Download PDF
SOHO Realty Enhances Real Estate Processes with Nintex Automation
Technology Category
- Analytics & Modeling - Process Analytics
- Analytics & Modeling - Robotic Process Automation (RPA)
Applicable Functions
- Procurement
- Sales & Marketing
Use Cases
- Inventory Management
- Process Control & Optimization
The Challenge
SOHO Realty, a full-service boutique real estate brokerage, was facing challenges in managing its sales and marketing processes. The agency was already using dotloop, a transaction management tool, for managing electronic signatures and other documentation needs. However, it was not a complete solution. The agency needed a more comprehensive system to automate the delivery of documents, track the status of tasks in the home buying and selling process, and manage incoming leads from both buyers and sellers. The existing system was not efficient enough to ensure proper and fast follow-ups. Moreover, the agency wanted to make the home buying process less complicated and easier for its clients, who were mostly first-time buyers.
About The Customer
SOHO Realty, Inc is a full-service boutique real estate brokerage based in the United States. The agency operates in the Houston and Atlanta markets, helping its clients, who are mostly first-time buyers, achieve their real estate goals. The agency is committed to improving the home buying process and making it less complicated for its clients. It uses a customer-first approach, focusing on efficient collaboration between its agents and customers, and ensuring that all sales process steps and procedures are properly executed.
The Solution
To address these challenges, SOHO Realty partnered with Optimum, a modern software and digital solutions consulting firm. Optimum developed a customized CRM for SOHO Realty using Nintex for Office 365. The solution was designed around the way SOHO operates and included one advanced and fully customized Nintex Forms and three Nintex Workflows. The solution starts with the agency’s online inquiries webform. Once completed and submitted, the information is added to SOHO Realty’s CRM which triggers a Nintex Workflow that notifies a SOHO Realty sales rep to follow up with the lead. The sales rep collects more information, entering it into the Nintex Form. If the lead is qualified, the customer is assigned to an agent, who is notified via the Nintex Workflow. As the sales journey progresses, the agent continues to use the Nintex Form to collect more information and, if applicable, kicks off a workflow to add the buying or selling and other legal documents to dotloop.
Operational Impact
Quantitative Benefit
Related Case Studies.
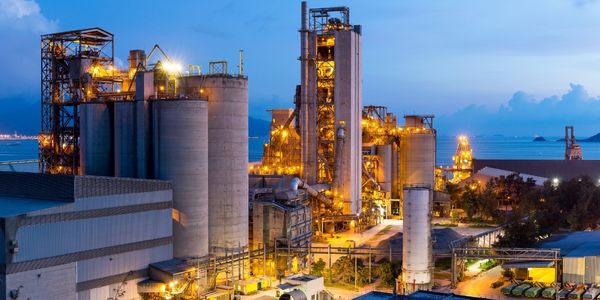
Case Study
System 800xA at Indian Cement Plants
Chettinad Cement recognized that further efficiencies could be achieved in its cement manufacturing process. It looked to investing in comprehensive operational and control technologies to manage and derive productivity and energy efficiency gains from the assets on Line 2, their second plant in India.
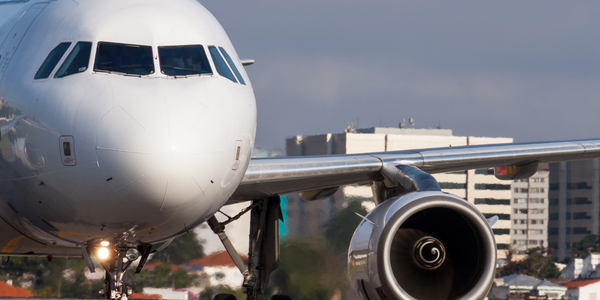
Case Study
Airbus Soars with Wearable Technology
Building an Airbus aircraft involves complex manufacturing processes consisting of thousands of moving parts. Speed and accuracy are critical to business and competitive advantage. Improvements in both would have high impact on Airbus’ bottom line. Airbus wanted to help operators reduce the complexity of assembling cabin seats and decrease the time required to complete this task.
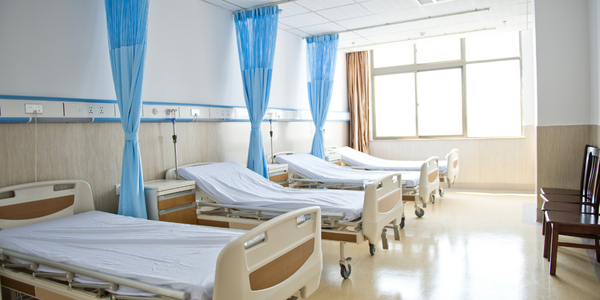
Case Study
Hospital Inventory Management
The hospital supply chain team is responsible for ensuring that the right medical supplies are readily available to clinicians when and where needed, and to do so in the most efficient manner possible. However, many of the systems and processes in use at the cancer center for supply chain management were not best suited to support these goals. Barcoding technology, a commonly used method for inventory management of medical supplies, is labor intensive, time consuming, does not provide real-time visibility into inventory levels and can be prone to error. Consequently, the lack of accurate and real-time visibility into inventory levels across multiple supply rooms in multiple hospital facilities creates additional inefficiency in the system causing over-ordering, hoarding, and wasted supplies. Other sources of waste and cost were also identified as candidates for improvement. Existing systems and processes did not provide adequate security for high-cost inventory within the hospital, which was another driver of cost. A lack of visibility into expiration dates for supplies resulted in supplies being wasted due to past expiry dates. Storage of supplies was also a key consideration given the location of the cancer center’s facilities in a dense urban setting, where space is always at a premium. In order to address the challenges outlined above, the hospital sought a solution that would provide real-time inventory information with high levels of accuracy, reduce the level of manual effort required and enable data driven decision making to ensure that the right supplies were readily available to clinicians in the right location at the right time.
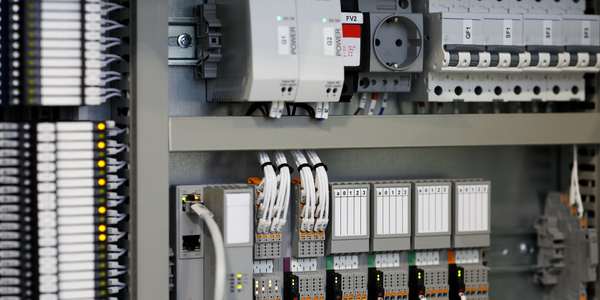
Case Study
Improving Production Line Efficiency with Ethernet Micro RTU Controller
Moxa was asked to provide a connectivity solution for one of the world's leading cosmetics companies. This multinational corporation, with retail presence in 130 countries, 23 global braches, and over 66,000 employees, sought to improve the efficiency of their production process by migrating from manual monitoring to an automatic productivity monitoring system. The production line was being monitored by ABB Real-TPI, a factory information system that offers data collection and analysis to improve plant efficiency. Due to software limitations, the customer needed an OPC server and a corresponding I/O solution to collect data from additional sensor devices for the Real-TPI system. The goal is to enable the factory information system to more thoroughly collect data from every corner of the production line. This will improve its ability to measure Overall Equipment Effectiveness (OEE) and translate into increased production efficiencies. System Requirements • Instant status updates while still consuming minimal bandwidth to relieve strain on limited factory networks • Interoperable with ABB Real-TPI • Small form factor appropriate for deployment where space is scarce • Remote software management and configuration to simplify operations