Download PDF
Revolutionizing Heat Exchanger Design with IoT: A Case Study on GEA Ecoflex India Pvt. Ltd.
Technology Category
- Analytics & Modeling - Digital Twin / Simulation
- Sensors - Utility Meters
Applicable Functions
- Maintenance
- Product Research & Development
Use Cases
- Manufacturing Process Simulation
- Virtual Prototyping & Product Testing
The Challenge
GEA Ecoflex India Pvt. Ltd., a part of the Global Engineering Alliance Group, operates in the competitive heat exchanger sector. The company's primary challenge was to expedite the product development process while ensuring the heat exchangers met client technical specifications for safety, space, environmental concerns, structural integrity, and international standards. The company needed to reduce prototyping time to deliver innovative products to the market first and grow its business. The heat exchangers, being a vital element in a wide range of industries, had to deliver excellent return on investment, reliable operation, and reduced maintenance costs for the companies using them.
About The Customer
GEA Ecoflex India Pvt. Ltd. is a part of the Global Engineering Alliance Group (GEA) PHE Systems, responsible for plate heat exchanger technology within the GEA Heat Exchangers segment of the GEA Group. The GEA Group is one of the largest system providers for food and energy processes. GEA Ecoflex focuses on process technology and components for sophisticated production processes. The company is based in Pune, India, and leads the GEA family in quantifying PHE performance characteristics.
The Solution
GEA Ecoflex adopted a simulation-driven product development approach using ANSYS Mechanical and ANSYS Fluent. The company modeled and simulated plate heat exchangers (PHEs) using a 2-D/3-D model for a set of design data and technical specifications. They applied structural, thermal, and seismic load case combinations to determine the static and dynamic behavior of the PHE, enabling them to predict actual performance in the field. The PHEs were optimized with multiphysics simulation from ANSYS. This approach allowed GEA Ecoflex to manufacture the PHEs to meet technical specifications and comply with standards, while significantly reducing the design and development cycle.
Operational Impact
Quantitative Benefit
Related Case Studies.
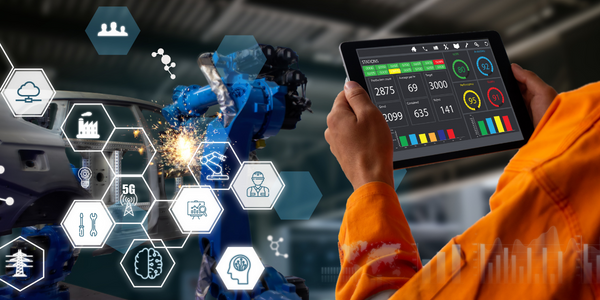
Case Study
Battery manufacturer Industrial Digital Twin
For optimum control of product quality, Banner relies on a high production depth. Its 560 production employees produce nearly all the components in¬-house that they need to make finished batteries on Banner’s six assembly lines. This includes the plastic parts for the battery cases as well as the paste-filled lead oxide grids. Their production involves two to five¬ days rest in maturing chambers to create optimum current absorption and storage capacity. Banner’s ongoing success was accompanied by a continuous, organic growth of the production facilities, adding or extending hall after hall until the complex filled the site that had seemed ever so spacious when the company moved here from a smaller place in 1959. These developments led to a heterogeneous production environment. “This confronts us with significant challenges, particularly concerning intra¬logistics issues, such as scheduling for the maturing chambers,” says Franz Dorninger, technical director at Banner. “We contemplated various ways to overcome this problem, including relocating to new premises.”
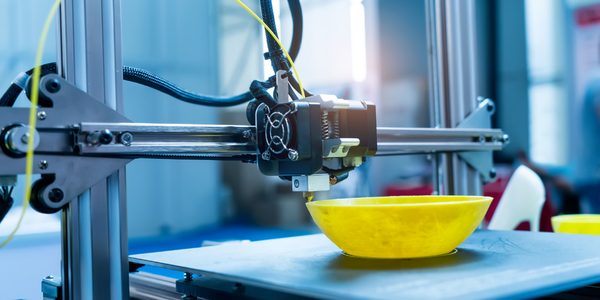
Case Study
Intralox Using Demo3D Case Study
Intralox strives to create significant economic value for our customers by optimizing their conveyance systems. Intralox wants to emulate real-world production environments for end users and OEMs working in multiple industries, including packaging, warehousing, parcel, beverage, brewery, food, tire, and consumer goods. They frequently had to perform physical tests to demonstrate to customers how ARB equipment would handle their products.
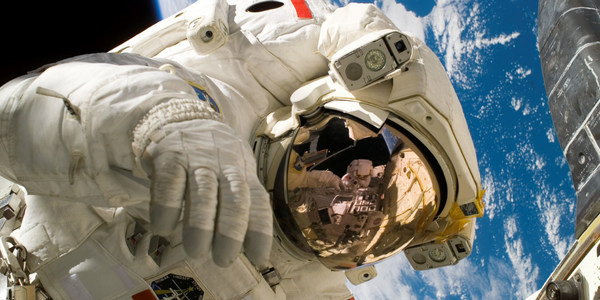
Case Study
General Dynamics Uses Wind River Simics to Meet NASA Challenge
In designing and building Fermi, the General Dynamics C4 Systems business unit was faced with a challenge: it needed to provide an environment that could support rigorous testing by multiple Fermi subsystem groups before the spacecraft hardware was available.