Download PDF
Optimising the COLLAPSECON C-400: A Case Study in IoT and Shipping Logistics
Technology Category
- Functional Applications - Manufacturing Execution Systems (MES)
- Platform as a Service (PaaS) - Application Development Platforms
Applicable Industries
- Marine & Shipping
- Transportation
Applicable Functions
- Logistics & Transportation
- Product Research & Development
Use Cases
- Additive Manufacturing
- Intelligent Packaging
Services
- System Integration
- Testing & Certification
The Challenge
The shipping and logistics industries are responsible for facilitating over 90% of global trade, utilizing an estimated 35 million containers worldwide. However, global trade deficits result in 1 in 5 containers being shipped empty, leading to losses of over $30 billion annually. CEC Systems’ COLLAPSECON® provides an innovative solution to this problem, with a collapsible container design that improves operational efficiency and reduces environmental impact. However, the COLLAPSECON® design faced challenges due to over-engineering to meet industry ISO standards and pass manufacture testing. The units were nearly three times heavier than a standard container, due to the addition of moving parts and unique structural components. The complex geometries used in the design were also incompatible with traditional manufacturing methods, potentially leading to increased manufacturing costs. To optimise the COLLAPSECON® C-400 design for mass production and operational use, CEC Systems partnered with The Singapore Institute of Manufacturing Technology (SIMTech).
About The Customer
CEC Systems is an industrial technology company founded in 2015, developing integrated solutions to the complex global challenges facing the shipping and logistics industries. Their innovative product, the COLLAPSECON®, is the world’s first semi-automated Collapsible Economic Container. Achieving a 4:1 ratio, COLLAPSECON® enables 4 empty containers to be collapsed and combined to form a single container. This solution improves operational efficiency, enhances return on investment, and reduces the impact on the environment. However, the design of the COLLAPSECON® faced challenges due to over-engineering and the use of complex geometries, which led to increased weight and potential manufacturing costs.
The Solution
SIMTech utilised the Altair HyperWorksTM software suite, and in particular Altair OptiStructTM, to find potential solutions for weight reduction without increasing manufacturing costs. The process involved constructing Finite Element (FE) models in Altair HyperMeshTM and solving optimisation problems with Altair OptiStructTM. The container design was reduced to seven sub-assemblies, and size optimisation of all container components was done by considering all critical load cases. High strength steel was used for hinges in the COLLAPSECON® C-400 units, which were costly and difficult to manufacture. Following a strength and deflection assessment of the current hinges, new hinge designs were proposed. SIMTech also investigated the damage tolerance of selected critical parts, simulating simple cracks, tears, and slits scenarios, and the effect of localised deformations. The morphing capabilities in Altair HyperMeshTM were used to locally deform the model to simulate accidental impact or other failure events.
Operational Impact
Quantitative Benefit
Related Case Studies.
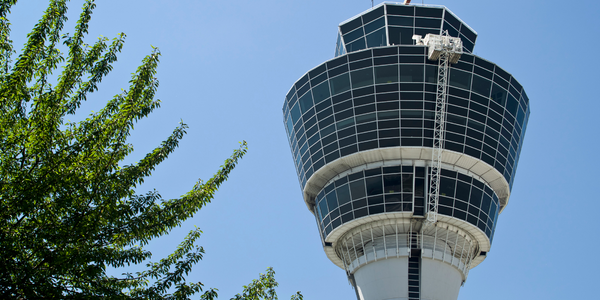
Case Study
Airport SCADA Systems Improve Service Levels
Modern airports are one of the busiest environments on Earth and rely on process automation equipment to ensure service operators achieve their KPIs. Increasingly airport SCADA systems are being used to control all aspects of the operation and associated facilities. This is because unplanned system downtime can cost dearly, both in terms of reduced revenues and the associated loss of customer satisfaction due to inevitable travel inconvenience and disruption.
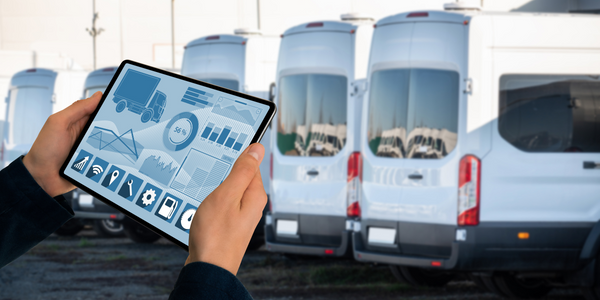
Case Study
IoT-based Fleet Intelligence Innovation
Speed to market is precious for DRVR, a rapidly growing start-up company. With a business model dependent on reliable mobile data, managers were spending their lives trying to negotiate data roaming deals with mobile network operators in different countries. And, even then, service quality was a constant concern.
