Download PDF
The Devil’s in the Data for Bunzl North America
Technology Category
- Functional Applications - Fleet Management Systems (FMS)
- Analytics & Modeling - Real Time Analytics
Applicable Industries
- Retail
- Food & Beverage
- Healthcare & Hospitals
Applicable Functions
- Warehouse & Inventory Management
- Logistics & Transportation
Use Cases
- Fleet Management
- Predictive Maintenance
- Inventory Management
Services
- System Integration
- Data Science Services
The Challenge
Bunzl North America faced challenges in managing and maintaining its extensive fleet of lift trucks across its North American facilities. The company needed a way to track lift truck maintenance activities, determine the true cost of ownership, and assess when to service, replace, or reassign equipment. Without a centralized system, managers at each distribution center struggled to track costs and answer critical questions about lift truck usage, repair history, and cost per hour. This lack of visibility hindered their ability to make informed decisions about capital expenditures and fleet management.
About The Customer
Bunzl North America, headquartered in St. Louis, is a leading supplier of outsourced food packaging, disposable supplies, and cleaning and safety products. The company serves a diverse range of customers, including food processors, supermarkets, retailers, convenience stores, and healthcare providers. Bunzl stocks over 100,000 SKUs in its North American facilities, which are shipped to customers in various markets such as grocery, food service, cleaning and safety, non-food retail, and healthcare. The company operates a large fleet of Raymond lift trucks, including counterbalanced trucks, order pickers, and electric pallet trucks, to manage its extensive inventory and ensure efficient operations.
The Solution
To address its challenges, Bunzl North America implemented the iWAREHOUSE fleet and warehouse optimization system from The Raymond Corporation. This system provided real-time data on lift truck operations, enabling Bunzl to track maintenance activities, determine the true cost of ownership, and make informed decisions about servicing, replacing, or reassigning equipment. Additionally, Bunzl adopted the iTRACK system to further enhance its fleet management capabilities. The iTRACK system allowed Bunzl to monitor lift truck usage, repair history, and cost per hour, providing valuable insights for budgeting and capital expenditure planning. With these systems in place, Bunzl's distribution center managers could access detailed data on individual lift trucks, analyze costs, and assess equipment age to determine whether to keep or replace units. The centralized data also helped Bunzl ensure that each facility had the right number and mix of trucks to meet throughput requirements.
Operational Impact
Quantitative Benefit
Related Case Studies.
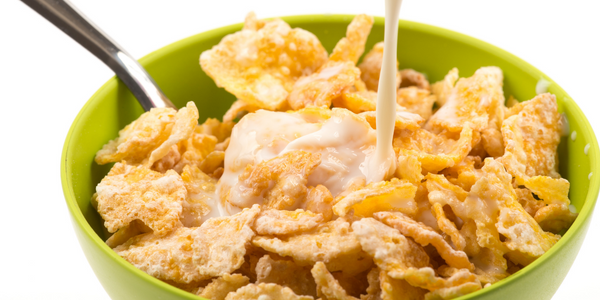
Case Study
The Kellogg Company
Kellogg keeps a close eye on its trade spend, analyzing large volumes of data and running complex simulations to predict which promotional activities will be the most effective. Kellogg needed to decrease the trade spend but its traditional relational database on premises could not keep up with the pace of demand.
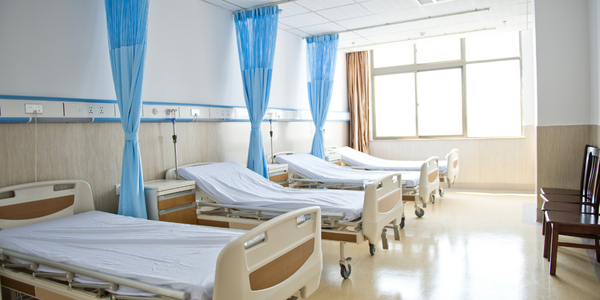
Case Study
Hospital Inventory Management
The hospital supply chain team is responsible for ensuring that the right medical supplies are readily available to clinicians when and where needed, and to do so in the most efficient manner possible. However, many of the systems and processes in use at the cancer center for supply chain management were not best suited to support these goals. Barcoding technology, a commonly used method for inventory management of medical supplies, is labor intensive, time consuming, does not provide real-time visibility into inventory levels and can be prone to error. Consequently, the lack of accurate and real-time visibility into inventory levels across multiple supply rooms in multiple hospital facilities creates additional inefficiency in the system causing over-ordering, hoarding, and wasted supplies. Other sources of waste and cost were also identified as candidates for improvement. Existing systems and processes did not provide adequate security for high-cost inventory within the hospital, which was another driver of cost. A lack of visibility into expiration dates for supplies resulted in supplies being wasted due to past expiry dates. Storage of supplies was also a key consideration given the location of the cancer center’s facilities in a dense urban setting, where space is always at a premium. In order to address the challenges outlined above, the hospital sought a solution that would provide real-time inventory information with high levels of accuracy, reduce the level of manual effort required and enable data driven decision making to ensure that the right supplies were readily available to clinicians in the right location at the right time.
