Download PDF
Oceana Shipyard Gains Global Competitive Advantage by Streamlining Production Process with AVEVA Enterprise Resource Management
Technology Category
- Functional Applications - Enterprise Resource Planning Systems (ERP)
Applicable Industries
- Marine & Shipping
Applicable Functions
- Discrete Manufacturing
- Procurement
Use Cases
- Manufacturing System Automation
- Supply Chain Visibility
Services
- System Integration
The Challenge
Oceana, a new, medium-sized shipyard specializing in the production of AHTS, PSV and offshore supply vessels, faced several challenges in streamlining its ship production process. Accessing all the necessary information was difficult, and planning across all disciplines was unreliable. The production process was inefficient as people and systems worked separately, not together. The company also struggled with high production costs and assembly times. Furthermore, there were issues with material delivery, with incorrect materials being delivered to the wrong places at the wrong times.
About The Customer
Oceana is a new, medium-sized shipyard based in Itajai, Santa Catarina, Brazil. The shipyard specializes in the production of Anchor Handling Tug Supply (AHTS), Platform Supply Vessel (PSV), and offshore supply vessels. It employs the latest equipment and production processes in building high-technology vessels for the petroleum and gas sectors. The shipyard employs state-of-the-art construction processes and facilities. With more than 1,500 employees, it also has the capacity to build up to six ships per year. The shipyard itself was designed in accordance with strict sustainability standards; these include reuse of rainwater, natural ventilation and light and an adjacent green area of 55,000m2.
The Solution
To overcome these challenges, Oceana selected the AVEVA ERM Integrated Suite. This solution enabled Oceana to conduct cross-departmental planning between engineering, procurement, warehouse, and planning to keep projects on schedule. The AVEVA ERM suite chosen by Oceana is made up of integrated applications, each of which can be configured, if necessary, to address specific standard operating procedures. The applications not only drive greater planning efficiencies but, in doing so, make production a far smoother process. This has resulted in Oceana’s initial gains in time against tight schedules.
Operational Impact
Related Case Studies.
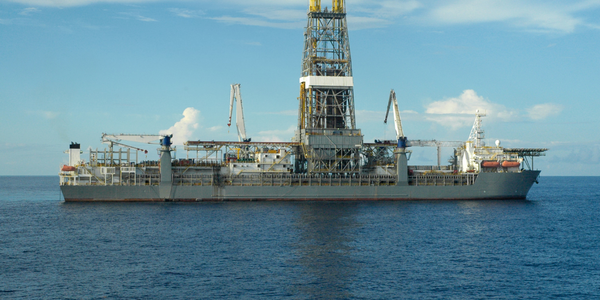
Case Study
Drill ship power challenge: hybrid solution solves distribution issues
Aspin Kemp & Associates (AKA), a manufacturer of electrical power and control systems headquartered in Montague, PEI, encountered one with its hybrid power initiative, the first hybrid drill floor destined for installation on ultra-deepwater drill ships operated by Transocean, Swiss offshore drilling contractors. Since on-site modification was impossible and scrap recycling of any modifications was unacceptable, the enclosures had to arrive ready-to-install.
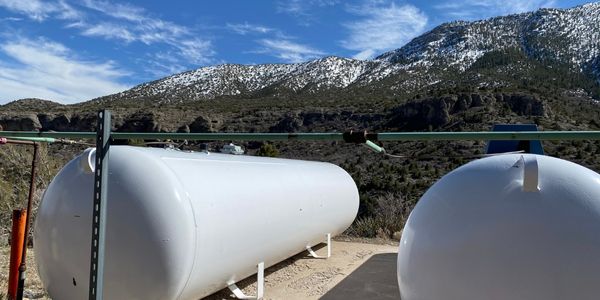
Case Study
Ensures Tanker Safety and Emissions Compliance
Storage tanks are irregular in shape and a certain amount of mathematical modelling is required to get an accurate representation of volume and, more importantly, the weight of material in each tank. In addition, countries have different emission regulations, so the ships position needed to be accurately known in order to geotag emission data.
