Download PDF
OptiStruct Technology Streamlines Production and Maintenance for CLAAS Harvester Reel Assembly
Technology Category
- Functional Applications - Computerized Maintenance Management Systems (CMMS)
Applicable Industries
- Equipment & Machinery
Applicable Functions
- Maintenance
- Product Research & Development
Use Cases
- Traffic Monitoring
Services
- System Integration
The Challenge
CLAAS, a leading manufacturer of agricultural machinery, was facing the challenge of reducing production and serviceability costs of their harvester reel hub assembly system. The existing system, although successful and field-proven, was identified as a candidate for redesign to improve profitability and customer satisfaction. The primary objective of the redesign was to increase serviceability by making an individual reel hub easier to replace without compromising the rigidity of the existing assembly design. The incumbent design had numerous welded lap joints that provided enhanced stiffness, which was a critical factor to maintain in the new design. The challenge was to find a unique reinforcement bead pattern that would meet the redesign objectives while using the same material stock and package envelope.
About The Customer
CLAAS is a Germany-based company that ranks among the world’s leading manufacturers of agricultural machinery. The company is the European market leader for combine harvesters and the number one producer of forage harvesters globally. CLAAS operates in more than 140 countries, offering a diverse product line to meet the varied needs of the agricultural industry. The company is committed to continually improving its products to enhance performance, reliability, and customer satisfaction while reducing production and serviceability costs.
The Solution
To meet the redesign objectives, CLAAS turned to Altair OptiStruct design optimization software. OptiStruct’s topography optimization capabilities were leveraged to define the optimal reinforcement bead pattern that would meet the stiffness objective. The software provided the optimal bead pattern layout for the new reel hub design, which was then used by CLAAS die engineers to create a release level design. The new design significantly reduced the assembly from eight parts to just two, thereby cutting costly welding processes from production and increasing assembly efficiency. The new design also simplified in-service maintenance, as each reel hub could now be removed independently without the need to dismantle the entire system.
Operational Impact
Quantitative Benefit
Related Case Studies.
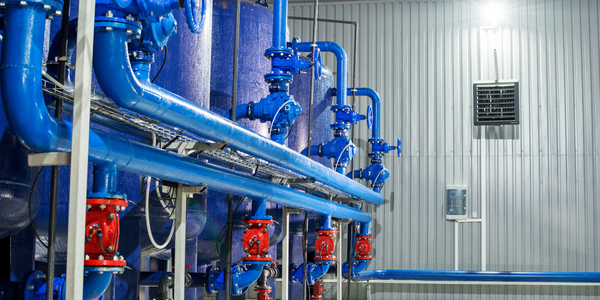
Case Study
Smart Water Filtration Systems
Before working with Ayla Networks, Ozner was already using cloud connectivity to identify and solve water-filtration system malfunctions as well as to monitor filter cartridges for replacements.But, in June 2015, Ozner executives talked with Ayla about how the company might further improve its water systems with IoT technology. They liked what they heard from Ayla, but the executives needed to be sure that Ayla’s Agile IoT Platform provided the security and reliability Ozner required.
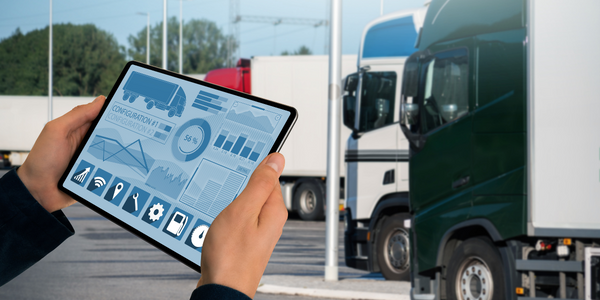
Case Study
IoT enabled Fleet Management with MindSphere
In view of growing competition, Gämmerler had a strong need to remain competitive via process optimization, reliability and gentle handling of printed products, even at highest press speeds. In addition, a digitalization initiative also included developing a key differentiation via data-driven services offers.
