Download PDF
Subaru Italia drives sales with QlikView
Technology Category
- Analytics & Modeling - Real Time Analytics
Applicable Industries
- Automotive
Applicable Functions
- Sales & Marketing
Use Cases
- Supply Chain Visibility
- Inventory Management
Services
- Software Design & Engineering Services
The Challenge
Subaru Italia, the official importer of Subaru for Italy, Slovenia, and Croatia, faced several challenges. The company needed to improve sales, dealer and garage management with the flow of vehicle orders. They also needed to manage credits and invoicing processes more efficiently. The company was looking for an easy-to-use business analysis system that could adapt with the company’s growth. Subaru Italia had been using business intelligence software since 1996, but as the company grew and the database evolved, they needed a tool with faster and simpler development capabilities. The company also needed an easy-to-deploy, dynamic and flexible tool to improve the sales area and management of its several dealers and garages.
About The Customer
Subaru Italia is the automotive division of Fuji Heavy Industries Ltd., created in 1953. Since 1986, Subaru Italia has been the official importer for Subaru in Italy, Slovenia, and Croatia. The company employs approximately 50 people and has a sales network that includes 72 car dealers and 150 authorized garages. Italian headquarters are in Ala di Trento. Last year, Subaru Italia generated sales of approximately €160 million. The company distributes, sells and provides after-sales service in all of the aforementioned countries.
The Solution
Subaru Italia chose QlikView, a complete suite of tools for business analysis developed by QlikTech International. The company appreciated QlikView’s depth of analysis, which immediately points out any anomalies and nonconformities of corporate data, as well as the program’s user-friendly interface. QlikView was implemented by Subaru Italia to manage vehicles, the administrative area and the spare parts warehouse. Nearly 90 % of its installation was managed entirely by Subaru Italia, with external consultation by QlikView Italy. Different models were created in the strategic area of vehicle management concerning sales, acquisitions, stock and registration data. The implementation of QlikView allows sales management and area managers to make use of data (constantly updated in real time) to view the position of each individual dealer and every vehicle from the moment it’s ordered to delivery to the final customer.
Operational Impact
Quantitative Benefit
Related Case Studies.
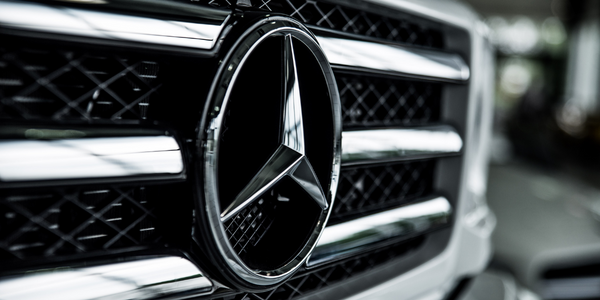
Case Study
Integral Plant Maintenance
Mercedes-Benz and his partner GAZ chose Siemens to be its maintenance partner at a new engine plant in Yaroslavl, Russia. The new plant offers a capacity to manufacture diesel engines for the Russian market, for locally produced Sprinter Classic. In addition to engines for the local market, the Yaroslavl plant will also produce spare parts. Mercedes-Benz Russia and his partner needed a service partner in order to ensure the operation of these lines in a maintenance partnership arrangement. The challenges included coordinating the entire maintenance management operation, in particular inspections, corrective and predictive maintenance activities, and the optimizing spare parts management. Siemens developed a customized maintenance solution that includes all electronic and mechanical maintenance activities (Integral Plant Maintenance).
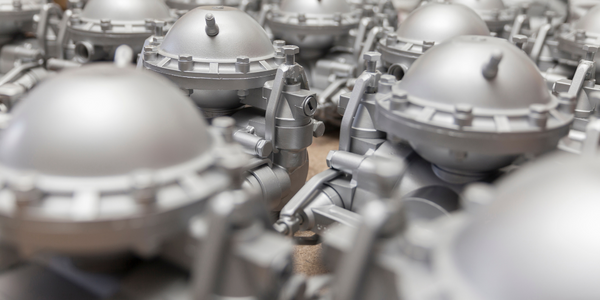
Case Study
Monitoring of Pressure Pumps in Automotive Industry
A large German/American producer of auto parts uses high-pressure pumps to deburr machined parts as a part of its production and quality check process. They decided to monitor these pumps to make sure they work properly and that they can see any indications leading to a potential failure before it affects their process.