Download PDF
Withings: Leveraging Carbon Data for Low-Carbon Product Development
Applicable Industries
- Electronics
- Packaging
Applicable Functions
- Product Research & Development
- Quality Assurance
Use Cases
- Continuous Emission Monitoring Systems
Services
- Testing & Certification
The Challenge
Withings, a French electronics manufacturer, is committed to designing durable and low-carbon products that improve people's health. However, eco-design, or the process of designing low-carbon products, is a complex task. It requires detailed information on each stage of a product's life cycle, from material sourcing to product disposal, and testing alternatives to minimize the carbon footprint. The challenge lies in obtaining accurate measurements, which require high-quality emission factors at each step of the product's journey. Finding these can be time-consuming and expensive, depending on the emission factor databases involved, which can be national or international, public or private, and vary in scope. Additionally, conducting a life cycle assessment can be beyond the company's immediate control, as it involves gathering data on suppliers, which may not always be available or of good quality.
About The Customer
Withings is a consumer electronics manufacturer based in Issy-les-Moulineaux, France. The company, with a workforce of 340 employees, specializes in the production of smartwatches, scales, heart, and blood pressure monitors. Withings is committed to designing durable and low-carbon products that improve people's health. In October 2021, they began tracking their carbon footprint and issued their first carbon report at the beginning of 2022, demonstrating their commitment to sustainability and eco-friendly practices.
The Solution
Withings, where 85% of their emissions come from the products they sell, needed full visibility over their carbon data to create durable products and achieve their sustainability objectives. They partnered with Sweep to gain a complete overview of the emissions across their operations, value chain, and per product by collecting suppliers' carbon data. This allowed them to identify emission hotspots in their product life cycle and strategically act on them. For instance, they promoted maritime shipment instead of air freight. They also used the data to compare alternative materials and processes across each stage of a product's life cycle to inform the development of low-carbon products. For example, they tested different materials to design the most climate-friendly packaging.
Operational Impact
Quantitative Benefit
Related Case Studies.
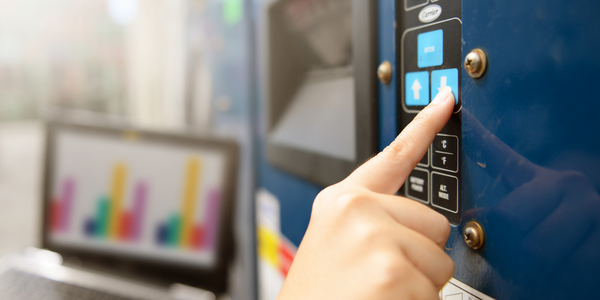
Case Study
Remote Temperature Monitoring of Perishable Goods Saves Money
RMONI was facing temperature monitoring challenges in a cold chain business. A cold chain must be established and maintained to ensure goods have been properly refrigerated during every step of the process, making temperature monitoring a critical business function. Manual registration practice can be very costly, labor intensive and prone to mistakes.
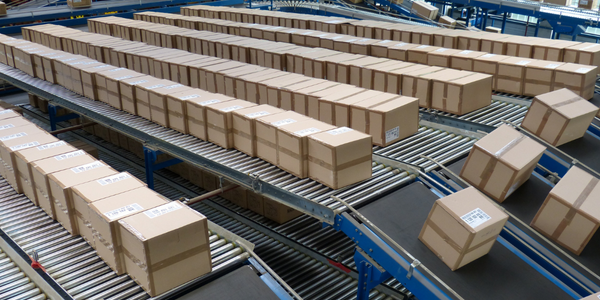
Case Study
IoT Data Analytics Case Study - Packaging Films Manufacturer
The company manufactures packaging films on made to order or configure to order basis. Every order has a different set of requirements from the product characteristics perspective and hence requires machine’s settings to be adjusted accordingly. If the film quality does not meet the required standards, the degraded quality impacts customer delivery causes customer dissatisfaction and results in lower margins. The biggest challenge was to identify the real root cause and devise a remedy for that.
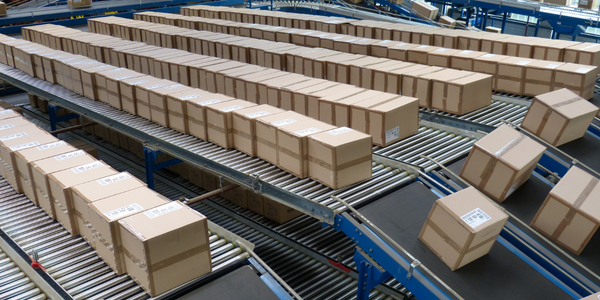
Case Study
Zenon the Ideal Basis for An Ergonomic HMI
KHS develops and produces machines and equipment for filling and packaging in the drinks industry. Because drinks manufacturing, filling and packaging consist of a number of highly complex processes, the user-friendly and intuitive operation of equipment is increasingly gaining in significance. In order to design these processes as simple as possible for the user, KHS decided to introduce a uniform, transparent and standardized solution to the company. The HMI interface should meet the requirement for people with different qualifications and enable them to work on a standard platform.
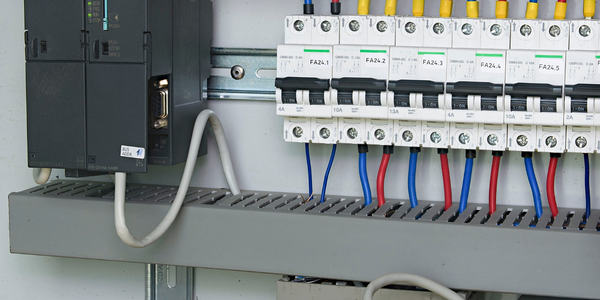
Case Study
Predictive maintenance in Schneider Electric
Schneider Electric Le Vaudreuil factory in France is recognized by the World Economic Forum as one of the world’s top nine most advanced “lighthouse” sites, applying Fourth Industrial Revolution technologies at large scale. It was experiencing machine-health and unplanned downtime issues on a critical machine within their manufacturing process. They were looking for a solution that could easily leverage existing machine data feeds, be used by machine operators without requiring complex setup or extensive training, and with a fast return on investment.