Download PDF
Optimizing Indoor Climate Control with Simulation and Optimization
Technology Category
- Analytics & Modeling - Digital Twin / Simulation
- Sensors - Environmental Sensors
Applicable Industries
- Buildings
- Equipment & Machinery
Applicable Functions
- Product Research & Development
- Quality Assurance
Use Cases
- Digital Twin
- Virtual Reality
Services
- System Integration
- Testing & Certification
The Challenge
Kampmann GmbH, a leading specialist in heating, cooling, air-conditioning, and integrated building automation, faced the challenge of reducing physical prototypes and gaining early insights into system performance via a virtual development approach. The company's flagship products, KaTherm HK, a trench unit, and KaDeck, a ceiling system for heating and cooling, had to be customized to the needs of each customer and individual environment. This often required individual design adjustments that had to be tested and approved on site. Before the introduction of simulation, the air-conditioning systems were physically tested, which resulted in longer development time and required greater effort. The challenge was to find a solution that would allow for early testing of functionality and special requirements prior to production, thereby reducing the need for physical prototypes and shortening the development cycle.
About The Customer
Kampmann GmbH is an internationally leading specialist for heating, cooling, air-conditioning, and integrated building automation. The company employs more than 720 people at 14 locations all over the world. Traditionally, Kampmann’s expertise is in series production, offering a broad range of system variants and appealing solutions that are project-based and individually customized. The flagship products of the company are KaTherm HK, a trench unit, and KaDeck, a ceiling system for heating and cooling. The company prides itself on its ability to customize its products to the needs of each customer and individual environment.
The Solution
Kampmann adopted a virtual development process using the Altair HyperWorks® software suite, specifically AcuSolve®, the CFD solver; OptiStruct®, the suite's FE-solver and an optimization tool; and HyperMesh® for modeling and meshing tasks. For plant control design, Kampmann considered solidThinking Activate®, a mapping software for control systems. This simulation approach allowed Kampmann engineers to gain insights into the internal processes of the system, which were difficult to study through physical testing. The simulation made it possible to test multiple variants and optimize the system, so the perfect solution for each customer could be designed. After final physical testing, the design could be approved by the customer on site. The use of simulation also helped Kampmann engineers shorten testing time by an entire week during a recent project to optimize the trench heating/cooling system Katherm HK.
Operational Impact
Quantitative Benefit
Related Case Studies.
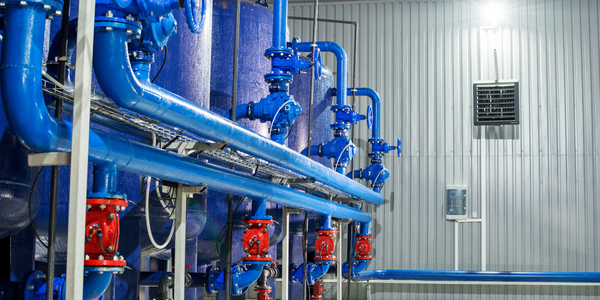
Case Study
Smart Water Filtration Systems
Before working with Ayla Networks, Ozner was already using cloud connectivity to identify and solve water-filtration system malfunctions as well as to monitor filter cartridges for replacements.But, in June 2015, Ozner executives talked with Ayla about how the company might further improve its water systems with IoT technology. They liked what they heard from Ayla, but the executives needed to be sure that Ayla’s Agile IoT Platform provided the security and reliability Ozner required.
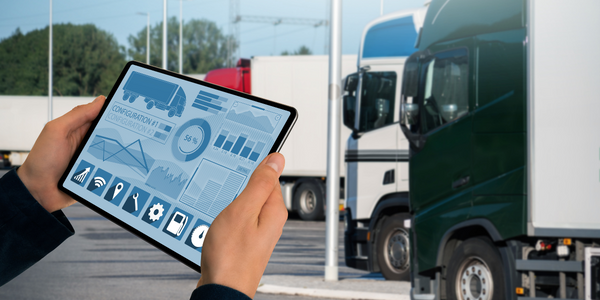
Case Study
IoT enabled Fleet Management with MindSphere
In view of growing competition, Gämmerler had a strong need to remain competitive via process optimization, reliability and gentle handling of printed products, even at highest press speeds. In addition, a digitalization initiative also included developing a key differentiation via data-driven services offers.