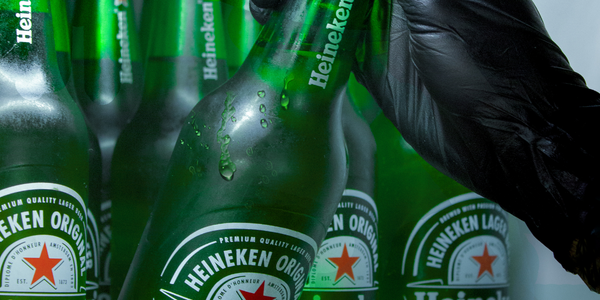
Case Study
HEINEKEN Uses the Cloud to Reach 10.5 Million Consumers
For 2012 campaign, the Bond promotion, it planned to launch the campaign at the same time everywhere on the planet. That created unprecedented challenges for HEINEKEN—nowhere more so than in its technology operation. The primary digital content for the campaign was a 100-megabyte movie that had to play flawlessly for millions of viewers worldwide. After all, Bond never fails. No one was going to tolerate a technology failure that might bruise his brand.Previously, HEINEKEN had supported digital media at its outsourced datacenter. But that datacenter lacked the computing resources HEINEKEN needed, and building them—especially to support peak traffic that would total millions of simultaneous hits—would have been both time-consuming and expensive. Nor would it have provided the geographic reach that HEINEKEN needed to minimize latency worldwide.
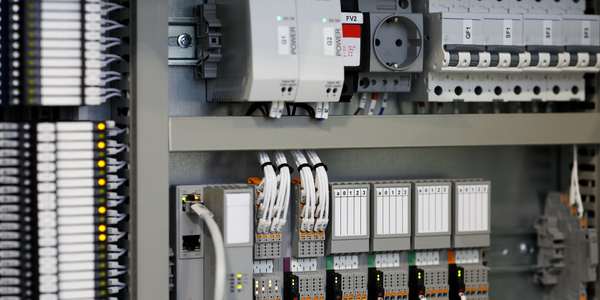
Case Study
Improving Production Line Efficiency with Ethernet Micro RTU Controller
Moxa was asked to provide a connectivity solution for one of the world's leading cosmetics companies. This multinational corporation, with retail presence in 130 countries, 23 global braches, and over 66,000 employees, sought to improve the efficiency of their production process by migrating from manual monitoring to an automatic productivity monitoring system. The production line was being monitored by ABB Real-TPI, a factory information system that offers data collection and analysis to improve plant efficiency. Due to software limitations, the customer needed an OPC server and a corresponding I/O solution to collect data from additional sensor devices for the Real-TPI system. The goal is to enable the factory information system to more thoroughly collect data from every corner of the production line. This will improve its ability to measure Overall Equipment Effectiveness (OEE) and translate into increased production efficiencies. System Requirements • Instant status updates while still consuming minimal bandwidth to relieve strain on limited factory networks • Interoperable with ABB Real-TPI • Small form factor appropriate for deployment where space is scarce • Remote software management and configuration to simplify operations
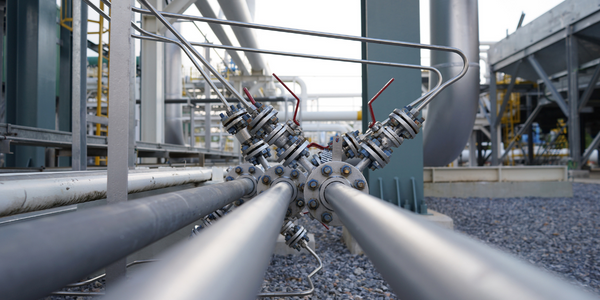
Case Study
Gas Pipeline Monitoring System for Hospitals
This system integrator focuses on providing centralized gas pipeline monitoring systems for hospitals. The service they provide makes it possible for hospitals to reduce both maintenance and labor costs. Since hospitals may not have an existing network suitable for this type of system, GPRS communication provides an easy and ready-to-use solution for remote, distributed monitoring systems System Requirements - GPRS communication - Seamless connection with SCADA software - Simple, front-end control capability - Expandable I/O channels - Combine AI, DI, and DO channels