Download PDF
Optimizing Hydropower Plant Location with IoT: A Case Study of Kawa Engineering Ltd.
Technology Category
- Actuators - Hydraulic Actuators
- Analytics & Modeling - Digital Twin / Simulation
Applicable Industries
- Cement
- Renewable Energy
Applicable Functions
- Product Research & Development
Use Cases
- Construction Management
- Virtual Prototyping & Product Testing
The Challenge
Kawa Engineering Ltd. was faced with the challenge of locating a powerhouse close to a waterfall for a client in an area with minimal flood risk. The stakes were high as any occurrence of flooding in the powerhouse would result in significant costs. The ideal location would not only mitigate the risk of flooding but also reduce the need for additional components to protect electrical equipment such as generators, turbines, and switch boxes. Furthermore, the right location would determine the cut and fill required for construction, thereby conserving construction resources.
About The Customer
Kawa Engineering Ltd., based in Vancouver, Canada, is a provider of engineering consulting services. While their expertise is not limited to any specific field, they primarily focus on the design of hydropower projects. They leverage state-of-the-art computational software, finite element analysis, and computer-aided design to add value to their customers. Their services span from conceptual design to final design and construction management of hydroelectric schemes. Their commitment to harnessing renewable energy sources responsibly and effectively is evident in their work.
The Solution
Kawa Engineering Ltd. employed a series of technological solutions to address this challenge. Firstly, they created a model of the riverbed’s surface and shores, near where the powerhouse would be positioned, using data collected via laser scanning. This data was then imported into CAD software and then ANSYS® DesignModeler®. They then used the Eulerian−Eulerian multiphase model in ANSYS CFD to define the interaction between flood water and the ambient air for open channel flow. Transient simulation was employed to determine the initial hydraulic jump from flood-water flow through the waterfall. The CFD simulation was run on a 32-core cluster machine and repeated multiple times using different river conditions to determine the maximum hydraulic jump.
Operational Impact
Quantitative Benefit
Related Case Studies.
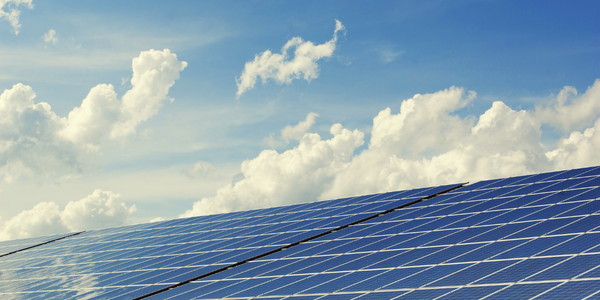
Case Study
Remote Monitoring & Predictive Maintenance App for a Solar Energy System
The maintenance & tracking of various modules was an overhead for the customer due to the huge labor costs involved. Being an advanced solar solutions provider, they wanted to ensure early detection of issues and provide the best-in-class customer experience. Hence they wanted to automate the whole process.
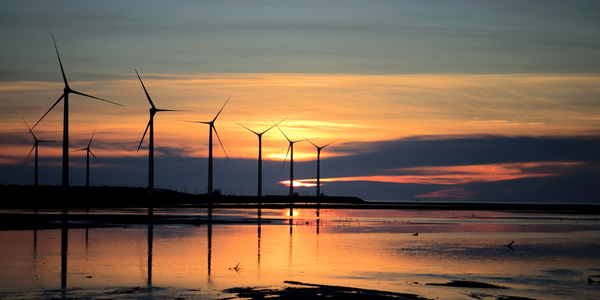
Case Study
Vestas: Turning Climate into Capital with Big Data
Making wind a reliable source of energy depends greatly on the placement of the wind turbines used to produce electricity. Turbulence is a significant factor as it strains turbine components, making them more likely to fail. Vestas wanted to pinpoint the optimal location for wind turbines to maximize power generation and reduce energy costs.
