Download PDF
Revolutionizing Process Management in Real Estate and Medical Equipment Industry: A Case Study of Sichuan Languang Development Co., Ltd. (BRC)
Technology Category
- Analytics & Modeling - Process Analytics
Applicable Industries
- Education
- Mining
Applicable Functions
- Human Resources
- Product Research & Development
Use Cases
- Process Control & Optimization
- Virtual Training
Services
- Training
The Challenge
Sichuan Languang Development Co., Ltd. (BRC), a company with over 20,000 employees and 390+ enterprises, was facing significant challenges in managing its vast documentation. The company had over 8,000 documents about systems, processes, specifications, and guidelines that were not updated in a timely manner. This lack of organization and timely updates impacted the implementation of systems, affecting workers' efficiency. Additionally, training new employees was a time-consuming process due to the scattered and unorganized training materials. The company needed to coordinate the participation of business personnel from multiple departments, which was difficult to control. This often resulted in confusion and a slow start for new employees.
About The Customer
Sichuan Languang Development Co., Ltd. (BRC) is a company established in 1990 that develops and markets tourism, residential, office, entertainment, and restaurant real estate. It also develops and sells medical equipment and medicine products. The company operates in China with more than 20,000 employees and over 390 holding and participating enterprises. BRC is responsible for creating detailed and meticulously documented rules and guidelines for its 390+ properties, which had grown to more than 8 million words across 8,000 separate documents.
The Solution
To address these challenges, BRC decided to implement a process management solution. After an extensive search, the company chose ARIS in 2019. ARIS's process management platform helped BRC organize its scattered processes and documents. It created a one-stop operation with identifiers such as 'who I am,' 'what I do,' and 'how I do it.' This allowed employees to quickly locate their position and job content within the process. ARIS also helped clarify the complex relationships among personnel, position, role, and process. It provided a panoramic presentation of the value chain, offering analysis reports for process optimization. Furthermore, ARIS established a long-term operation mechanism of process governance, supporting the flexible adjustment of business, organization, power, and responsibility. The second stage of BRC's project in 2021 will include a proof of concept for ARIS Process Mining.
Operational Impact
Quantitative Benefit
Related Case Studies.
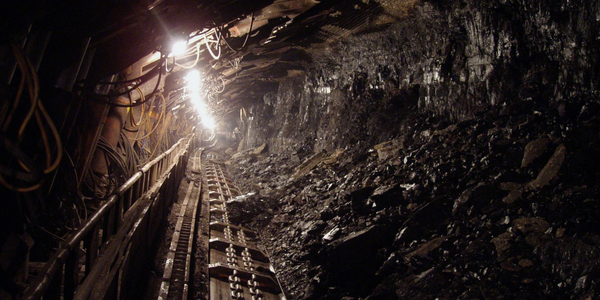
Case Study
Underground Mining Safety
The goal was to produce a safety system to monitor and support underground mining operations; existing systems were either too simple (i.e. phone line) or overly complex and expensive, inhibiting deployment, and providing little-to-no support in event of an accident. Given the dangerous nature of the mining work environment and the strict regulations placed on the industry, the solution would have to comply with Mine Safety and Health Administration (MSHA) regulations. Yet the product needed to allow for simple deployment to truly be a groundbreaking solution - increasing miner safety and changing daily operations for the better.
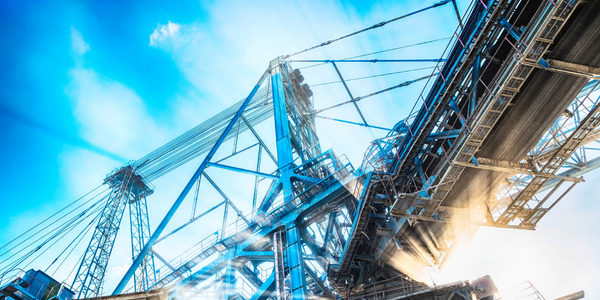
Case Study
Mining Firm Quadruples Production, with Internet of Everything
Dundee Precious Metal’s flagship mine, in Chelopech, Bulgaria, produces a gold, copper, and silver concentrate set a goal to increase production by 30%. Dundee wanted to increase production quality and output without increasing headcount and resources, improve miner safety, and minimize cost.
