Download PDF
Streamlining the Development Process of Glass Fiber Composite Products with IoT
Technology Category
- Analytics & Modeling - Digital Twin / Simulation
- Networks & Connectivity - Ethernet
Applicable Industries
- Automotive
- Glass
Applicable Functions
- Product Research & Development
Use Cases
- Manufacturing Process Simulation
- Virtual Reality
The Challenge
Valeo, a leading automotive supplier, was faced with the challenge of covering a broad range of simulation tasks for model preparation of glass fiber polymer composite parts. The company was focused on lightweight design with the primary aim of reducing CO2 emissions and achieving improved fuel consumption. The typical development process involved model generation and preparation, the actual solving, post-processing, and result interpretation. However, due to regulatory requirements for CO2 emissions and the overall need in the automotive industry for better fuel efficiency, it was becoming increasingly important to consider lightweight issues within the development of automotive parts. This drive for lightweight design required new and lighter materials in vehicles. The challenge was to make these processes as efficient as possible while keeping software investments low. For continuous improvement, Valeo validates its development processes each year, always on the lookout for additional efficient tools to handle the simulations involved in their development processes.
About The Customer
Valeo is an independent industrial group fully focused on the design, production, and sale of components, integrated systems, and modules for the automotive industry. It ranks among the world's top automotive suppliers. The group has 124 plants, 20 research centers, 35 development centers, 12 distribution platforms, and employs 73,300 people in 28 countries worldwide. One of its major focuses is on lightweight design, with the primary aim of reducing CO2 emissions and achieving improved fuel consumption. At Valeo Lighting Systems (VLS), one of the company’s Business Groups, engineers focus on the virtual development of head and rear lamps.
The Solution
Valeo found a solution in Altair’s HyperWorks CAE Suite and CONVERSE by PART Engineering. The Altair Partner Alliance (APA) program allowed Valeo to access third-party partner products with the same license units the customers use for HyperWorks. This allowed Valeo engineers in China to use the APA product CONVERSE, by Part Engineering, to prepare their models of reinforced glass fiber parts for the FE simulation. When a new part was designed, CONVERSE helped them to consider anisotropic characteristics of the material, emerging during the manufacturing process. Bridging the gap between injection molding simulation and mechanical simulation was especially valuable for the Valeo development teams. By including it in their development process, the engineers received more reliable and accurate results with regard to stiffness and strength of shortfiber-reinforced molded parts. This was achieved by enabling the user to consider anisotropic material properties such as fiber orientations in a mechanical simulation of the molded part.
Operational Impact
Quantitative Benefit
Related Case Studies.
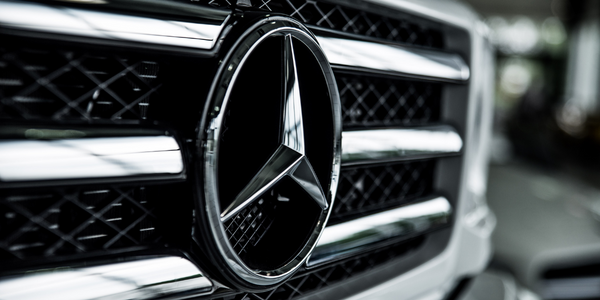
Case Study
Integral Plant Maintenance
Mercedes-Benz and his partner GAZ chose Siemens to be its maintenance partner at a new engine plant in Yaroslavl, Russia. The new plant offers a capacity to manufacture diesel engines for the Russian market, for locally produced Sprinter Classic. In addition to engines for the local market, the Yaroslavl plant will also produce spare parts. Mercedes-Benz Russia and his partner needed a service partner in order to ensure the operation of these lines in a maintenance partnership arrangement. The challenges included coordinating the entire maintenance management operation, in particular inspections, corrective and predictive maintenance activities, and the optimizing spare parts management. Siemens developed a customized maintenance solution that includes all electronic and mechanical maintenance activities (Integral Plant Maintenance).
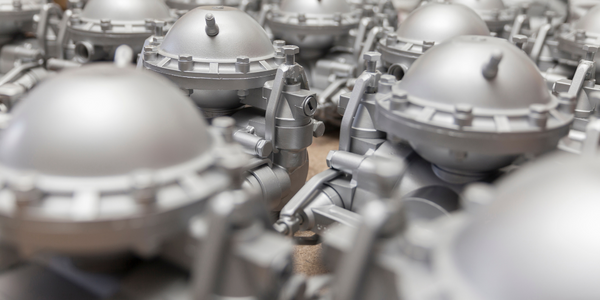
Case Study
Monitoring of Pressure Pumps in Automotive Industry
A large German/American producer of auto parts uses high-pressure pumps to deburr machined parts as a part of its production and quality check process. They decided to monitor these pumps to make sure they work properly and that they can see any indications leading to a potential failure before it affects their process.