Download PDF
Optimizing Formula Student Car Performance with IoT
Technology Category
- Robots - Autonomous Guided Vehicles (AGV)
- Sensors - Autonomous Driving Sensors
Applicable Industries
- Automotive
- Packaging
Applicable Functions
- Product Research & Development
- Quality Assurance
Use Cases
- Smart Parking
- Vehicle-to-Infrastructure
Services
- System Integration
- Testing & Certification
The Challenge
The Durham University Electric Motorsport (DUEM) team, a group of undergraduate and postgraduate students, were faced with the challenge of reducing the weight and improving the performance of their Formula Student vehicle. The team participates in the highly competitive Formula Student competition, hosted annually by the Institute of Mechanical Engineering (IMechE) at the Silverstone Formula 1 track in the UK. The competition requires teams to demonstrate their technical, engineering, design, and manufacturing skills, reflecting the changes and demands of the industry while considering new developments in commercial car racing. The DUEM team aimed to apply the latest weight-saving technology to achieve a faster, more efficient car by optimizing an upright design for multiple load cases. The optimization of the upright design was a complex challenge, requiring design for multiple load cases including bump, cornering, braking, and acceleration loads. The conventional means of design iteration for many load cases by removing areas of low stress at each iteration was time-consuming and the final solution was not necessarily the most structurally efficient.
About The Customer
The Durham University Electric Motorsport (DUEM) team is a UK-based team of students who design, build, and race electric vehicles. The team consists of more than 30 undergraduate and postgraduate students with specialties in Vehicle Dynamics, Electronics, and Aerodynamics. The team members volunteer to work outside of university hours to participate in motorsport competitions. The team has a track record of participating in international competitions, including the North American Solar Challenge and the World Solar Challenge in Australia. They are known for their innovative approach, being the first Formula Student team in Class 2 to design a Regenerative Magneto Rheological (MR) suspension system.
The Solution
The DUEM team turned to Altair HyperWorks simulation suite, specifically OptiStruct, to meet this challenge. OptiStruct is a design tool that predicts optimal shapes of structures early in the design process using topology optimization methods, facilitating an analysis-driven design process that results in more efficient designs in shorter design cycle times. As the design process advances, OptiStruct's powerful shape and size optimization capabilities can be applied to further improve design performance. Using highly advanced optimization algorithms, OptiStruct can solve the most complex optimization problems with thousands of design variables in a short period of time. The design region was imported into OptiStruct and meshed. Load cases were applied for a 2g bump, 1.6g cornering, 1.6g braking, and combined braking, bumps and cornering load cases. Manufacturing constraints such as draw direction were applied to ensure that the final result is feasible for manufacturing. OptiStruct reduced the overall design cycle time of CAE-CAD iterations and enabled improvements.
Operational Impact
Quantitative Benefit
Related Case Studies.
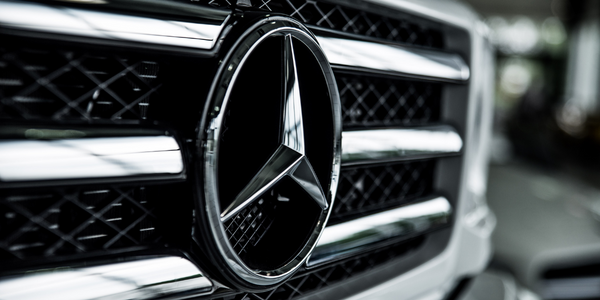
Case Study
Integral Plant Maintenance
Mercedes-Benz and his partner GAZ chose Siemens to be its maintenance partner at a new engine plant in Yaroslavl, Russia. The new plant offers a capacity to manufacture diesel engines for the Russian market, for locally produced Sprinter Classic. In addition to engines for the local market, the Yaroslavl plant will also produce spare parts. Mercedes-Benz Russia and his partner needed a service partner in order to ensure the operation of these lines in a maintenance partnership arrangement. The challenges included coordinating the entire maintenance management operation, in particular inspections, corrective and predictive maintenance activities, and the optimizing spare parts management. Siemens developed a customized maintenance solution that includes all electronic and mechanical maintenance activities (Integral Plant Maintenance).
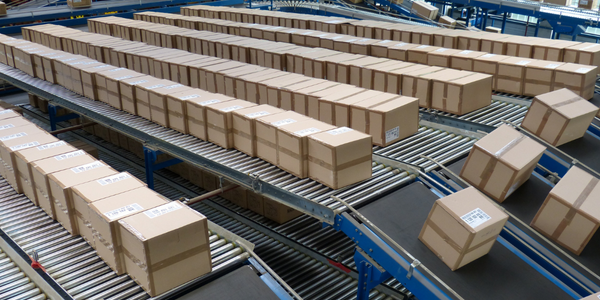
Case Study
IoT Data Analytics Case Study - Packaging Films Manufacturer
The company manufactures packaging films on made to order or configure to order basis. Every order has a different set of requirements from the product characteristics perspective and hence requires machine’s settings to be adjusted accordingly. If the film quality does not meet the required standards, the degraded quality impacts customer delivery causes customer dissatisfaction and results in lower margins. The biggest challenge was to identify the real root cause and devise a remedy for that.
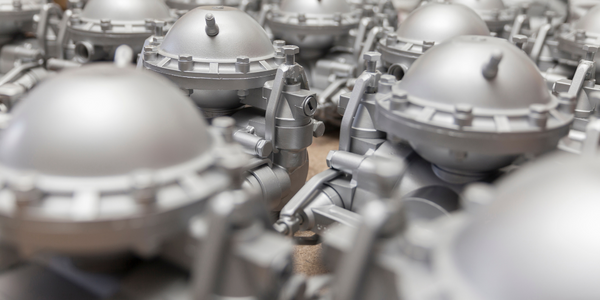
Case Study
Monitoring of Pressure Pumps in Automotive Industry
A large German/American producer of auto parts uses high-pressure pumps to deburr machined parts as a part of its production and quality check process. They decided to monitor these pumps to make sure they work properly and that they can see any indications leading to a potential failure before it affects their process.