Download PDF
Transforming Building Management with IoT: A Case Study on Learnd
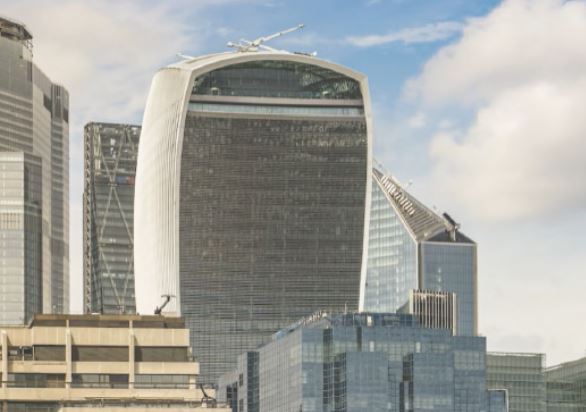
Technology Category
- Analytics & Modeling - Big Data Analytics
- Analytics & Modeling - Data-as-a-Service
Applicable Industries
- Buildings
- Retail
Use Cases
- Building Automation & Control
- Retail Store Automation
The Challenge
Buildings, like living organisms, consist of multiple systems that need to function seamlessly round the clock. However, maintaining aging equipment and facilities, dealing with utility issues, and controlling costs are ongoing concerns in the buildings industry. These challenges often undermine the well-being of the end-users, leading to dissatisfaction and lower performance. The various components of buildings usually have a long lifespan, and their management involves high risks and unexpected pitfalls. This situation leaves organizations struggling to focus on their core business while delivering a high-quality experience for end-users.
The Customer
Learnd
About The Customer
Learnd's customers are organizations that operate commercial premises across various sectors including critical infrastructure, healthcare, retail, education, government, and business offices. These organizations often struggle with the management of their buildings due to the high risks and unexpected pitfalls involved. They are in need of a solution that allows them to focus on their core business while ensuring that their buildings are well-maintained and provide a high-quality experience for end-users. Learnd's customers are spread across the UK and Europe, and they manage over 10,000 buildings.
The Solution
Learnd, a leading technology-led integrator for buildings, has partnered with Relayr to transform the way systems within a building are managed and maintained. Learnd helps its customers manage over 10,000 buildings across the UK and Europe, with strong sector expertise across healthcare, education, retail, critical infrastructure, data centers, and commercial offices. The partnership with Relayr and HSB enables a groundbreaking shift in the buildings industry. Relayr’s expertise in digitizing assets provides the backbone for Learnd’s capabilities by adding data processing and data analytics, combined with business enablement. For example, Learnd is now able to guarantee retail customers that their stores offer maximum shopper comfort or ensure a hospital that the conditions on its wards are optimized for patient care.
Operational Impact
Quantitative Benefit
Related Case Studies.
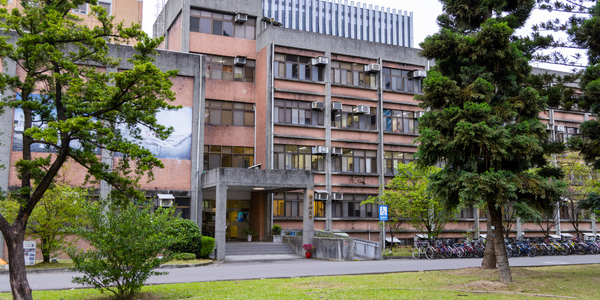
Case Study
Energy Saving & Power Monitoring System
Recently a university in Taiwan was experiencing dramatic power usage increases due to its growing number of campus buildings and students. Aiming to analyze their power consumption and increase their power efficiency across 52 buildings, the university wanted to build a power management system utilizing web-based hardware and software. With these goals in mind, they contacted Advantech to help them develop their system and provide them with the means to save energy in the years to come.
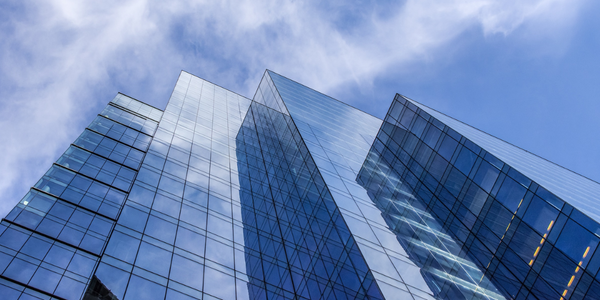
Case Study
Intelligent Building Automation System and Energy Saving Solution
One of the most difficult problems facing the world is conserving energy in buildings. However, it is not easy to have a cost-effective solution to reduce energy usage in a building. One solution for saving energy is to implement an intelligent building automation system (BAS) which can be controlled according to its schedule. In Indonesia a large university with a five floor building and 22 classrooms wanted to save the amount of energy being used.
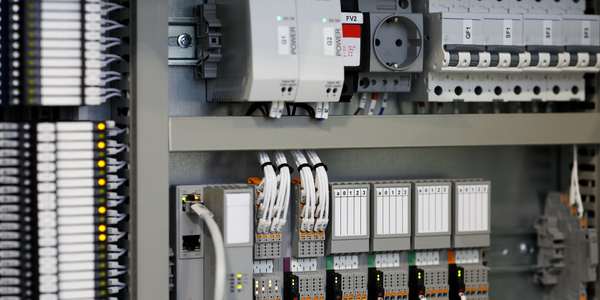
Case Study
Improving Production Line Efficiency with Ethernet Micro RTU Controller
Moxa was asked to provide a connectivity solution for one of the world's leading cosmetics companies. This multinational corporation, with retail presence in 130 countries, 23 global braches, and over 66,000 employees, sought to improve the efficiency of their production process by migrating from manual monitoring to an automatic productivity monitoring system. The production line was being monitored by ABB Real-TPI, a factory information system that offers data collection and analysis to improve plant efficiency. Due to software limitations, the customer needed an OPC server and a corresponding I/O solution to collect data from additional sensor devices for the Real-TPI system. The goal is to enable the factory information system to more thoroughly collect data from every corner of the production line. This will improve its ability to measure Overall Equipment Effectiveness (OEE) and translate into increased production efficiencies. System Requirements • Instant status updates while still consuming minimal bandwidth to relieve strain on limited factory networks • Interoperable with ABB Real-TPI • Small form factor appropriate for deployment where space is scarce • Remote software management and configuration to simplify operations
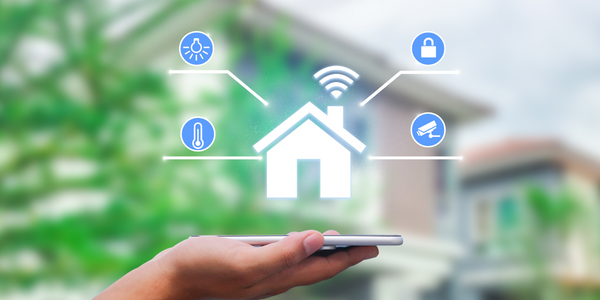
Case Study
Powering Smart Home Automation solutions with IoT for Energy conservation
Many industry leaders that offer Smart Energy Management products & solutions face challenges including:How to build a scalable platform that can automatically scale-up to on-board ‘n’ number of Smart home devicesData security, solution availability, and reliability are the other critical factors to deal withHow to create a robust common IoT platform that handles any kind of smart devicesHow to enable data management capabilities that would help in intelligent decision-making