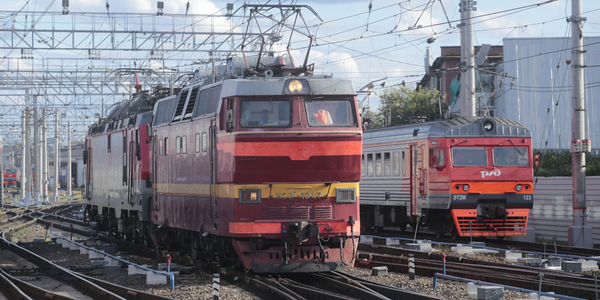
Case Study
Digitize Railway with Deutsche Bahn
To reduce maintenance costs and delay-causing failures for Deutsche Bahn. They need manual measurements by a position measurement system based on custom-made MEMS sensor clusters, which allow autonomous and continuous monitoring with wireless data transmission and long battery. They were looking for data pre-processing solution in the sensor and machine learning algorithms in the cloud so as to detect critical wear.

Case Study
Cold Chain Transportation and Refrigerated Fleet Management System
1) Create a digital connected transportation solution to retrofit cold chain trailers with real-time tracking and controls. 2) Prevent multi-million dollar losses due to theft or spoilage. 3) Deliver a digital chain-of-custody solution for door to door load monitoring and security. 4) Provide a trusted multi-fleet solution in a single application with granular data and access controls.
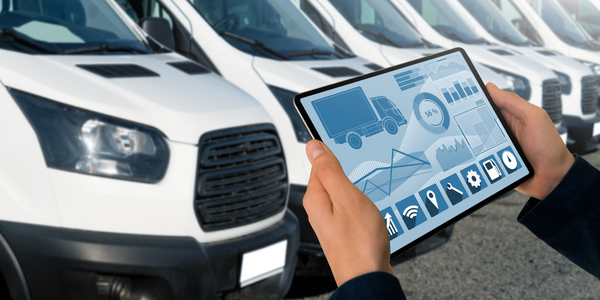
Case Study
Vehicle Fleet Analytics
Organizations frequently implement a maintenance strategy for their fleets of vehicles using a combination of time and usage based maintenance schedules. While effective as a whole, time and usage based schedules do not take into account driving patterns, environmental factors, and sensors currently deployed within the vehicle measuring crank voltage, ignition voltage, and acceleration, all of which have a significant influence on the overall health of the vehicle.In a typical fleet, a large percentage of road calls are related to electrical failure, with battery failure being a common cause. Battery failures result in unmet service agreement levels and costly re-adjustment of scheduled to provide replacement vehicles. To reduce the impact of unplanned maintenance, the transportation logistics company was interested in a trial of C3 Vehicle Fleet Analytics.

Case Study
3M Gains Real-Time Insight with Cloud Solution
The company has a long track record of innovative technology solutions. For example, 3M helps its customers optimize parking operations by automating fee collection and other processes. To improve support for this rapidly expanding segment, 3M needed to automate its own data collection and reporting. The company had recently purchased the assets of parking, tolling, and automatic license plate reader businesses, and required better insight into these acquisitions. Chad Reed, Global Business Manager for 3M Parking Systems, says, “With thousands of installations across the world, we couldn’t keep track of our software and hardware deployments, which made it difficult to understand our market penetration.” 3M wanted a tracking application that sales staff could use to get real-time information about the type and location of 3M products in parking lots and garages. So that it could be used on-site with potential customers, the solution would have to provide access to data anytime, anywhere, and from an array of mobile devices. Jason Fox, Mobile Application Architect at 3M, upped the ante by volunteering to deliver the new app in one weekend. For Fox and his team, these requirements meant turning to the cloud instead of an on-premises datacenter. “My first thought was to go directly to the cloud because we needed to provide access not only to our salespeople, but to resellers who didn’t have access to our internal network,” says Fox. “The cloud just seemed like a logical choice.”