Download PDF
Mondelēz International's Innovation Transformation with Sopheon's IoT Solution
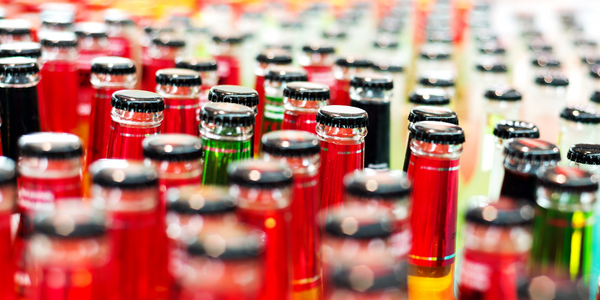
Technology Category
- Analytics & Modeling - Process Analytics
- Functional Applications - Enterprise Resource Planning Systems (ERP)
Applicable Functions
- Product Research & Development
- Quality Assurance
Use Cases
- Process Control & Optimization
- Supply Chain Visibility
The Challenge
Mondelēz International, a global food and beverage leader, faced significant challenges during the COVID-19 pandemic. The company had to accelerate its consumer-centric growth strategy amidst the global disruption. A significant part of this strategy involved replacing outdated, disconnected systems and tools for innovation process management. Mondelēz needed a single solution for managing its innovation portfolio, resources, demand planning, and project execution. The company was also faced with the challenge of delivering products to market that exceed consumer expectations faster and more profitably. The existing disconnected legacy systems were hampering timely insights, decision-making, and resource allocation. There was a lack of transparency to the innovation portfolio which slowed project management and complicated governance. Outdated and fragmented analytics created a lack of innovation project visibility across global teams.
The Customer
Mondelēz International
About The Customer
Mondelēz International is a global leader in the food and beverage industry, boasting a stable of well-known brands like Cadbury, Oreo, and many other household names. The company has a strong focus on innovation and consumer-centric growth. At the onset of the COVID-19 pandemic, Mondelēz doubled down on its long-term strategy to accelerate this growth. The company conducts more than 6,500 product-related project activities in a typical year, using a gated process to identify, define, and plan the resources allocated to these projects.
The Solution
To address these challenges, Mondelēz partnered with Sopheon to deploy its Accolade software as a new, enterprise-wide platform for innovation portfolio and process management. The software was implemented rapidly, with a focus on driving adoption across the global enterprise. The initial Accolade implementation was built in just nine weeks, followed by four weeks of testing and validation. The solution aimed at creating a 'single source of truth' by retiring outmoded processes and disconnected software solutions, then merging those functions into Accolade. With Accolade, Mondelēz International achieved 100 percent global visibility to all new product initiatives in the portfolio. This enabled the company to allocate resources and prioritize the highest-value products. The entire global organization now uses a single source for information, product, project, and portfolio management, enabling greater collaboration and efficiencies across product lines and business units.
Operational Impact
Quantitative Benefit
Related Case Studies.
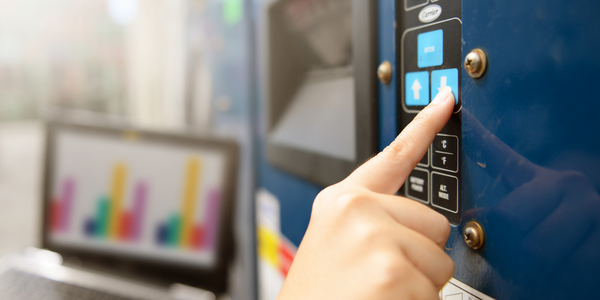
Case Study
Remote Temperature Monitoring of Perishable Goods Saves Money
RMONI was facing temperature monitoring challenges in a cold chain business. A cold chain must be established and maintained to ensure goods have been properly refrigerated during every step of the process, making temperature monitoring a critical business function. Manual registration practice can be very costly, labor intensive and prone to mistakes.
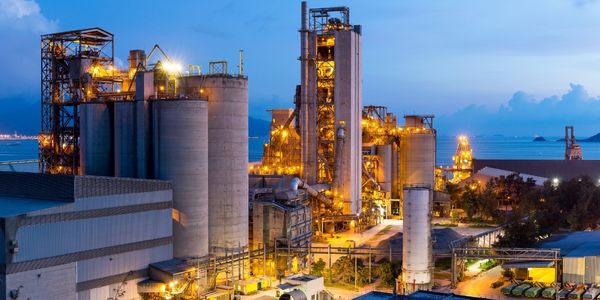
Case Study
System 800xA at Indian Cement Plants
Chettinad Cement recognized that further efficiencies could be achieved in its cement manufacturing process. It looked to investing in comprehensive operational and control technologies to manage and derive productivity and energy efficiency gains from the assets on Line 2, their second plant in India.
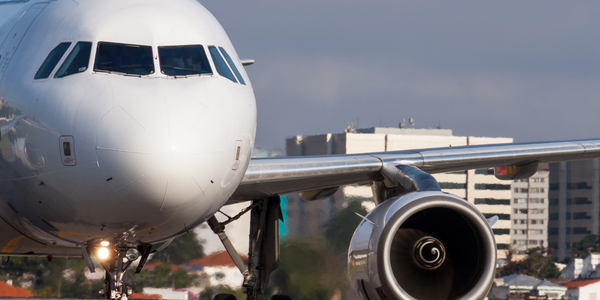
Case Study
Airbus Soars with Wearable Technology
Building an Airbus aircraft involves complex manufacturing processes consisting of thousands of moving parts. Speed and accuracy are critical to business and competitive advantage. Improvements in both would have high impact on Airbus’ bottom line. Airbus wanted to help operators reduce the complexity of assembling cabin seats and decrease the time required to complete this task.
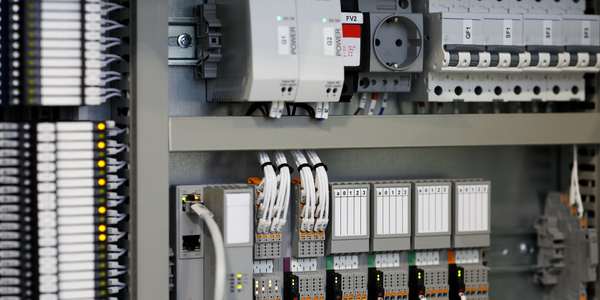
Case Study
Improving Production Line Efficiency with Ethernet Micro RTU Controller
Moxa was asked to provide a connectivity solution for one of the world's leading cosmetics companies. This multinational corporation, with retail presence in 130 countries, 23 global braches, and over 66,000 employees, sought to improve the efficiency of their production process by migrating from manual monitoring to an automatic productivity monitoring system. The production line was being monitored by ABB Real-TPI, a factory information system that offers data collection and analysis to improve plant efficiency. Due to software limitations, the customer needed an OPC server and a corresponding I/O solution to collect data from additional sensor devices for the Real-TPI system. The goal is to enable the factory information system to more thoroughly collect data from every corner of the production line. This will improve its ability to measure Overall Equipment Effectiveness (OEE) and translate into increased production efficiencies. System Requirements • Instant status updates while still consuming minimal bandwidth to relieve strain on limited factory networks • Interoperable with ABB Real-TPI • Small form factor appropriate for deployment where space is scarce • Remote software management and configuration to simplify operations