Download PDF
Scalability and Transparency Enhancement in Orion Registrar's Certification Process
Technology Category
- Application Infrastructure & Middleware - Event-Driven Application
- Infrastructure as a Service (IaaS) - Cloud Databases
Applicable Functions
- Quality Assurance
Use Cases
- Inventory Management
- Time Sensitive Networking
Services
- System Integration
- Testing & Certification
The Challenge
Orion Registrar, an internationally accredited provider of auditing services, was facing a significant challenge with its existing certification process. The process, built using Microsoft Access and a custom-built CRM solution, was not providing the scalability and flexibility needed to meet the company's growth trajectory. As the company expanded, it became clear that the existing system was not equipped to handle the increasing volume of work and the need for real-time updates for customers and auditors. The company needed a solution that could not only handle the growing business but also continue to provide a high level of customer service.
About The Customer
Orion Registrar is an internationally accredited provider of auditing services. The company acts as a certification body for companies looking to bring new solutions to market. As part of its services, Orion Registrar had built an end-to-end certification process. However, as the company grew, it realized the need for a more scalable and flexible solution that could handle the increasing volume of work and provide real-time updates to customers and auditors. The company is based in the United States and operates in the professional services industry.
The Solution
In response to this challenge, Orion Registrar collaborated with technology partner Catalyte to implement a new certification process. This process was integrated with Orion's on-premises and cloud-based systems, creating a comprehensive system that included a cloud infrastructure, content management system, a collaborative work environment, extensive document management, and business application integration. The core of this new certification solution was Nintex K2 Five, a process automation tool. This tool provided a predictable, reliable, and scalable solution for Orion's certification process. It also included an externally facing portal where customers and auditors could gain a real-time view of the status and issues with their pending certification.
Operational Impact
Quantitative Benefit
Related Case Studies.
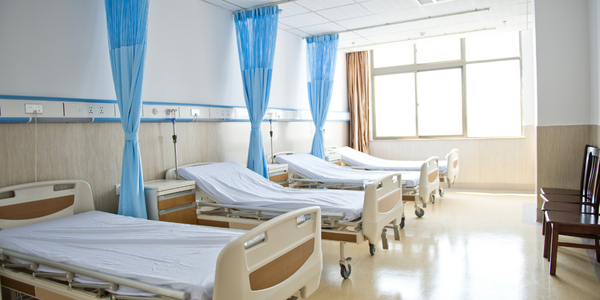
Case Study
Hospital Inventory Management
The hospital supply chain team is responsible for ensuring that the right medical supplies are readily available to clinicians when and where needed, and to do so in the most efficient manner possible. However, many of the systems and processes in use at the cancer center for supply chain management were not best suited to support these goals. Barcoding technology, a commonly used method for inventory management of medical supplies, is labor intensive, time consuming, does not provide real-time visibility into inventory levels and can be prone to error. Consequently, the lack of accurate and real-time visibility into inventory levels across multiple supply rooms in multiple hospital facilities creates additional inefficiency in the system causing over-ordering, hoarding, and wasted supplies. Other sources of waste and cost were also identified as candidates for improvement. Existing systems and processes did not provide adequate security for high-cost inventory within the hospital, which was another driver of cost. A lack of visibility into expiration dates for supplies resulted in supplies being wasted due to past expiry dates. Storage of supplies was also a key consideration given the location of the cancer center’s facilities in a dense urban setting, where space is always at a premium. In order to address the challenges outlined above, the hospital sought a solution that would provide real-time inventory information with high levels of accuracy, reduce the level of manual effort required and enable data driven decision making to ensure that the right supplies were readily available to clinicians in the right location at the right time.
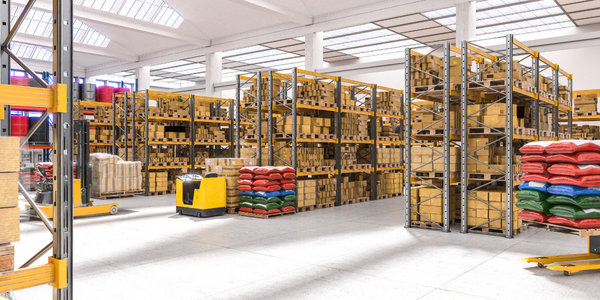
Case Study
Hardware Retailer Uses Data Warehouse to Track Inventory
Ace tracked which products retailers ordered, when they were ordered and shipped. However, the company could not track or forecast actual sales. Data used for reporting was up to a one-week old, owing to performance and data cleansing issues. Requirement to integrate wholesale and inventory data with POS data to help drive key business decisions, improve category management, lower inventory costs and optimize pricing. Reliance on custom coding to integrate POS data was excessively resource intensive and led to major performance constraints.
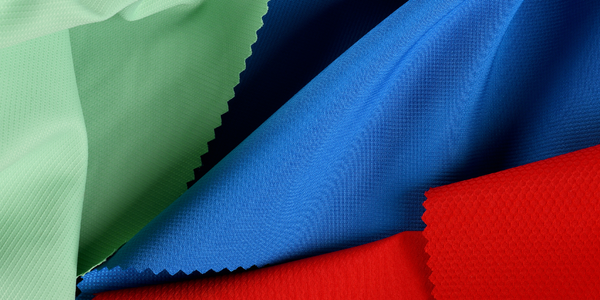
Case Study
Remake Enterprise-to-production System
The client was running a legacy material flow tracking system and wanted to replace the system with a more effective one as the system was increasingly expensive to maintain and support and also was not extendable. The client's IT landscape was filled with modern applications and it was difficult to interface the material flow tracking system with modern applications.