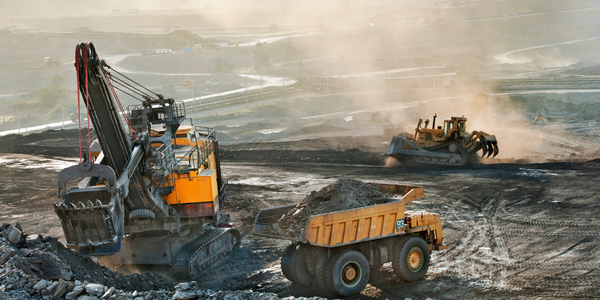
Case Study
Fastenal Builds the Future of Manufacturing with MachineMetrics
Fastenal's objective was to better understand their machine downtime, utilization, quality issues, and to embrace cutting-edge manufacturing technology/process improvement capabilities to bring their team to the next level. However, there was a lack of real-time data, visualization, and actionable insights made this transition impossible.
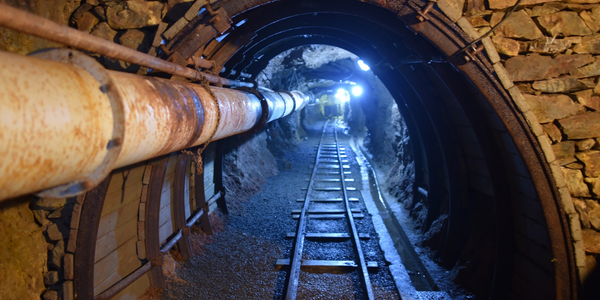
Case Study
Joy Mining Systems
Joy equipment faces many challenges. The first is machine integration and control. The business end of the machine has a rapidly-spinning cylinder with 6-inch diamond-studded cutting teeth. It chews through rock at rates measured in tens of tons per minute. The system grinds through the rock in front, creating a rectangular mine tunnel. Hydraulic lifters support the ceiling as the machine moves forward. Automated drills and screws drive 3-ft long screws into the ceiling to stabilize it. The rock and coal fall into a set of gathering "fingers" below the cutting cylinder. These fingers scoop up the rock and coal and deposit it onto a conveyor belt. The conveyor passes under the machine and out the back. A train of conveyor belt cars, up to a mile long, follows the cutter into the mine. The rock shoots along this train at over 400 feet per minute until it empties into rail cars at the end. Current systems place an operator cage next to the cutter. Choking dust (potentially explosive), the risk of collapse and the proximity of metal and rock mayhem make the operator cage a hazardous location.
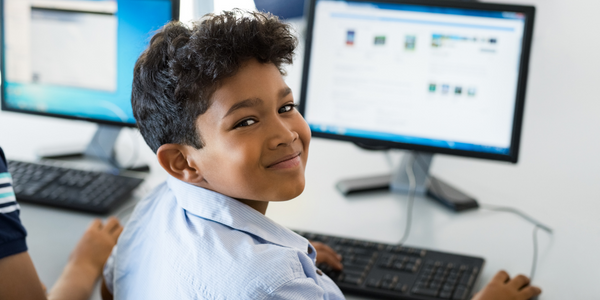
Case Study
IoT platform Enables Safety Solutions for U.S. School Districts
Designed to alert drivers when schoolchildren are present, especially in low-visibility conditions, school-zone flasher signals are typically updated manually at each school. The switching is based on the school calendar and manually changed when an unexpected early dismissal occurs, as in the case of a weather-event altering the normal schedule. The process to reprogram the flashers requires a significant effort by school district personnel to implement due to the large number of warning flashers installed across an entire school district.