Download PDF
Streamlining Truck Component Testing at IVECO Australia with HyperWorks and Altair Partner Alliance
Technology Category
- Other - Battery
- Sensors - Haptic Sensors
Applicable Industries
- Agriculture
- Automotive
Applicable Functions
- Product Research & Development
- Quality Assurance
Use Cases
- Manufacturing Process Simulation
- Time Sensitive Networking
Services
- System Integration
- Testing & Certification
The Challenge
IVECO Australia, a manufacturer and distributor of commercial vehicles, faced a challenge in reducing the size, weight, and solving time in Finite Element Analysis (FEA) while improving the durability of components. The company had to conduct physical durability testing, which often led to redesigning components that failed during the test. This unnecessary design loop extended the target release date and increased the idle time of trucks during repairs. The company sought to validate components through FEA to eliminate this design loop during physical durability testing. The challenge was to predict the durability and test pass rate of components before creating a prototype, while also meeting strict cost and weight targets. The battery box, mounted on the truck chassis, was particularly susceptible to mechanical vibration, which could cause structural damage and hamper battery life.
About The Customer
IVECO Australia is a manufacturer and distributor of light, medium, and heavy commercial vehicles for the Australian road transport industry. The company, formerly known as International Harvester and International Trucks, has been a part of Australia's way of life since 1902. IVECO is wholly owned by CNH Industrial, a global leader in capital goods that implements design, manufacturing, distribution, commercial, and financial activities in international markets. IVECO Australia manufactures ACCO, Powerstar, Stralis AS-L and AD/AT models, and bus chassis at its plant in Dandenong, Victoria. It also imports its Daily light commercial range, Eurocargo, and Stralis ATi models from IVECO plants in Europe and South America. IVECO Trucks Australia employs 600 people Australia wide, and the investment in the Australian truck market creates local employment for thousands more people in related industries, from operations to component suppliers.
The Solution
IVECO adopted HyperWorks on the recommendation of their first CAE employee and later discovered that their global parent companies, CNH Industrial and FCA Group, were already using HyperWorks extensively. The company has been using simulation modeling for over eight years, which has helped them cut down on testing time as many design concepts can be analyzed before a prototype is made. IVECO uses Altair HyperWorks and nCode DesignLife for fatigue analysis. HyperMesh has helped them mesh intricate and complicated models and handle larger models with ease. Stress analysis for fatigue is done in OptiStruct and then the models are imported into nCode DesignLife to calculate the fatigue. For the battery box, a mesh model was created in HyperMesh and then modal analysis was performed in OptiStruct to evaluate the battery box design. The final design was then evaluated for fatigue using dynamic analysis with nCode DesignLife.
Operational Impact
Quantitative Benefit
Related Case Studies.
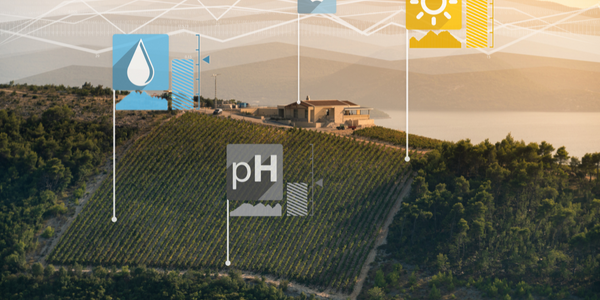
Case Study
Intelligent Farming with ThingWorx Analytics
Z Farms was facing three challenges: costly irrigation systems with water as a limited resource, narrow optimal ranges of soil moisture for growth with difficult maintenance and farm operators could not simply turn on irrigation systems like a faucet.
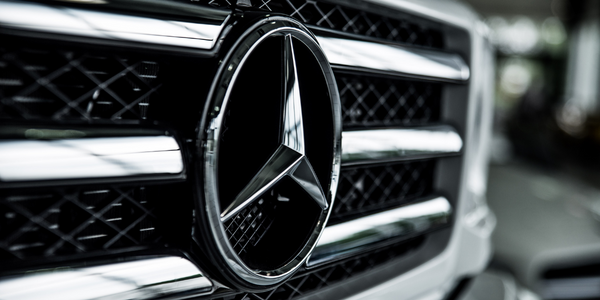
Case Study
Integral Plant Maintenance
Mercedes-Benz and his partner GAZ chose Siemens to be its maintenance partner at a new engine plant in Yaroslavl, Russia. The new plant offers a capacity to manufacture diesel engines for the Russian market, for locally produced Sprinter Classic. In addition to engines for the local market, the Yaroslavl plant will also produce spare parts. Mercedes-Benz Russia and his partner needed a service partner in order to ensure the operation of these lines in a maintenance partnership arrangement. The challenges included coordinating the entire maintenance management operation, in particular inspections, corrective and predictive maintenance activities, and the optimizing spare parts management. Siemens developed a customized maintenance solution that includes all electronic and mechanical maintenance activities (Integral Plant Maintenance).