Download PDF
Revolutionizing Custom Bike Manufacturing with 3D Metal Printing: A Triton Bikes Case Study
Technology Category
- Functional Applications - Manufacturing Execution Systems (MES)
Applicable Industries
- Consumer Goods
- Equipment & Machinery
Applicable Functions
- Product Research & Development
Use Cases
- Additive Manufacturing
- Rapid Prototyping
The Challenge
Triton Bikes, a custom titanium bicycle and unicycle frames producer based in Moscow, Russia, was faced with the challenge of improving the performance, reducing the weight, and simplifying the manufacturability of a custom bike rear yoke. The rear yoke, a part of the bicycle’s titanium frame that connects the rear chainstays and the bottom bracket, was initially manufactured using a complex, time-consuming, and wasteful process. The part was CNC milled out of a titanium block in two parts, with some of the material milled out from the inside to save weight. The two halves were then welded together. Triton Bikes wanted to redesign this part to withstand a load equal to 130 kg, reduce its weight, increase its strength, simplify the production technology, and reduce cost.
About The Customer
Triton Bikes is a custom titanium bicycle and unicycle frames producer based in Moscow, Russia. The company is known for its innovative approach to bike design and manufacturing, constantly seeking ways to improve performance, reduce weight, and simplify production processes. Triton Bikes approached CML AT with a potential project to redesign the rear yoke for its latest bike model. The company wanted a solution that would not only enhance the strength and performance of the part but also simplify its production and reduce costs. Triton Bikes is currently working on integrating the new design into their customized bike frame and may explore redesigning other parts of the frame in the future.
The Solution
CML AT, a company specializing in the implementation of additive technologies, partnered with CompMechLab, an engineering center and expert in design, optimization, and simulation tools, to redesign the rear yoke. The team at CompMechLab used solidThinking Inspire to apply all of the loads, shape, and boundary conditions and ran multiple rounds of optimization on the part. The redesign process took less than a couple of weeks. After the final design was determined, they ran FEA analysis to ensure that it would meet all of the required loads. CML AT then organized 3D printing and post-processing of the prototype using electron beam melting technology by Arcam. This allowed the production of the part in Ti6Al4V within a very short time frame. CML AT is now responsible for all future production cooperation, as well as technical support for Triton Bikes.
Operational Impact
Quantitative Benefit
Related Case Studies.
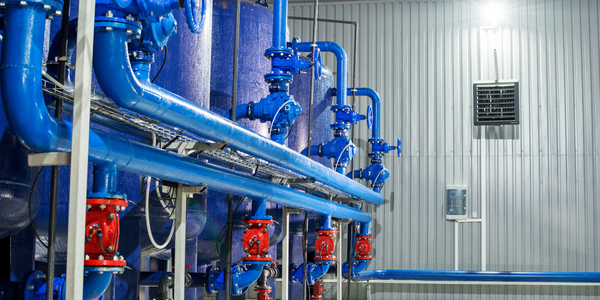
Case Study
Smart Water Filtration Systems
Before working with Ayla Networks, Ozner was already using cloud connectivity to identify and solve water-filtration system malfunctions as well as to monitor filter cartridges for replacements.But, in June 2015, Ozner executives talked with Ayla about how the company might further improve its water systems with IoT technology. They liked what they heard from Ayla, but the executives needed to be sure that Ayla’s Agile IoT Platform provided the security and reliability Ozner required.
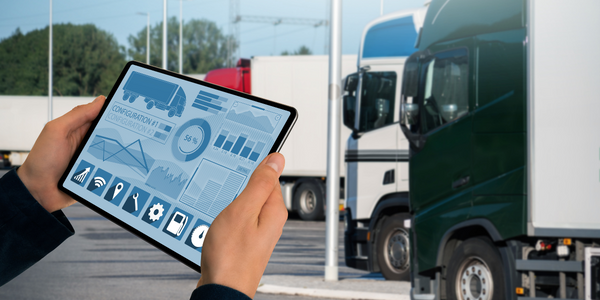
Case Study
IoT enabled Fleet Management with MindSphere
In view of growing competition, Gämmerler had a strong need to remain competitive via process optimization, reliability and gentle handling of printed products, even at highest press speeds. In addition, a digitalization initiative also included developing a key differentiation via data-driven services offers.
.png)
Case Study
Improving Vending Machine Profitability with the Internet of Things (IoT)
The vending industry is undergoing a sea change, taking advantage of new technologies to go beyond just delivering snacks to creating a new retail location. Intelligent vending machines can be found in many public locations as well as company facilities, selling different types of goods and services, including even computer accessories, gold bars, tickets, and office supplies. With increasing sophistication, they may also provide time- and location-based data pertaining to sales, inventory, and customer preferences. But at the end of the day, vending machine operators know greater profitability is driven by higher sales and lower operating costs.
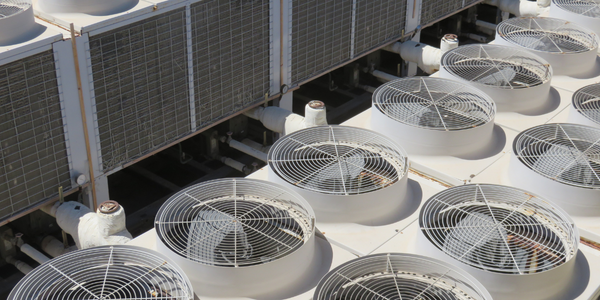
Case Study
Predictive Maintenance for Industrial Chillers
For global leaders in the industrial chiller manufacturing, reliability of the entire production process is of the utmost importance. Chillers are refrigeration systems that produce ice water to provide cooling for a process or industrial application. One of those leaders sought a way to respond to asset performance issues, even before they occur. The intelligence to guarantee maximum reliability of cooling devices is embedded (pre-alarming). A pre-alarming phase means that the cooling device still works, but symptoms may appear, telling manufacturers that a failure is likely to occur in the near future. Chillers who are not internet connected at that moment, provide little insight in this pre-alarming phase.
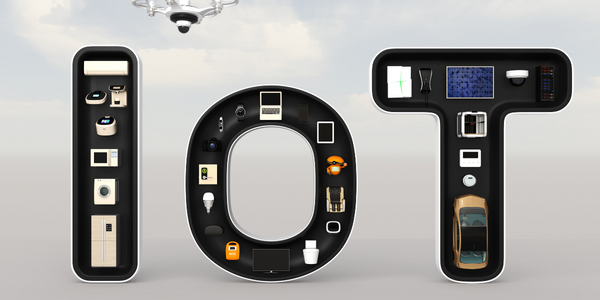
Case Study
Premium Appliance Producer Innovates with Internet of Everything
Sub-Zero faced the largest product launch in the company’s history:It wanted to launch 60 new products as scheduled while simultaneously opening a new “greenfield” production facility, yet still adhering to stringent quality requirements and manage issues from new supply-chain partners. A the same time, it wanted to increase staff productivity time and collaboration while reducing travel and costs.