than 40,000 people in 66 countries and earned revenues of EUR 11.5 billion in 2014. The company is a global leader in the pharmaceutical and chemical industry, with a strong focus on innovation and collaboration.
The Solution
Merck employed a social business solution that enabled it to present a four-day virtual brainstorming event that engaged more than 400 employees enterprise-wide. Invitees joined discussions in four moderated groups that encouraged some of the company’s most forward-thinking employees to engage in dynamic teamwork to become drivers for creating a dynamic source of domain-specific knowledge. The solution supported lively collaboration among 400 participants during more than 80 hours of online discussion and ideation, with a 59 percent participation rate.
Operational Impact
Quantitative Benefit
Related Case Studies.
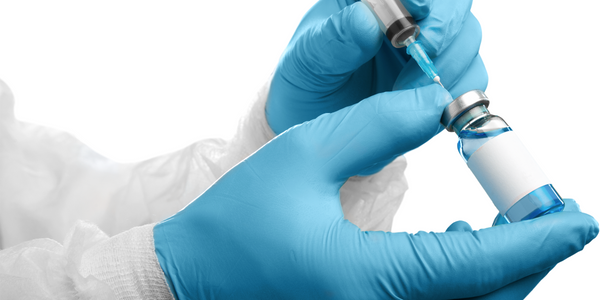
Case Study
Case Study: Pfizer
Pfizer’s high-performance computing software and systems for worldwide research and development support large-scale data analysis, research projects, clinical analytics, and modeling. Pfizer’s computing services are used across the spectrum of research and development efforts, from the deep biological understanding of disease to the design of safe, efficacious therapeutic agents.
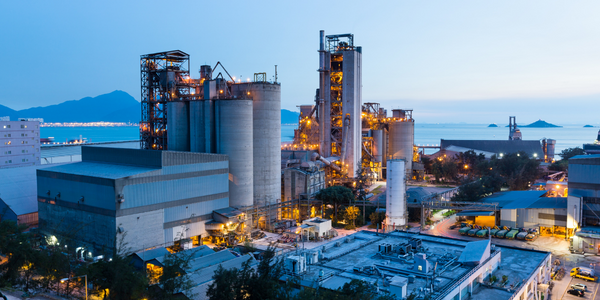
Case Study
Honeywell - Tata Chemicals Improves Data Accessibility with OneWireless
Tata was facing data accessibility challenges in the cement plant control room tapping signals from remote process control areas and other distant locations, including the gas scrubber. Tata needed a wireless solution to extend its control network securely to remote locations that would also provide seamless communication with existing control applications.
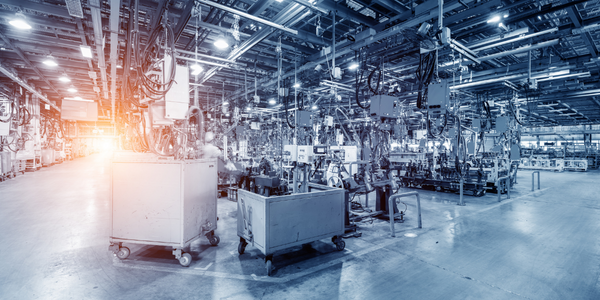
Case Study
Advanced Elastomer Systems Upgrades Production
In order to maintain its share of the international market for thermoplastic elastomers AES recently expanded its Florida plant by adding a new production line. While the existing lines were operating satisfactorily using a PROVOX distributed control system with traditional analog I/O, AES wanted advanced technology on the new line for greater economy, efficiency, and reliability. AES officials were anxious to get this line into production to meet incoming orders, but two hurricanes slowed construction.
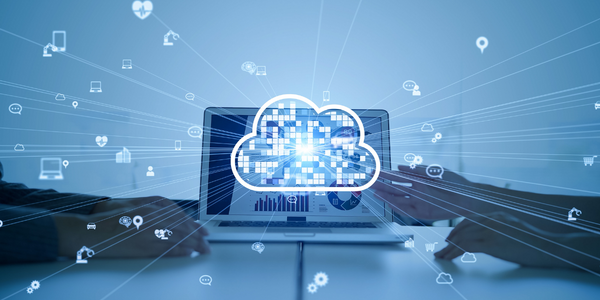
Case Study
Fusion Middleware Integration on Cloud for Pharma Major
Customer wanted a real-time, seamless, cloud based integration between the existing on premise and cloud based application using SOA technology on Oracle Fusion Middleware Platform, a Contingent Worker Solution to collect, track, manage and report information for on-boarding, maintenance and off-boarding of contingent workers using a streamlined and Integrated business process, and streamlining of integration to the back-end systems and multiple SaaS applications.
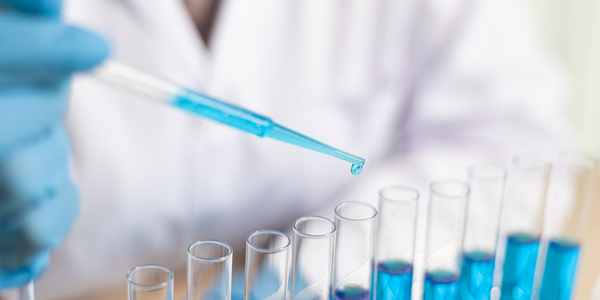
Case Study
Process Control System Support
In many automated production facilities, changes are made to SIMATIC PCS 7 projects on a daily basis, with individual processes often optimised by multiple workers due to shift changes. Documentation is key here, as this keeps workers informed about why a change was made. Furthermore, SIMATIC PCS 7 installations are generally used in locations where documentation is required for audits and certification. The ability to track changes between two software projects is not only an invaluable aid during shift changes, but also when searching for errors or optimising a PCS 7 installation. Every change made to the system is labour-intensive and time-consuming. Moreover, there is also the risk that errors may occur. If a change is saved in the project, then the old version is lost unless a backup copy was created in advance. If no backup was created, it will no longer be possible to return to the previous state if and when programming errors occur. Each backup denotes a version used by the SIMATIC PCS 7 system to operate an installation. To correctly interpret a version, information is required on WHO changed WHAT, WHERE, WHEN and WHY: - Who created the version/who is responsible for the version? - Who released the version? - What was changed in the version i.e. in which block or module of the SIMATIC PCS 7 installation were the changes made? - When was the version created? Is this the latest version or is there a more recent version? - Why were the changes made to the version? If they are part of a regular maintenance cycle, then is the aim to fix an error or to improve production processes? - Is this particular version also the version currently being used in production? The fact that SIMATIC PCS 7 projects use extremely large quantities of data complicates the situation even further, and it can take a long time to load and save information as a result. Without a sustainable strategy for operating a SIMATIC PCS 7 installation, searching for the right software version can become extremely time-consuming and the installation may run inefficiently as a result.