Download PDF
Personalized Automation: FITme's Journey to Increase Productivity by 346% with 3D Printing
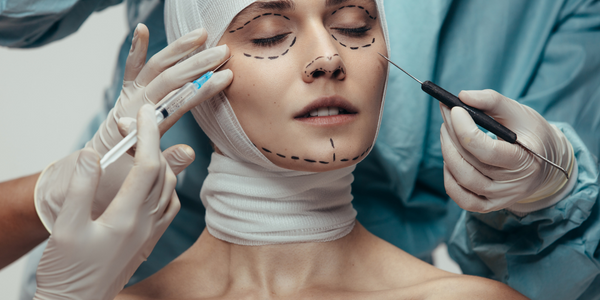
Technology Category
- Platform as a Service (PaaS) - Device Management Platforms
- Wearables - Implants
Applicable Industries
- Buildings
- Healthcare & Hospitals
Applicable Functions
- Product Research & Development
Use Cases
- Mass Customization
- Time Sensitive Networking
Services
- Training
The Challenge
FITme, a Korean-based company specializing in manufacturing implants for facial reconstruction, faced a significant challenge in scaling up their processes for mass personalization. The conventional process of fitting a ready-made silicone implant onto bone structure with manual carving was time-consuming and lacked precision. Surgeons had no tool to analyze patients' scan data and relied solely on photographs. This led to side effects such as bending and movement of the implant, resulting in patient dissatisfaction. The medical tourism industry in Korea was rapidly rising, and FITme had to meet higher demands and reduce lead time. The process of designing custom nasal implants that conformed to the variable shape of patient nasal profiles was a daunting and repetitive task for design engineers. It took up to three months to adequately train new engineers in designing patient implants, which was also expensive.
The Customer
FITme
About The Customer
FITme is a Korean-based company that specializes in manufacturing implants for facial reconstruction. They are pioneers in the field, focusing on 3D printing and engineering to provide better fitting implants and faster service to their patients. They aim to improve their production processes with mass personalization through 3D technology. FITme is committed to reducing the manual effort and time spent designing implants, and they strive to provide a solution that reduces lead time and meets the increasing demands of the rapidly rising medical tourism industry in Korea.
The Solution
FITme collaborated with Materialise to develop a custom plugin that automates the workflow while retaining key manual design steps for the design engineer. The plugin, named FITme Nasal Implant Wizard, streamlined the design process. After the design engineer prepared the segmented parts of the patient, the custom plugin imported the segmented parts as 3D models into 3-matic, where the parts were merged and warped into a single object. The plugin then set the sketches by automatically creating the base and center sketch plane based on the engineer's landmark indication. The sketches auto-aligned to the midface, and the engineer had the flexibility to adjust the sketch planes. Once the engineer completed the sketch, the plugin superimposed the sketch to the nasal structure and created the base profile of the nasal implants. The plugin automatically created the profile of the implant with a single click, perfectly conforming to the unique shape of each patient's nasal bone and cartilage structure.
Operational Impact
Quantitative Benefit
Related Case Studies.
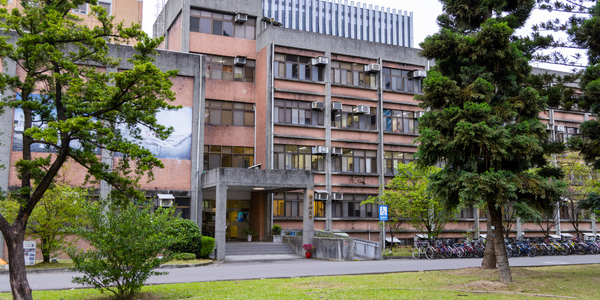
Case Study
Energy Saving & Power Monitoring System
Recently a university in Taiwan was experiencing dramatic power usage increases due to its growing number of campus buildings and students. Aiming to analyze their power consumption and increase their power efficiency across 52 buildings, the university wanted to build a power management system utilizing web-based hardware and software. With these goals in mind, they contacted Advantech to help them develop their system and provide them with the means to save energy in the years to come.