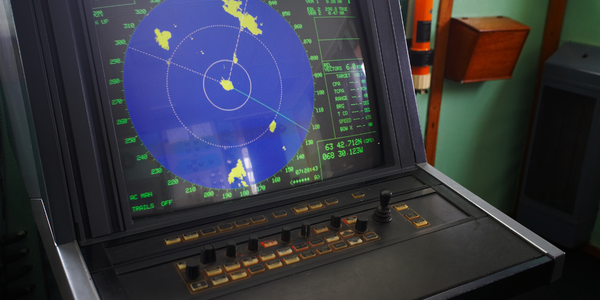
Case Study
Real-time Networked Sonar System for Ships
A multinational, knowledge-based corporation that delivers marine electronics solutions is utilizing industrial Ethernet technology to help ensure that operations at sea are dependable and optimal. Based in Europe, the company has nearly 4000 employees working in 20 countries around the world, and produces high-tech systems for offshore oil and gas operations, merchant marine systems, and various applications for the defense and aerospace industries. The company produces products and systems used by merchant vessels and offshore installations for positioning, navigation, automation, as well as for surveying and monitoring the seabed, and for fishing vessels and fi sheries research. As one of the major suppliers of high quality marine electronics in the world, their products include chart plotters for yachts, triple redundant dynamic positioning systems for oil drilling rigs, and sonar and instrument systems for scientifi c research vessels. Products used for marine applications must be rugged enough to endure the corrosive effects of salt water, and be able to withstand excessive amounts of vibration and shock. For this reason, the company only uses DNV and GL certified products and components to ensure that their systems can meet the high standards required by the maritime industry.
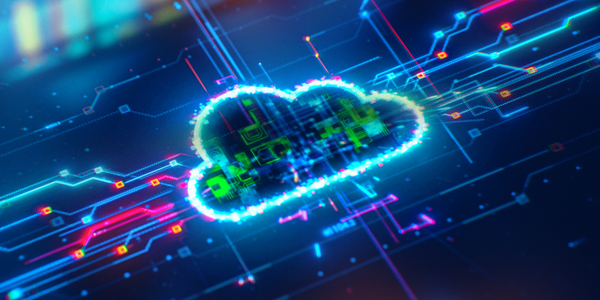
Case Study
Fleet Management Connectivity Solution for Marzam
Marzam, in order to ensure the best service, invested 3 million dollars in the construction of 2 fuel oil tanks with 40k gallons and 10k gallons capacity each, located in Manta, Ecuador. The customer needs to keep fleet operations going with fuel available at all times in order to guarantee quality of service. KEY ELEMENTS FOR THE CUSTOMER: Real-time level monitoring: Tank infrastructure remote level monitoring. Configure alerts and notifications when reaching critical values to avoid the need for emergency refills and optimize supply schedules. Real-time consumption monitoring: The customer needed an easy way to monitor in real-time accurate values of consumption.
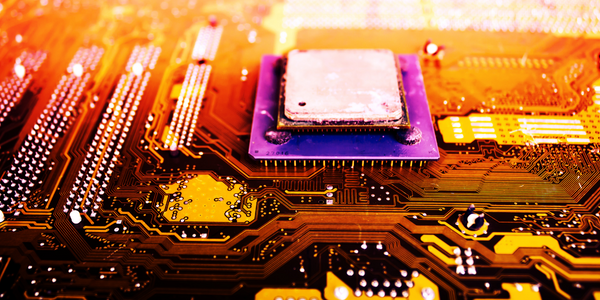
Case Study
Mitsubishi Electric's Edge Computing Solution Powered by Wind River VxWorks
Mitsubishi Electric Corporation, a global leader in factory automation (FA) applications, identified edge computing as a critical component of the Industrial Internet of Things (IIoT). The company aimed to enhance device and data security, reduce data traffic to the cloud, and enable faster response to network or device issues. In 2018, Mitsubishi Electric launched its first line of industrial hardware products designed for edge computing, the MELIPC Series. The primary development goals for MELIPC were to support the type of edge computing promoted by Mitsubishi Electric and to introduce advanced vision technology for device control. The flagship computer of the MELIPC line, the MI5000, was designed to combine real-time equipment control with high-speed data collection, processing, diagnosis, and feedback in a single machine. However, the development team needed a real-time control platform that could seamlessly integrate real-time control with proven analytic and diagnostic applications.
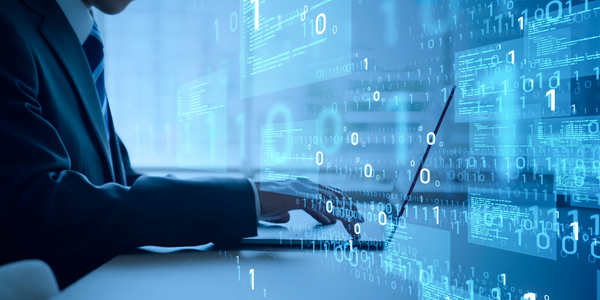
Case Study
Migrating to Software-Only Licenses for More Responsive License Management
The world’s premier shipping companies work with the software solutions of ABB Marine & Ports to get their vessels safely and efficiently to their destinations. A loyal customer of Wibu-Systems for over a decade, ABB has been relying on CodeMeter dongles to store the license keys for their ABB AbilityTM Marine Advisory System - OCTOPUS.The current version of the system is using Wibu-Systems’ robust metal-case CmStick ME, a perfect choice for the rugged conditions at sea. As satellite communications has made fast Internet connections at sea a common reality for maritime operators, the company is looking to move from physical to software solutions to streamline its logistics processes.