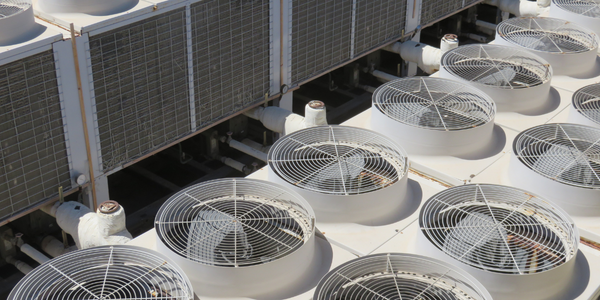
Case Study
Predictive Maintenance for Industrial Chillers
For global leaders in the industrial chiller manufacturing, reliability of the entire production process is of the utmost importance. Chillers are refrigeration systems that produce ice water to provide cooling for a process or industrial application. One of those leaders sought a way to respond to asset performance issues, even before they occur. The intelligence to guarantee maximum reliability of cooling devices is embedded (pre-alarming). A pre-alarming phase means that the cooling device still works, but symptoms may appear, telling manufacturers that a failure is likely to occur in the near future. Chillers who are not internet connected at that moment, provide little insight in this pre-alarming phase.
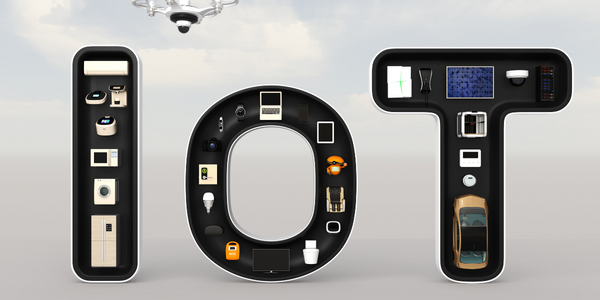
Case Study
Premium Appliance Producer Innovates with Internet of Everything
Sub-Zero faced the largest product launch in the company’s history:It wanted to launch 60 new products as scheduled while simultaneously opening a new “greenfield” production facility, yet still adhering to stringent quality requirements and manage issues from new supply-chain partners. A the same time, it wanted to increase staff productivity time and collaboration while reducing travel and costs.
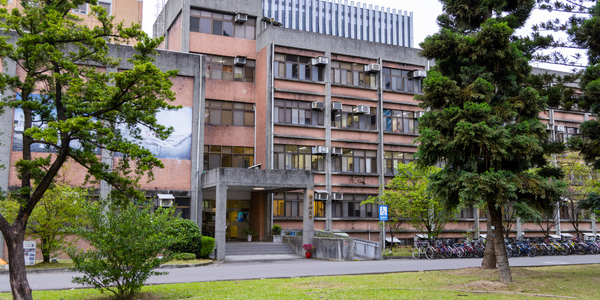
Case Study
Energy Saving & Power Monitoring System
Recently a university in Taiwan was experiencing dramatic power usage increases due to its growing number of campus buildings and students. Aiming to analyze their power consumption and increase their power efficiency across 52 buildings, the university wanted to build a power management system utilizing web-based hardware and software. With these goals in mind, they contacted Advantech to help them develop their system and provide them with the means to save energy in the years to come.
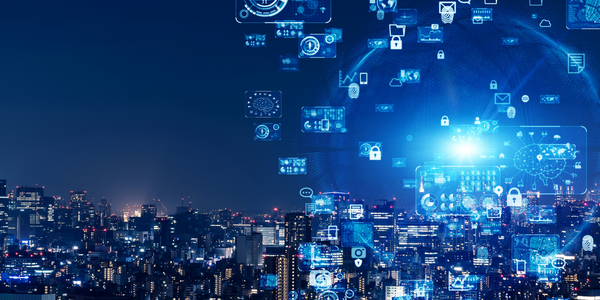
Case Study
Integration of PLC with IoT for Bosch Rexroth
The application arises from the need to monitor and anticipate the problems of one or more machines managed by a PLC. These problems, often resulting from the accumulation over time of small discrepancies, require, when they occur, ex post technical operations maintenance.