Download PDF
Sharda Motors: Leveraging Altair CAE Solution for Durability Analysis in Automobile Manufacturing
Technology Category
- Analytics & Modeling - Digital Twin / Simulation
- Functional Applications - Manufacturing Execution Systems (MES)
Applicable Industries
- Automotive
- Buildings
Applicable Functions
- Facility Management
- Product Research & Development
Use Cases
- Manufacturing Process Simulation
- Time Sensitive Networking
Services
- Hardware Design & Engineering Services
- System Integration
The Challenge
Sharda Motor Industries Limited (SMIL), a market leader in the manufacturing of exhaust systems and other automobile components, was faced with the challenge of reducing product design and development cycle time, effort, and cost. The company aimed to provide innovative products to clients by using simulation, automation, and optimization technologies in the development of exhaust components and systems. The challenge was to evaluate the durability of exhaust system components within a given time frame with high accuracy. They were expected to carry out finite element analysis and explain the results for typical exhaust system components. They also had to consider durability loads such as engine vibration loading and proving ground road-loads. Other durability issues associated with exhaust system components such as the muffler-pipe system, brackets, and hanger designs were required to be analyzed.
About The Customer
Sharda Motor Industries Limited (SMIL) is a leading manufacturer in the country of exhaust systems, catalytic converters, independent suspension systems, seat frames, seat covers, soft top canopies, and stamped part for white goods products. They believe in maintaining the highest quality standards in the entire product development life cycle. Their state-of-the-art manufacturing facilities help them to continuously focus on new products, innovation, technology upgradation, and research & development. SMIL supplies exhaust systems to major automobile companies like Mahindra, TATA, Hyundai, Force Motors, and SML ISUZU in the country. They support all their clients through cutting-edge research and enable them to produce world-class engineering products.
The Solution
To meet their simulation software needs for concept and product design and development, SMIL decided to use the Altair Suite. The SMIL team evaluated the durability of exhaust system components by CAE simulation using Altair HyperWorks. They carried out finite element analysis and explained the results for typical exhaust system components considering various types of durability loads. They also examined durability issues related to other exhaust system components. The team carried out Finite element modeling for passenger car exhaust systems using Altair’s pre-processing tool HyperMesh and performed Static Analysis by using OptiStruct FEA for exhaust components to determine high-stress regions. They followed this up by using the S-N approach for calculating the fatigue life of exhaust system components with the help of HyperWorks and Fatigue Process Manager (FPM) in OptiStruct FEA. The results were viewed through Altair’s post-processing tool HyperView.
Operational Impact
Quantitative Benefit
Related Case Studies.
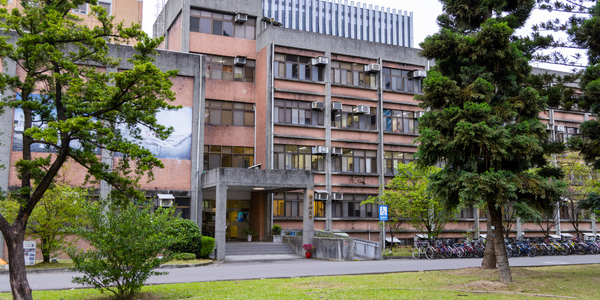
Case Study
Energy Saving & Power Monitoring System
Recently a university in Taiwan was experiencing dramatic power usage increases due to its growing number of campus buildings and students. Aiming to analyze their power consumption and increase their power efficiency across 52 buildings, the university wanted to build a power management system utilizing web-based hardware and software. With these goals in mind, they contacted Advantech to help them develop their system and provide them with the means to save energy in the years to come.
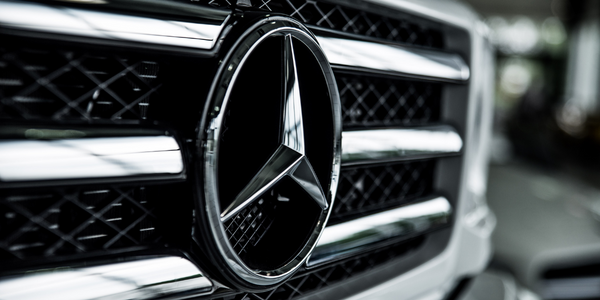
Case Study
Integral Plant Maintenance
Mercedes-Benz and his partner GAZ chose Siemens to be its maintenance partner at a new engine plant in Yaroslavl, Russia. The new plant offers a capacity to manufacture diesel engines for the Russian market, for locally produced Sprinter Classic. In addition to engines for the local market, the Yaroslavl plant will also produce spare parts. Mercedes-Benz Russia and his partner needed a service partner in order to ensure the operation of these lines in a maintenance partnership arrangement. The challenges included coordinating the entire maintenance management operation, in particular inspections, corrective and predictive maintenance activities, and the optimizing spare parts management. Siemens developed a customized maintenance solution that includes all electronic and mechanical maintenance activities (Integral Plant Maintenance).
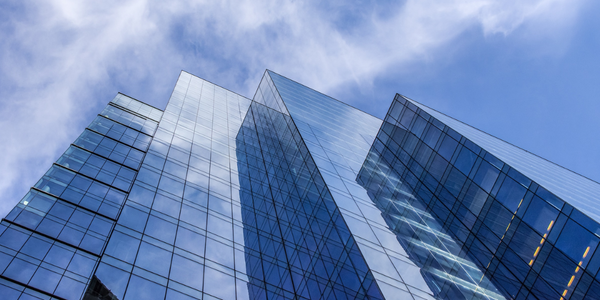
Case Study
Intelligent Building Automation System and Energy Saving Solution
One of the most difficult problems facing the world is conserving energy in buildings. However, it is not easy to have a cost-effective solution to reduce energy usage in a building. One solution for saving energy is to implement an intelligent building automation system (BAS) which can be controlled according to its schedule. In Indonesia a large university with a five floor building and 22 classrooms wanted to save the amount of energy being used.
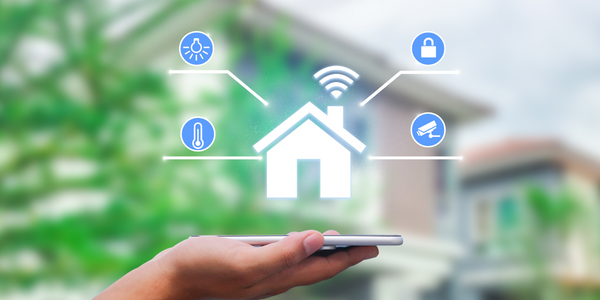
Case Study
Powering Smart Home Automation solutions with IoT for Energy conservation
Many industry leaders that offer Smart Energy Management products & solutions face challenges including:How to build a scalable platform that can automatically scale-up to on-board ‘n’ number of Smart home devicesData security, solution availability, and reliability are the other critical factors to deal withHow to create a robust common IoT platform that handles any kind of smart devicesHow to enable data management capabilities that would help in intelligent decision-making