Download PDF
Owens Corning Standardizes on Aspen Plant Scheduler and Receives Rapid Deployment Results
Technology Category
- Functional Applications - Manufacturing Execution Systems (MES)
Applicable Industries
- Buildings
- Construction & Infrastructure
Applicable Functions
- Discrete Manufacturing
- Quality Assurance
Use Cases
- Manufacturing System Automation
- Predictive Waste Reduction
Services
- System Integration
- Software Design & Engineering Services
The Challenge
Owens Corning, a global leader in insulation, roofing, and fiberglass composites, aimed to implement a scheduling solution for its roofing and insulation manufacturing businesses. The goal was to eliminate legacy tools and quickly provide a solution that met the distinct challenges of each business. For the roofing business, the challenges included modifying scheduling settings for products and periods of supply, and using a product wheel for the sequencing of products that consider changeover considerations in the setup mix. For the insulation business, the challenges were to minimize raw materials waste when manufacturing different SKUs of insulation, determine the best co-products to make that will meet demand and minimize excess trim, and schedule long runs that promote steady-state operations and reduce the need for changeovers.
About The Customer
Owens Corning is a global company that develops, manufactures, and markets insulation, roofing, and fiberglass composites. The company's market-leading businesses use their expertise in materials, manufacturing, and building science to develop products and systems that save energy and improve comfort in commercial and residential buildings. Founded in 1938, Owens Corning has been a Fortune 500® company for 61 consecutive years. The company's goal was to implement a scheduling solution for its roofing and insulation manufacturing businesses that eliminated legacy tools and quickly provided a solution that met the distinct challenges of each business.
The Solution
Owens Corning standardized on Aspen Plant Scheduler for both the roofing and insulation divisions using a phased deployment approach. During implementation, schedulers and business users provided input to define requirements for roofing and insulation businesses. As a result, Aspen Plant Scheduler was configured to incorporate constraints that are common across all businesses, such as sequence-dependent setups, as well as site-specific requirements, for example co-products that are unique to a particular business. This allowed a standard solution to be deployed across multiple business units, with a library of features that could be activated/deactivated to meet the needs of the business. After the initial rollout of Aspen Plant Scheduler, more high-value enhancements were needed for the roofing models. Two additional capabilities were added, including ABC scheduling and sequencing via a manufacturing wheel.
Operational Impact
Quantitative Benefit
Related Case Studies.
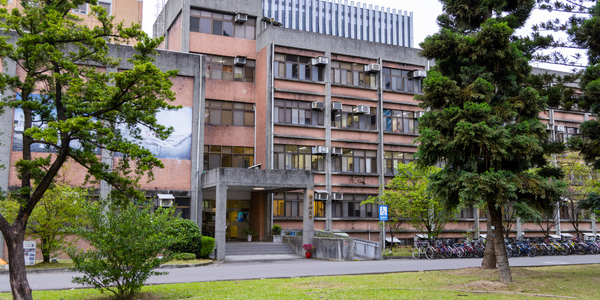
Case Study
Energy Saving & Power Monitoring System
Recently a university in Taiwan was experiencing dramatic power usage increases due to its growing number of campus buildings and students. Aiming to analyze their power consumption and increase their power efficiency across 52 buildings, the university wanted to build a power management system utilizing web-based hardware and software. With these goals in mind, they contacted Advantech to help them develop their system and provide them with the means to save energy in the years to come.
