Download PDF
Optimizing Formula Racing Car Parts with IoT: A Case Study on Gator Motorsports
Technology Category
- Robots - Autonomous Guided Vehicles (AGV)
- Sensors - Autonomous Driving Sensors
Applicable Industries
- Automotive
- Cement
Applicable Functions
- Product Research & Development
Use Cases
- Smart Parking
- Vehicle Performance Monitoring
Services
- System Integration
The Challenge
Gator Motorsports, the Formula SAE team based out of the University of Florida, was faced with the challenge of improving the performance of their Formula-style racecar. The team aimed to decrease the weight and increase the strength of the car parts for better competition performance and faster design. The critical components that needed redesigning included the pedal box and suspension bell cranks. The team's goal was to develop and construct a single-seat race car for the non-professional weekend autocross racer with the best overall package of design, construction, performance, and cost. The challenge was not only to engineer and produce a reliable, high-performance vehicle but also to organize and manage a team to develop a feasible product for the market.
About The Customer
Gator Motorsports is the Formula SAE team based out of the University of Florida. Each May, Gator Motorsports competes against 120 teams from all over the world in the Formula Society of Automotive Engineers (FSAE) design competition in Michigan. This competition assesses the team’s ability to not only engineer and produce a reliable, high-performance vehicle, but also its ability to organize and manage a team to develop a feasible product for market. The program provides students with the technical, teamwork, and project management skills required to transition seamlessly into careers in industry. Gator Motorsports has been extremely successful in recent years with a 9th place overall finish in 2016 and a 2nd place finish in 2015.
The Solution
The team utilized solidThinking Inspire for concept generation and optimization to redesign and increase the performance of the vehicle's bell cranks and brake pedal. The first parts that Gator Motorsports focused on were the bell cranks. They measured how far the suspension system could safely travel and used their data logging system to find the maximum forces on the pull rod. These forces were then applied to different locations on the bell crank in Inspire, which used these loads to generate the optimal structural design for the bell cranks. The next part that the team worked on with Inspire was the car's brake pedal. After viewing a few online tutorials, the team was comfortable enough with the program to apply loads and perform a full optimization of the pedal. The whole redesign process took less than two weeks from start to finish.
Operational Impact
Quantitative Benefit
Related Case Studies.
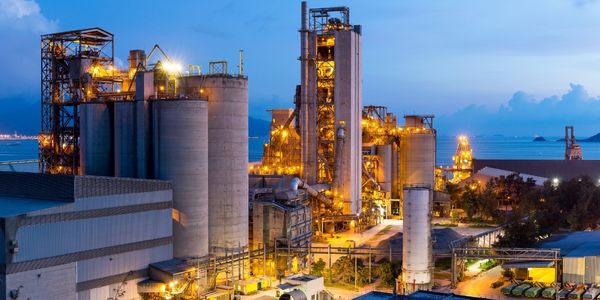
Case Study
System 800xA at Indian Cement Plants
Chettinad Cement recognized that further efficiencies could be achieved in its cement manufacturing process. It looked to investing in comprehensive operational and control technologies to manage and derive productivity and energy efficiency gains from the assets on Line 2, their second plant in India.
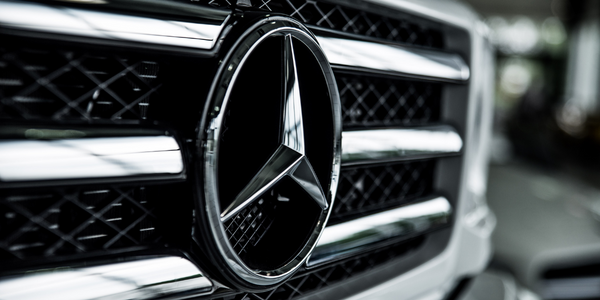
Case Study
Integral Plant Maintenance
Mercedes-Benz and his partner GAZ chose Siemens to be its maintenance partner at a new engine plant in Yaroslavl, Russia. The new plant offers a capacity to manufacture diesel engines for the Russian market, for locally produced Sprinter Classic. In addition to engines for the local market, the Yaroslavl plant will also produce spare parts. Mercedes-Benz Russia and his partner needed a service partner in order to ensure the operation of these lines in a maintenance partnership arrangement. The challenges included coordinating the entire maintenance management operation, in particular inspections, corrective and predictive maintenance activities, and the optimizing spare parts management. Siemens developed a customized maintenance solution that includes all electronic and mechanical maintenance activities (Integral Plant Maintenance).
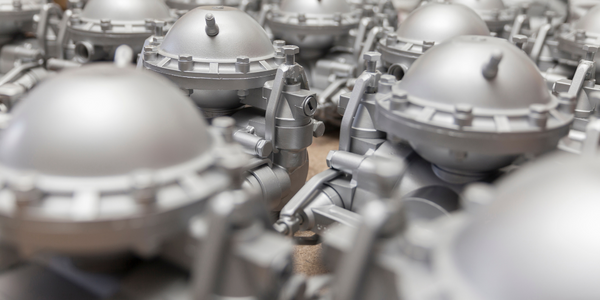
Case Study
Monitoring of Pressure Pumps in Automotive Industry
A large German/American producer of auto parts uses high-pressure pumps to deburr machined parts as a part of its production and quality check process. They decided to monitor these pumps to make sure they work properly and that they can see any indications leading to a potential failure before it affects their process.