Download PDF
Tesla's Innovative Approach to Optimizing Design Cycle with Automated CAE Connector Creation
Technology Category
- Analytics & Modeling - Digital Twin / Simulation
- Other - Battery
Applicable Industries
- Automotive
- Buildings
Applicable Functions
- Product Research & Development
Use Cases
- Virtual Prototyping & Product Testing
- Virtual Reality
The Challenge
Tesla Motors, a high-profile electric car manufacturer, was seeking ways to optimize its development cycle to expedite the production of high-quality vehicles. A significant challenge was the time-consuming process of preparing the finite element analysis (FEA) model, particularly the connector portion of its CAE model. The Model S sedan, for instance, had over 300 different fixings and more than 6,000 weld points, including welds, bolts, rivets, adhesives, and MIG welds. The most laborious task was recreating these connectors in the CAD model, which could take up to several days. This process was not only inefficient but also prone to errors, as there was a risk of overlooking a MIG weld or adhesive due to the lack of detail in the CAD file about the type of connector used, its mechanical properties, and the panels it was connecting.
About The Customer
Tesla Motors, founded in 2003 by Elon Musk, is a globally recognized electric vehicle manufacturer. The company's mission is to launch mass-marketed electric vehicles that appeal to buyers unimpressed with the quality and performance of first-generation electric car offerings. Tesla's strategy involves introducing high-end, high-performance sports cars to establish the viability and appeal of electric cars, followed by more affordable models for mainstream buyers. Since the launch of its first model, the Roadster, in 2008, Tesla has sold over 2,300 units and received orders for 6,900 Model S sedans in the last quarter of 2013 alone, marking a 25% increase over the previous quarter.
The Solution
To address this challenge, Tesla's simulation team, in collaboration with Altair, a CAE vendor, automated the connector creation process in the CAE model. They developed a connector (CNX) CAD structure, which included tags on the connector entities for consistency in naming and tree structure. This allowed the data to be easily extracted with a search string. They also created a CNX data merge tool, which generated an Excel file depicting CATIA geometric entities, connection types, and other attributes. An Excel macro was used to mark all relevant geometric entities in the spreadsheet for export based on the search string provided by the design engineer. Finally, a HyperMesh TCL script was developed to import the updated CATIA files into HyperMesh, create all the CAE connection elements for the various weld types, and highlight any connectors that failed to be created. This solution not only eliminated manual labor but also reduced the model creation process by a couple of days.
Operational Impact
Quantitative Benefit
Related Case Studies.
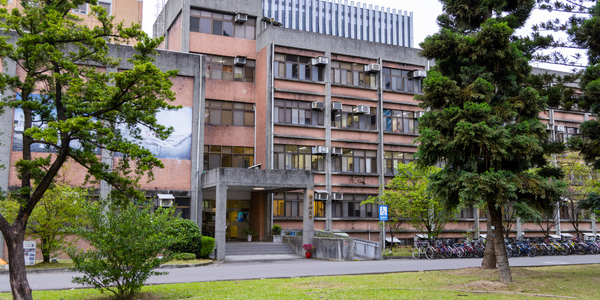
Case Study
Energy Saving & Power Monitoring System
Recently a university in Taiwan was experiencing dramatic power usage increases due to its growing number of campus buildings and students. Aiming to analyze their power consumption and increase their power efficiency across 52 buildings, the university wanted to build a power management system utilizing web-based hardware and software. With these goals in mind, they contacted Advantech to help them develop their system and provide them with the means to save energy in the years to come.
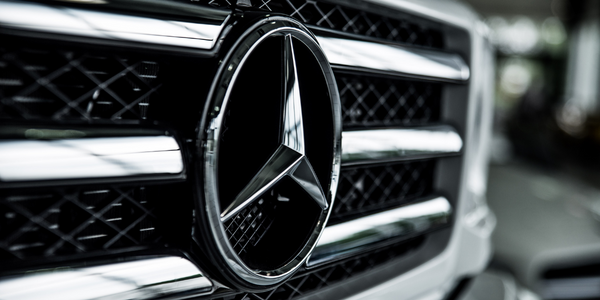
Case Study
Integral Plant Maintenance
Mercedes-Benz and his partner GAZ chose Siemens to be its maintenance partner at a new engine plant in Yaroslavl, Russia. The new plant offers a capacity to manufacture diesel engines for the Russian market, for locally produced Sprinter Classic. In addition to engines for the local market, the Yaroslavl plant will also produce spare parts. Mercedes-Benz Russia and his partner needed a service partner in order to ensure the operation of these lines in a maintenance partnership arrangement. The challenges included coordinating the entire maintenance management operation, in particular inspections, corrective and predictive maintenance activities, and the optimizing spare parts management. Siemens developed a customized maintenance solution that includes all electronic and mechanical maintenance activities (Integral Plant Maintenance).
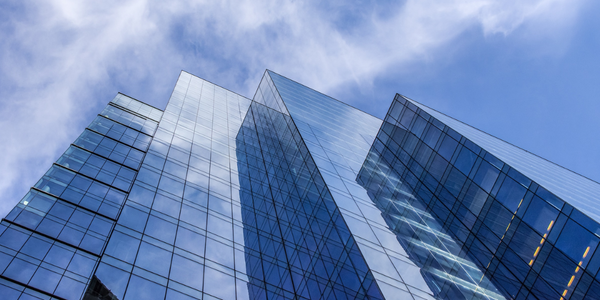
Case Study
Intelligent Building Automation System and Energy Saving Solution
One of the most difficult problems facing the world is conserving energy in buildings. However, it is not easy to have a cost-effective solution to reduce energy usage in a building. One solution for saving energy is to implement an intelligent building automation system (BAS) which can be controlled according to its schedule. In Indonesia a large university with a five floor building and 22 classrooms wanted to save the amount of energy being used.
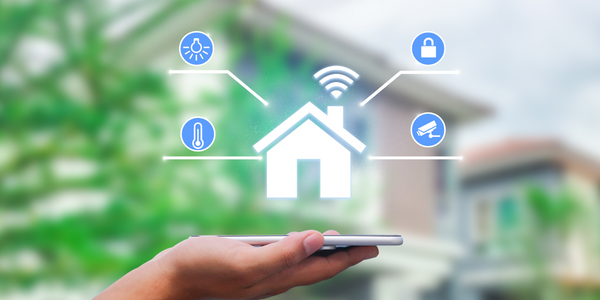
Case Study
Powering Smart Home Automation solutions with IoT for Energy conservation
Many industry leaders that offer Smart Energy Management products & solutions face challenges including:How to build a scalable platform that can automatically scale-up to on-board ‘n’ number of Smart home devicesData security, solution availability, and reliability are the other critical factors to deal withHow to create a robust common IoT platform that handles any kind of smart devicesHow to enable data management capabilities that would help in intelligent decision-making