Download PDF
Quality Furniture Strengthens Lead Times and Costing Accuracy with Lectra’s Upholstery Solutions
Technology Category
- Functional Applications - Product Lifecycle Management Systems (PLM)
- Analytics & Modeling - Predictive Analytics
- Application Infrastructure & Middleware - Data Visualization
Applicable Functions
- Product Research & Development
- Quality Assurance
Use Cases
- Predictive Maintenance
Services
- Software Design & Engineering Services
- System Integration
- Training
The Challenge
Having built a reputation for the fastest and most reliable lead times in the industry, Quality Furniture constantly seeks to pinpoint areas for additional time and cost savings. In particular, the company wanted to bring more products to market faster—both for designs based on client briefs as well as their own original ideas. Seeing the opportunity to cut time and costs from tasks like manual pattern making, drafting with pen and paper, estimating resource usage, and testing prototypes, Quality Furniture sought to implement a CAD solution. They immediately saw that Lectra could handle all their needs—something no other solution could.
About The Customer
Since its start in 1993, Quality Furniture (QFC) has evolved from being a small upholsterer serving a wide customer base, to the UK’s leading manufacturer of entry-level sofas with a focus on a limited number of large national retailers. In 18 years, the company’s turnover has gone from approximately £3 million to just under £25 million, with a track record in designing and supplying some of the UK’s best-selling sofas. QFC focuses on serving customers that operate a stock model—providing them with reliable, cost-effective sofas on an extremely short lead time of seven to ten days. QFC’s major customers include Argos, Homebase, Tesco, Next, Laura Ashley, and Sainsbury’s. The company operates from a 130,000ft2 factory in the East Midlands, employs 240 people, and currently produces approximately 4,000 sofas per week.
The Solution
Having worked successfully together for over 15 years, Quality Furniture turned to Lectra to provide a solution that combines performance and responsiveness to guarantee the build quality of the finished product, significant material savings, and faster time-to-market. According to managing director Vernon Goldberg, “Lectra’s solution was exactly what we were looking for because it did all the surface and solid modeling and gave us the ability to integrate with our own ERP system,” he says. “We can spend more time designing products and less time prototyping. From the product development side, what we did in a week can now be done in a couple of days. We can spend our time adding value, getting rid of waste, and getting leaner—giving us the potential to grow the business significantly without any additional staff.” Lectra’s solution is now an integral part of Quality Furniture’s competitive strategy—solidifying their signature seven-to-ten-day lead time.
Operational Impact
Quantitative Benefit
Related Case Studies.
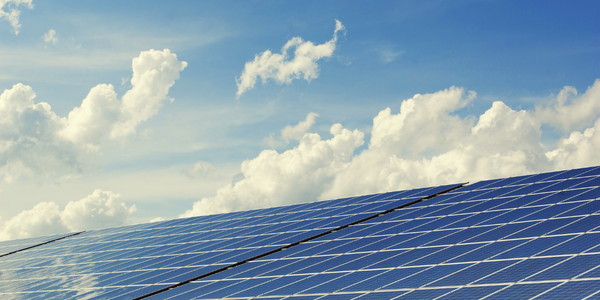
Case Study
Remote Monitoring & Predictive Maintenance App for a Solar Energy System
The maintenance & tracking of various modules was an overhead for the customer due to the huge labor costs involved. Being an advanced solar solutions provider, they wanted to ensure early detection of issues and provide the best-in-class customer experience. Hence they wanted to automate the whole process.
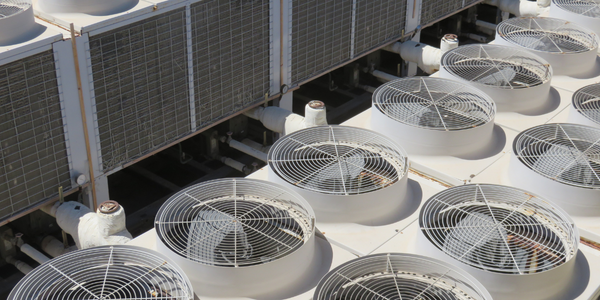
Case Study
Predictive Maintenance for Industrial Chillers
For global leaders in the industrial chiller manufacturing, reliability of the entire production process is of the utmost importance. Chillers are refrigeration systems that produce ice water to provide cooling for a process or industrial application. One of those leaders sought a way to respond to asset performance issues, even before they occur. The intelligence to guarantee maximum reliability of cooling devices is embedded (pre-alarming). A pre-alarming phase means that the cooling device still works, but symptoms may appear, telling manufacturers that a failure is likely to occur in the near future. Chillers who are not internet connected at that moment, provide little insight in this pre-alarming phase.
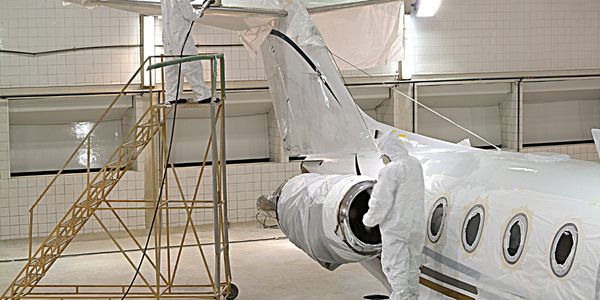
Case Study
Aircraft Predictive Maintenance and Workflow Optimization
First, aircraft manufacturer have trouble monitoring the health of aircraft systems with health prognostics and deliver predictive maintenance insights. Second, aircraft manufacturer wants a solution that can provide an in-context advisory and align job assignments to match technician experience and expertise.
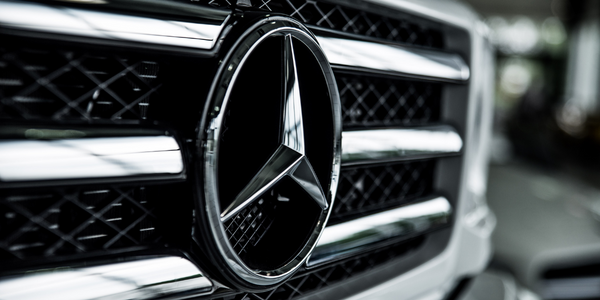
Case Study
Integral Plant Maintenance
Mercedes-Benz and his partner GAZ chose Siemens to be its maintenance partner at a new engine plant in Yaroslavl, Russia. The new plant offers a capacity to manufacture diesel engines for the Russian market, for locally produced Sprinter Classic. In addition to engines for the local market, the Yaroslavl plant will also produce spare parts. Mercedes-Benz Russia and his partner needed a service partner in order to ensure the operation of these lines in a maintenance partnership arrangement. The challenges included coordinating the entire maintenance management operation, in particular inspections, corrective and predictive maintenance activities, and the optimizing spare parts management. Siemens developed a customized maintenance solution that includes all electronic and mechanical maintenance activities (Integral Plant Maintenance).

Case Study
Asset Management and Predictive Maintenance
The customer prides itself on excellent engineering and customer centric philosophy, allowing its customer’s minds to be at ease and not worry about machine failure. They can easily deliver the excellent maintenance services to their customers, but there are some processes that can be automated to deliver less downtime for the customer and more efficient maintenance schedules.