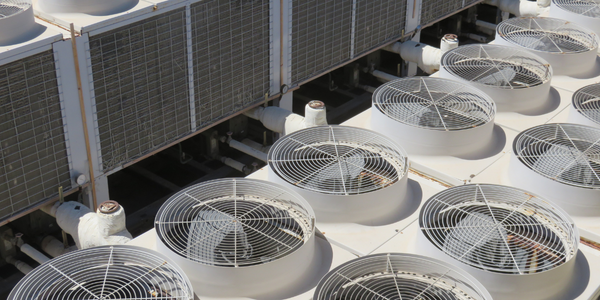
Case Study
Predictive Maintenance for Industrial Chillers
For global leaders in the industrial chiller manufacturing, reliability of the entire production process is of the utmost importance. Chillers are refrigeration systems that produce ice water to provide cooling for a process or industrial application. One of those leaders sought a way to respond to asset performance issues, even before they occur. The intelligence to guarantee maximum reliability of cooling devices is embedded (pre-alarming). A pre-alarming phase means that the cooling device still works, but symptoms may appear, telling manufacturers that a failure is likely to occur in the near future. Chillers who are not internet connected at that moment, provide little insight in this pre-alarming phase.
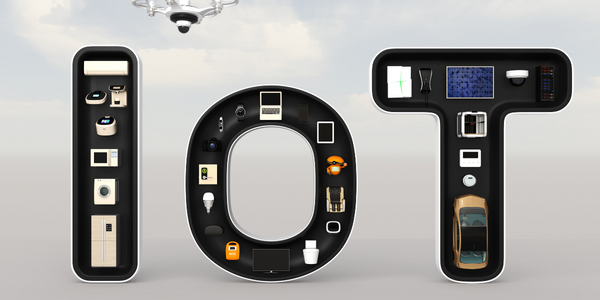
Case Study
Premium Appliance Producer Innovates with Internet of Everything
Sub-Zero faced the largest product launch in the company’s history:It wanted to launch 60 new products as scheduled while simultaneously opening a new “greenfield” production facility, yet still adhering to stringent quality requirements and manage issues from new supply-chain partners. A the same time, it wanted to increase staff productivity time and collaboration while reducing travel and costs.
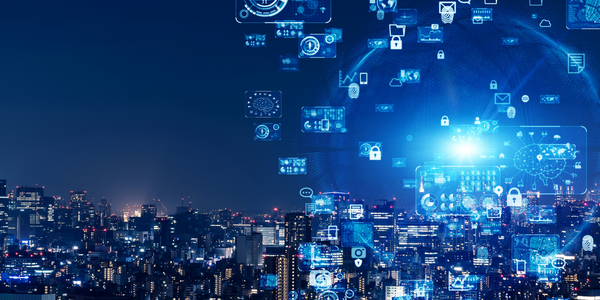
Case Study
Integration of PLC with IoT for Bosch Rexroth
The application arises from the need to monitor and anticipate the problems of one or more machines managed by a PLC. These problems, often resulting from the accumulation over time of small discrepancies, require, when they occur, ex post technical operations maintenance.
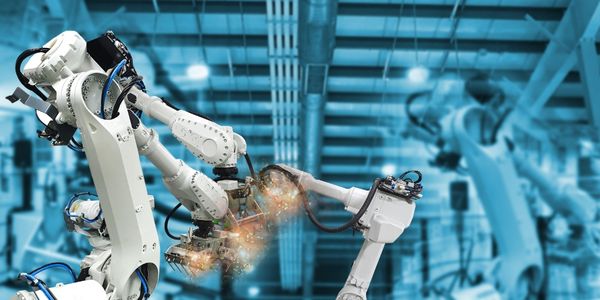
Case Study
Robot Saves Money and Time for US Custom Molding Company
Injection Technology (Itech) is a custom molder for a variety of clients that require precision plastic parts for such products as electric meter covers, dental appliance cases and spools. With 95 employees operating 23 molding machines in a 30,000 square foot plant, Itech wanted to reduce man hours and increase efficiency.