Download PDF
Titan International on the Move with RF-SMART
Technology Category
- Functional Applications - Enterprise Resource Planning Systems (ERP)
- Functional Applications - Warehouse Management Systems (WMS)
Applicable Industries
- Automotive
Applicable Functions
- Business Operation
- Warehouse & Inventory Management
Use Cases
- Inventory Management
- Predictive Maintenance
- Warehouse Automation
Services
- System Integration
- Training
The Challenge
Titan International, a manufacturer of off-road and all-road wheels and tires, sought to replace disparate and legacy ERP systems with a unified system to prepare for long-term growth. They chose Oracle SCM Cloud to achieve this goal. Additionally, Titan aimed to eliminate paper processes and manual inventory updates with a mobile solution to increase inventory accuracy and provide real-time visibility into material movements. The company needed a partner to mirror Oracle Cloud in the manufacturing environment and provide production reports, leading them to select RF-SMART based on recommendations from Oracle and their implementation partner.
About The Customer
Titan International is a leading manufacturer of off-road and all-road wheels and tires, serving as an Original Equipment Manufacturer (OEM) with an extensive international distribution network that includes aftermarket channels. The company operates multiple facilities across North America and is focused on continuous growth and innovation. Titan's leadership is committed to modernizing their operations by implementing advanced technology solutions to streamline processes, enhance efficiency, and support long-term business objectives. With a strong emphasis on inventory management and production reporting, Titan International is dedicated to maintaining high standards of operational excellence and customer satisfaction.
The Solution
Titan International implemented Oracle SCM Cloud at three North American locations, with plans to expand to four additional US locations over the next two years. To complement this, they selected RF-SMART to achieve their mobile inventory management goals. RF-SMART provided out-of-the-box functionality for receiving, item inquiry, putaway, label design, and printing. Production employees used RF-SMART on tablets and scanners to report pieces and print labels. The solution also enabled Titan to track trailers on their 80-acre lot, significantly reducing the time required for inventorying trailer locations. The integration of RF-SMART with Oracle SCM Cloud allowed for real-time inventory movements, eliminating paperwork and associated delays, and improving the speed and accuracy of receiving processes. The implementation was smooth, with RF-SMART's flexibility and ease of use facilitating quick adoption by Titan employees.
Operational Impact
Quantitative Benefit
Related Case Studies.
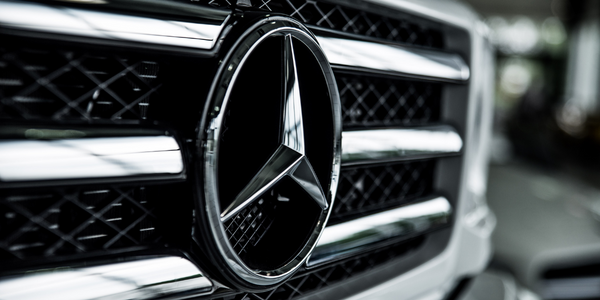
Case Study
Integral Plant Maintenance
Mercedes-Benz and his partner GAZ chose Siemens to be its maintenance partner at a new engine plant in Yaroslavl, Russia. The new plant offers a capacity to manufacture diesel engines for the Russian market, for locally produced Sprinter Classic. In addition to engines for the local market, the Yaroslavl plant will also produce spare parts. Mercedes-Benz Russia and his partner needed a service partner in order to ensure the operation of these lines in a maintenance partnership arrangement. The challenges included coordinating the entire maintenance management operation, in particular inspections, corrective and predictive maintenance activities, and the optimizing spare parts management. Siemens developed a customized maintenance solution that includes all electronic and mechanical maintenance activities (Integral Plant Maintenance).
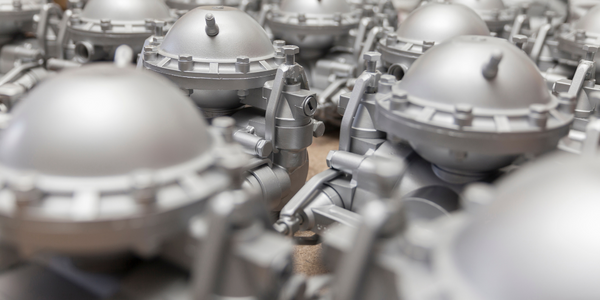
Case Study
Monitoring of Pressure Pumps in Automotive Industry
A large German/American producer of auto parts uses high-pressure pumps to deburr machined parts as a part of its production and quality check process. They decided to monitor these pumps to make sure they work properly and that they can see any indications leading to a potential failure before it affects their process.