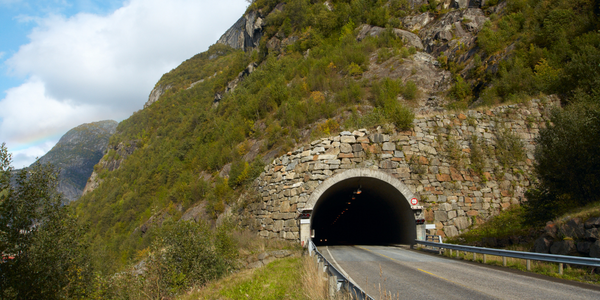
Case Study
IoT System for Tunnel Construction
The Zenitaka Corporation ('Zenitaka') has two major business areas: its architectural business focuses on structures such as government buildings, office buildings, and commercial facilities, while its civil engineering business is targeted at structures such as tunnels, bridges and dams. Within these areas, there presented two issues that have always persisted in regard to the construction of mountain tunnels. These issues are 'improving safety" and "reducing energy consumption". Mountain tunnels construction requires a massive amount of electricity. This is because there are many kinds of electrical equipment being used day and night, including construction machinery, construction lighting, and ventilating fan. Despite this, the amount of power consumption is generally not tightly managed. In many cases, the exact amount of power consumption is only ascertained when the bill from the power company becomes available. Sometimes, corporations install demand-monitoring equipment to help curb the maximum power demanded. However, even in these cases, the devices only allow the total volume of power consumption to be ascertained, or they may issue warnings to prevent the contracted volume of power from being exceeded. In order to tackle the issue of reducing power consumption, it was first necessary to obtain an accurate breakdown of how much power was being used in each particular area. In other words, we needed to be able to visualize the amount of power being consumed. Safety, was also not being managed very rigorously. Even now, tunnel construction sites often use a 'name label' system for managing entry into the work site. Specifically, red labels with white reverse sides that bear the workers' names on both sides are displayed at the tunnel work site entrance. The workers themselves then flip the name label to the appropriate side when entering or exiting from the work site to indicate whether or not they are working inside the tunnel at any given time. If a worker forgets to flip his or her name label when entering or exiting from the tunnel, management cannot be performed effectively. In order to tackle the challenges mentioned above, Zenitaka decided to build a system that could improve the safety of tunnel construction as well as reduce the amount of power consumed. In other words, this new system would facilitate a clear picture of which workers were working in each location at the mountain tunnel construction site, as well as which processes were being carried out at those respective locations at any given time. The system would maintain the safety of all workers while also carefully controlling the electrical equipment to reduce unnecessary power consumption. Having decided on the concept, our next concern was whether there existed any kind of robust hardware that would not break down at the construction work site, that could move freely in response to changes in the working environment, and that could accurately detect workers and vehicles using radio frequency identification (RFID). Given that this system would involve many components that were new to Zenitaka, we decided to enlist the cooperation of E.I.Sol Co., Ltd. ('E.I.Sol') as our joint development partner, as they had provided us with a highly practical proposal.
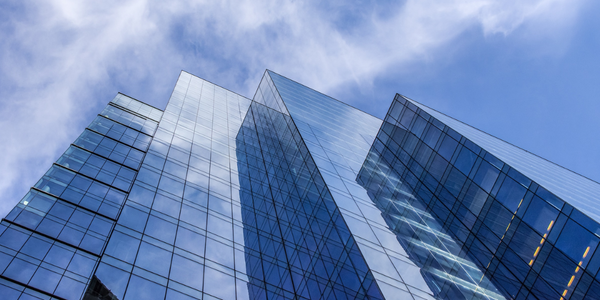
Case Study
Intelligent Building Automation System and Energy Saving Solution
One of the most difficult problems facing the world is conserving energy in buildings. However, it is not easy to have a cost-effective solution to reduce energy usage in a building. One solution for saving energy is to implement an intelligent building automation system (BAS) which can be controlled according to its schedule. In Indonesia a large university with a five floor building and 22 classrooms wanted to save the amount of energy being used.
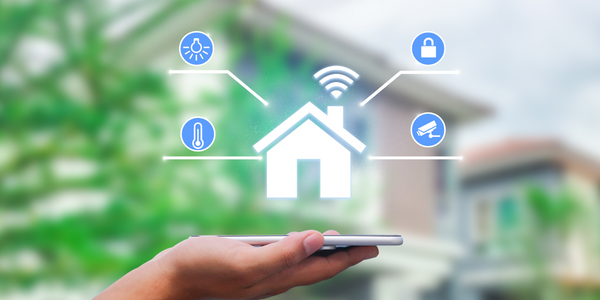
Case Study
Powering Smart Home Automation solutions with IoT for Energy conservation
Many industry leaders that offer Smart Energy Management products & solutions face challenges including:How to build a scalable platform that can automatically scale-up to on-board ‘n’ number of Smart home devicesData security, solution availability, and reliability are the other critical factors to deal withHow to create a robust common IoT platform that handles any kind of smart devicesHow to enable data management capabilities that would help in intelligent decision-making
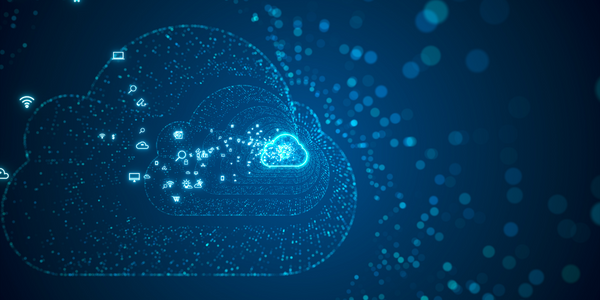
Case Study
Splunk Partnership Ties Together Big Data & IoT Services
Splunk was faced with the need to meet emerging customer demands for interfacing IoT projects to its suite of services. The company required an IoT partner that would be able to easily and quickly integrate with its Splunk Enterprise platform, rather than allocating development resources and time to building out an IoT interface and application platform.