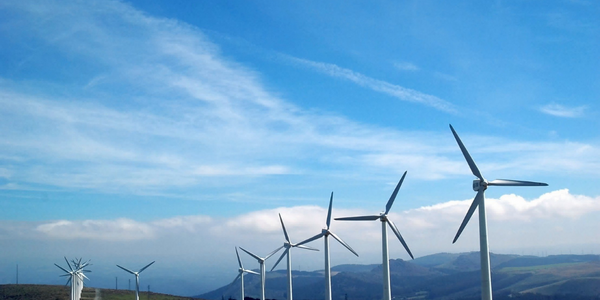
Case Study
Siemens Wind Power
Wind provides clean, renewable energy. The core concept is simple: wind turbines spin blades to generate power. However, today's systems are anything but simple. Modern wind turbines have blades that sweep a 120 meter circle, cost more than 1 million dollars and generate multiple megawatts of power. Each turbine may include up to 1,000 sensors and actuators – integrating strain gages, bearing monitors and power conditioning technology. The turbine can control blade speed and power generation by altering the blade pitch and power extraction. Controlling the turbine is a sophisticated job requiring many cooperating processors closing high-speed loops and implementing intelligent monitoring and optimization algorithms. But the real challenge is integrating these turbines so that they work together. A wind farm may include hundreds of turbines. They are often installed in difficult-to-access locations at sea. The farm must implement a fundamentally and truly distributed control system. Like all power systems, the goal of the farm is to match generation to load. A farm with hundreds of turbines must optimize that load by balancing the loading and generation across a wide geography. Wind, of course, is dynamic. Almost every picture of a wind farm shows a calm sea and a setting sun. But things get challenging when a storm goes through the wind farm. In a storm, the control system must decide how to take energy out of gusts to generate constant power. It must intelligently balance load across many turbines. And a critical consideration is the loading and potential damage to a half-billion-dollar installed asset. This is no environment for a slow or undependable control system. Reliability and performance are crucial.
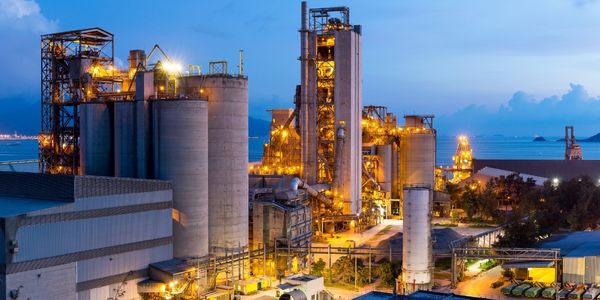
Case Study
System 800xA at Indian Cement Plants
Chettinad Cement recognized that further efficiencies could be achieved in its cement manufacturing process. It looked to investing in comprehensive operational and control technologies to manage and derive productivity and energy efficiency gains from the assets on Line 2, their second plant in India.
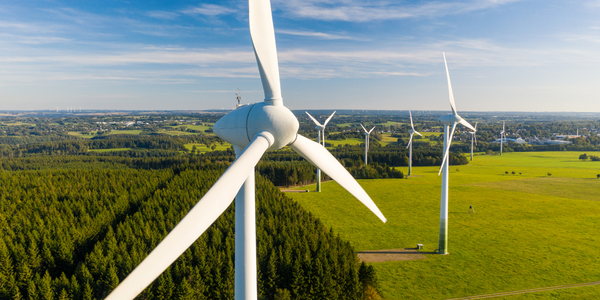
Case Study
Remote Monitoring and Control for a Windmill Generator
As concerns over global warming continue to grow, green technologies are becoming increasingly popular. Wind turbine companies provide an excellent alternative to burning fossil fuels by harnessing kinetic energy from the wind and converting it into electricity. A typical wind farm may include over 80 wind turbines so efficient and reliable networks to manage and control these installations are imperative. Each wind turbine includes a generator and a variety of serial components such as a water cooler, high voltage transformer, ultrasonic wind sensors, yaw gear, blade bearing, pitch cylinder, and hub controller. All of these components are controlled by a PLC and communicate with the ground host. Due to the total integration of these devices into an Ethernet network, one of our customers in the wind turbine industry needed a serial-to-Ethernet solution that can operate reliably for years without interruption.
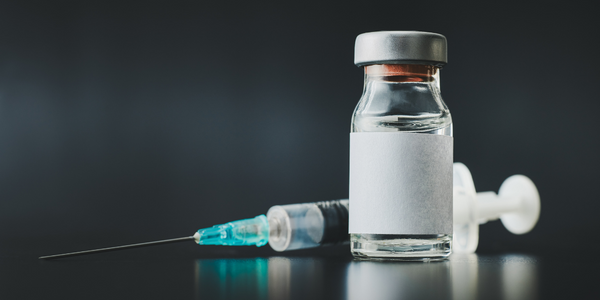
Case Study
Temperature monitoring for vaccine fridges
Dulas wanted a way to improve the reliability of the cold chain, facilitating maintenance and ensuring fewer vaccines are spoiled. Dulas wanted an M2M solution which would enable them to record and report the temperature inside vaccine refrigerators.