Download PDF
Scaling a Small Data Team with the Power of Machine Learning
Technology Category
- Analytics & Modeling - Machine Learning
- Analytics & Modeling - Predictive Analytics
- Analytics & Modeling - Natural Language Processing (NLP)
Applicable Functions
- Sales & Marketing
Use Cases
- Predictive Maintenance
Services
- Data Science Services
The Challenge
DAZN, a subscription sports streaming service, was looking to grow their business in existing and new markets. They wanted to enable their small data team to run predictive analytics and machine learning projects at scale. They also wanted to find a way to allow data analysts who were not necessarily technical or experienced in machine learning to contribute in meaningful ways to impactful data projects. The goal was to support an underlying data culture with advanced analytics and machine learning at the heart of the business.
About The Customer
DAZN is a subscription service owned by Perform Group dedicated to live and on-demand streaming of worldwide sporting events. It offers access to more than 8,000 sporting events a year across a wide range of devices to customers in Austria, Germany, Japan, Switzerland, and Canada, with more markets coming soon. In an effort to continue to grow their business in existing and new markets, DAZN wanted a fast, low-maintenance way to enable their small data team to run predictive analytics and machine learning projects at scale.
The Solution
DAZN turned to Amazon Web Services (AWS) and Dataiku Data Science Studio (DSS) for their simplicity in setup, connection, integration, and usability. They were able to get up and running in under one hour. With AWS and Dataiku, the small data team built and now manages more than 30 models in parallel, all without needing to do any coding so that the processes are completely accessible to non-technical team members. They use these models as the basis for a variety of critical processes throughout all areas of the business, including content attribution, advanced customer segmentation, propensity modeling, survival analysis, and natural language processing on social networks for market research.
Operational Impact
Quantitative Benefit
Related Case Studies.
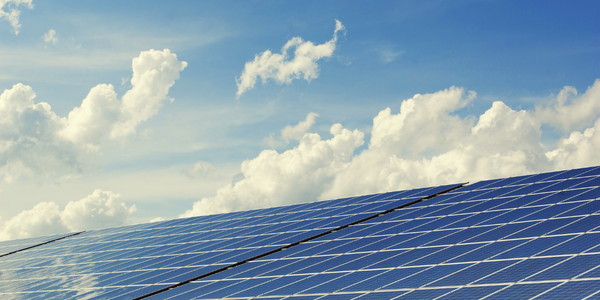
Case Study
Remote Monitoring & Predictive Maintenance App for a Solar Energy System
The maintenance & tracking of various modules was an overhead for the customer due to the huge labor costs involved. Being an advanced solar solutions provider, they wanted to ensure early detection of issues and provide the best-in-class customer experience. Hence they wanted to automate the whole process.
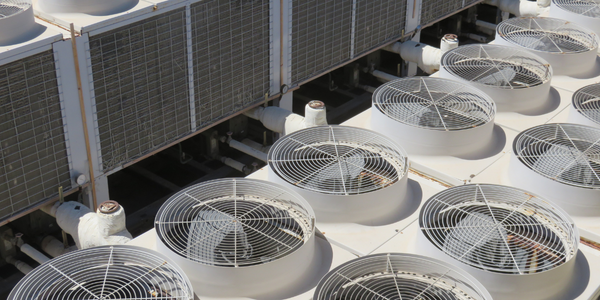
Case Study
Predictive Maintenance for Industrial Chillers
For global leaders in the industrial chiller manufacturing, reliability of the entire production process is of the utmost importance. Chillers are refrigeration systems that produce ice water to provide cooling for a process or industrial application. One of those leaders sought a way to respond to asset performance issues, even before they occur. The intelligence to guarantee maximum reliability of cooling devices is embedded (pre-alarming). A pre-alarming phase means that the cooling device still works, but symptoms may appear, telling manufacturers that a failure is likely to occur in the near future. Chillers who are not internet connected at that moment, provide little insight in this pre-alarming phase.
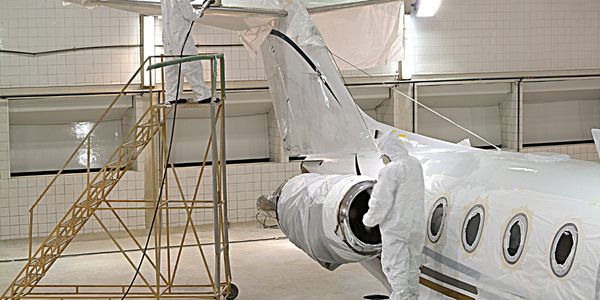
Case Study
Aircraft Predictive Maintenance and Workflow Optimization
First, aircraft manufacturer have trouble monitoring the health of aircraft systems with health prognostics and deliver predictive maintenance insights. Second, aircraft manufacturer wants a solution that can provide an in-context advisory and align job assignments to match technician experience and expertise.
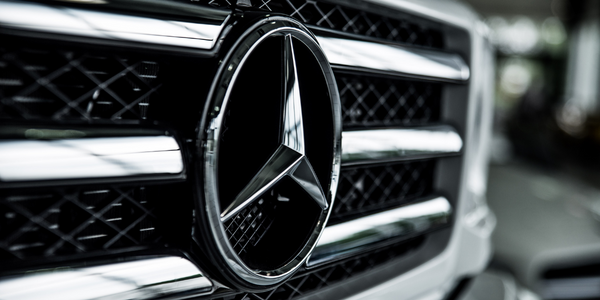
Case Study
Integral Plant Maintenance
Mercedes-Benz and his partner GAZ chose Siemens to be its maintenance partner at a new engine plant in Yaroslavl, Russia. The new plant offers a capacity to manufacture diesel engines for the Russian market, for locally produced Sprinter Classic. In addition to engines for the local market, the Yaroslavl plant will also produce spare parts. Mercedes-Benz Russia and his partner needed a service partner in order to ensure the operation of these lines in a maintenance partnership arrangement. The challenges included coordinating the entire maintenance management operation, in particular inspections, corrective and predictive maintenance activities, and the optimizing spare parts management. Siemens developed a customized maintenance solution that includes all electronic and mechanical maintenance activities (Integral Plant Maintenance).

Case Study
Asset Management and Predictive Maintenance
The customer prides itself on excellent engineering and customer centric philosophy, allowing its customer’s minds to be at ease and not worry about machine failure. They can easily deliver the excellent maintenance services to their customers, but there are some processes that can be automated to deliver less downtime for the customer and more efficient maintenance schedules.