Download PDF
Westfalia Technologies, Inc. Automated Pepsi Bottling Group
Technology Category
- Functional Applications - Warehouse Management Systems (WMS)
- Automation & Control - Automation & Process Control Systems
- Robots - Robot Application & Programming Software
Applicable Industries
- Food & Beverage
- Consumer Goods
Applicable Functions
- Warehouse & Inventory Management
- Logistics & Transportation
Use Cases
- Warehouse Automation
- Inventory Management
- Predictive Maintenance
Services
- System Integration
- Software Design & Engineering Services
The Challenge
The Pepsi Bottling Group needed a warehousing solution that would maximize their storage space and increase efficiency at peak times. Without this, production wouldn’t be quick enough to keep up with the increasing demand of their products. Turning to automation would allow the company to keep up with their customer needs and maintain their title as one of the most successful Pepsi Beverage Groups.
About The Customer
The Pepsi Bottling Group is the largest manufacturer, seller, and distributor of Pepsi beverages, with over 100 plants worldwide and 545 distribution centers. Among the brands they handle are Pepsi, Aquafina, Aqua Minerale, Tropicana, Lipton Iced Tea, Starbucks Frappuccino, Dole juices, Mountain Dew, Sierra Mist, and the SoBe line of beverages. The company is known for its extensive product range and significant market presence, making it a key player in the beverage industry. Their operations span globally, ensuring that their products reach a wide audience, and they are committed to maintaining high standards of quality and efficiency in their production and distribution processes.
The Solution
PBG selected a flexible, high-density AS/RS for their Tampa facility to meet their need for maximum storage, high throughput, buffers for handling peak production from their bottling plant, and aids in preparing various types of pallets to ship to customers. It was decided that a multiple deep system made the most sense, along with Westfalia’s other beverage manufacturing customers. Westfalia’s Savanna.NET WCS manages and controls all product flows throughout the facility from receiving to order fulfillment. It is a complex system as PBG requires full layer and mixed layer palletizing in order to have ‘store ready’ pallets loaded onto their straight and bay trucks. The company needed the system for product arriving from their own facility as well as outside bottling operations. Among the technologies controlled via Savanna.NET® WCS are the two Storage/Retrieval Machines (SRMs) of the AS/RS, conveying systems for pallets and cases, five KUKA robots for layer picking/palletizing, pallet squaring stations, stretch-wrapping, and print & apply labeling. S/RM Satellite technology allows each S/RM to handle 2 pallets at a time, which makes for lower energy consumption and lower system maintenance for the company.
Operational Impact
Quantitative Benefit
Related Case Studies.
.png)
Case Study
Improving Vending Machine Profitability with the Internet of Things (IoT)
The vending industry is undergoing a sea change, taking advantage of new technologies to go beyond just delivering snacks to creating a new retail location. Intelligent vending machines can be found in many public locations as well as company facilities, selling different types of goods and services, including even computer accessories, gold bars, tickets, and office supplies. With increasing sophistication, they may also provide time- and location-based data pertaining to sales, inventory, and customer preferences. But at the end of the day, vending machine operators know greater profitability is driven by higher sales and lower operating costs.
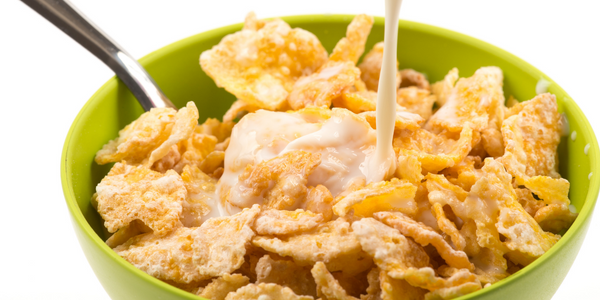
Case Study
The Kellogg Company
Kellogg keeps a close eye on its trade spend, analyzing large volumes of data and running complex simulations to predict which promotional activities will be the most effective. Kellogg needed to decrease the trade spend but its traditional relational database on premises could not keep up with the pace of demand.
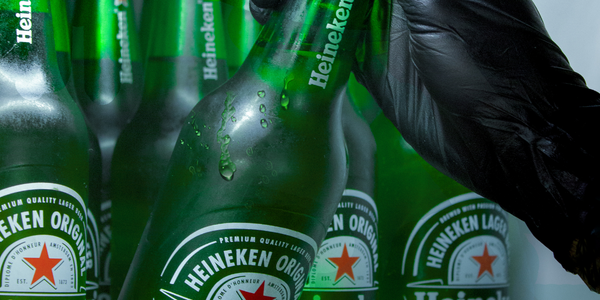
Case Study
HEINEKEN Uses the Cloud to Reach 10.5 Million Consumers
For 2012 campaign, the Bond promotion, it planned to launch the campaign at the same time everywhere on the planet. That created unprecedented challenges for HEINEKEN—nowhere more so than in its technology operation. The primary digital content for the campaign was a 100-megabyte movie that had to play flawlessly for millions of viewers worldwide. After all, Bond never fails. No one was going to tolerate a technology failure that might bruise his brand.Previously, HEINEKEN had supported digital media at its outsourced datacenter. But that datacenter lacked the computing resources HEINEKEN needed, and building them—especially to support peak traffic that would total millions of simultaneous hits—would have been both time-consuming and expensive. Nor would it have provided the geographic reach that HEINEKEN needed to minimize latency worldwide.
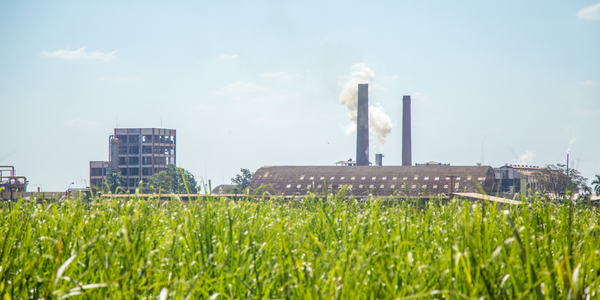
Case Study
Energy Management System at Sugar Industry
The company wanted to use the information from the system to claim under the renewable energy certificate scheme. The benefit to the company under the renewable energy certificates is Rs 75 million a year. To enable the above, an end-to-end solution for load monitoring, consumption monitoring, online data monitoring, automatic meter data acquisition which can be exported to SAP and other applications is required.
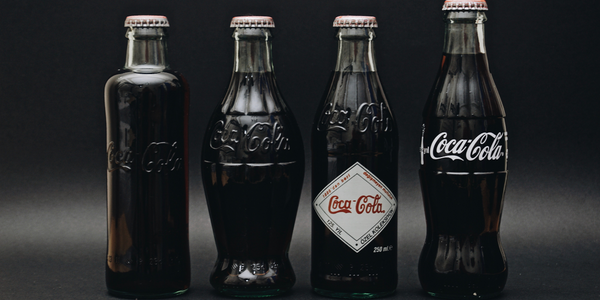
Case Study
Coca Cola Swaziland Conco Case Study
Coco Cola Swaziland, South Africa would like to find a solution that would enable the following results: - Reduce energy consumption by 20% in one year. - Formulate a series of strategic initiatives that would enlist the commitment of corporate management and create employee awareness while helping meet departmental targets and investing in tools that assist with energy management. - Formulate a series of tactical initiatives that would optimize energy usage on the shop floor. These would include charging forklifts and running cold rooms only during off-peak periods, running the dust extractors only during working hours and basing lights and air-conditioning on someone’s presence. - Increase visibility into the factory and other processes. - Enable limited, non-intrusive control functions for certain processes.