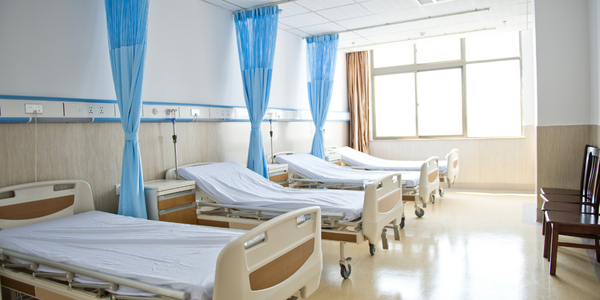
Case Study
Hospital Inventory Management
The hospital supply chain team is responsible for ensuring that the right medical supplies are readily available to clinicians when and where needed, and to do so in the most efficient manner possible. However, many of the systems and processes in use at the cancer center for supply chain management were not best suited to support these goals. Barcoding technology, a commonly used method for inventory management of medical supplies, is labor intensive, time consuming, does not provide real-time visibility into inventory levels and can be prone to error. Consequently, the lack of accurate and real-time visibility into inventory levels across multiple supply rooms in multiple hospital facilities creates additional inefficiency in the system causing over-ordering, hoarding, and wasted supplies. Other sources of waste and cost were also identified as candidates for improvement. Existing systems and processes did not provide adequate security for high-cost inventory within the hospital, which was another driver of cost. A lack of visibility into expiration dates for supplies resulted in supplies being wasted due to past expiry dates. Storage of supplies was also a key consideration given the location of the cancer center’s facilities in a dense urban setting, where space is always at a premium. In order to address the challenges outlined above, the hospital sought a solution that would provide real-time inventory information with high levels of accuracy, reduce the level of manual effort required and enable data driven decision making to ensure that the right supplies were readily available to clinicians in the right location at the right time.
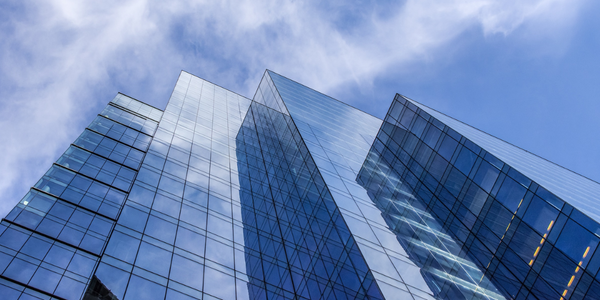
Case Study
Intelligent Building Automation System and Energy Saving Solution
One of the most difficult problems facing the world is conserving energy in buildings. However, it is not easy to have a cost-effective solution to reduce energy usage in a building. One solution for saving energy is to implement an intelligent building automation system (BAS) which can be controlled according to its schedule. In Indonesia a large university with a five floor building and 22 classrooms wanted to save the amount of energy being used.
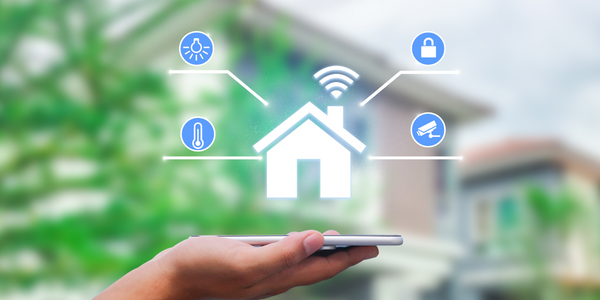
Case Study
Powering Smart Home Automation solutions with IoT for Energy conservation
Many industry leaders that offer Smart Energy Management products & solutions face challenges including:How to build a scalable platform that can automatically scale-up to on-board ‘n’ number of Smart home devicesData security, solution availability, and reliability are the other critical factors to deal withHow to create a robust common IoT platform that handles any kind of smart devicesHow to enable data management capabilities that would help in intelligent decision-making
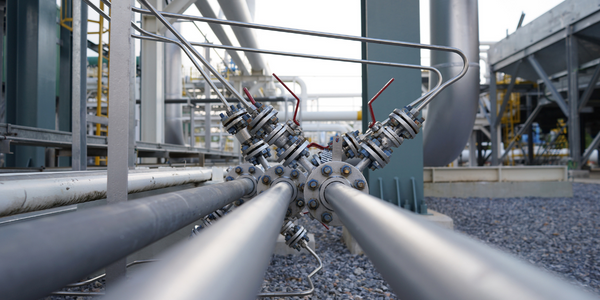
Case Study
Gas Pipeline Monitoring System for Hospitals
This system integrator focuses on providing centralized gas pipeline monitoring systems for hospitals. The service they provide makes it possible for hospitals to reduce both maintenance and labor costs. Since hospitals may not have an existing network suitable for this type of system, GPRS communication provides an easy and ready-to-use solution for remote, distributed monitoring systems System Requirements - GPRS communication - Seamless connection with SCADA software - Simple, front-end control capability - Expandable I/O channels - Combine AI, DI, and DO channels