下载PDF
Chasing the next win: Oracle Red Bull Racing pushes data to the limit
技术
- 分析与建模 - 预测分析
- 分析与建模 - 实时分析
- 基础设施即服务 (IaaS) - 云计算
- 基础设施即服务 (IaaS) - 云存储服务
适用功能
- 产品研发
- 质量保证
用例
- 网络安全
- 边缘计算与边缘智能
- 预测性维护
- 实时定位系统 (RTLS)
服务
- 云规划/设计/实施服务
- 数据科学服务
- 硬件设计与工程服务
- 软件设计与工程服务
- 系统集成
挑战
Oracle Red Bull Racing team is in a constant race against time to develop and optimize their cars for each of the 22 races in the Formula One season. The team has to make thousands of changes to the car's design between races, each of which needs to be simulated, manufactured, and tested. The team also has to work within new Formula One design regulations and established cost caps, making efficiency a top priority. Furthermore, changes in F1 rules limit the number of aerodynamics testing hours each team can run per week, making it crucial to optimize every second and achieve peak application performance.
关于客户
Oracle Red Bull Racing is a Formula One racing team based in the United Kingdom. The team is composed of hundreds of people, including technicians, engineers, and drivers, all working towards the common goal of winning races. The team uses data-driven insights to develop and optimize their cars, making thousands of changes to the car's design between races. The team operates in a highly competitive and regulated environment, with new Formula One design regulations and established cost caps requiring them to be highly efficient in their use of resources. The team's success is heavily dependent on their ability to effectively use data and technology to drive performance improvements.
解决方案
To achieve maximum efficiency and performance, the Red Bull Racing team partnered with HPE. They implemented a range of HPE products including HPE SimpliVity, HPE Synergy, HPE Apollo 2000, HPE Apollo 6500, HPE Nimble Storage, and HPE Primera. These solutions provide a software-defined, composable platform that allows the team to quickly adapt to changes and maximize IT usage. The high-density platforms also support the team's quest for efficiency, saving money with reduced power, cooling, and footprint costs. HPE InfoSight delivers AI-enabled predictive analytics to prevent issues, while HPE Primera guarantees 100% availability. The team also uses HPE SimpliVity as the core of their mobile data center, providing post-processing of race telemetry data and real-time insight to optimize car setup and support in-race decision-making.
运营影响
数量效益
相关案例.
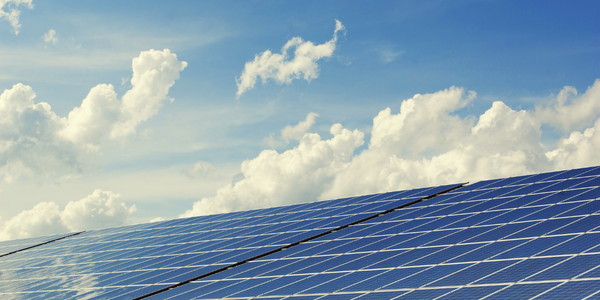
Case Study
Remote Monitoring & Predictive Maintenance App for a Solar Energy System
The maintenance & tracking of various modules was an overhead for the customer due to the huge labor costs involved. Being an advanced solar solutions provider, they wanted to ensure early detection of issues and provide the best-in-class customer experience. Hence they wanted to automate the whole process.
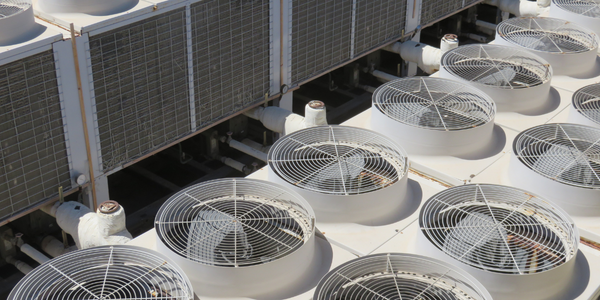
Case Study
Predictive Maintenance for Industrial Chillers
For global leaders in the industrial chiller manufacturing, reliability of the entire production process is of the utmost importance. Chillers are refrigeration systems that produce ice water to provide cooling for a process or industrial application. One of those leaders sought a way to respond to asset performance issues, even before they occur. The intelligence to guarantee maximum reliability of cooling devices is embedded (pre-alarming). A pre-alarming phase means that the cooling device still works, but symptoms may appear, telling manufacturers that a failure is likely to occur in the near future. Chillers who are not internet connected at that moment, provide little insight in this pre-alarming phase.
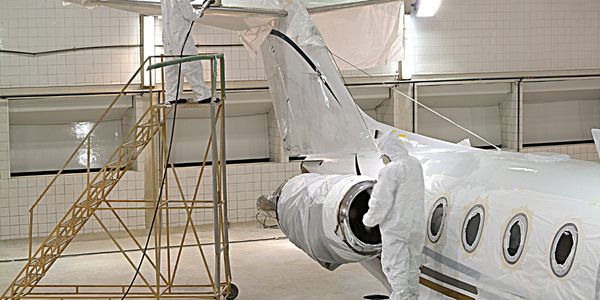
Case Study
Aircraft Predictive Maintenance and Workflow Optimization
First, aircraft manufacturer have trouble monitoring the health of aircraft systems with health prognostics and deliver predictive maintenance insights. Second, aircraft manufacturer wants a solution that can provide an in-context advisory and align job assignments to match technician experience and expertise.
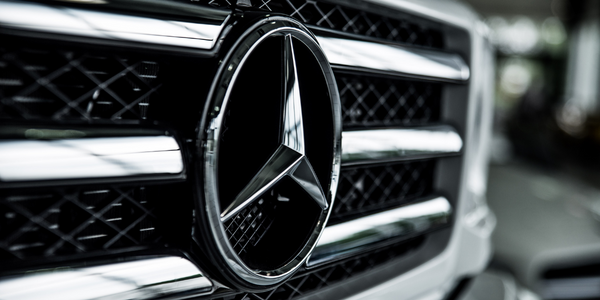
Case Study
Integral Plant Maintenance
Mercedes-Benz and his partner GAZ chose Siemens to be its maintenance partner at a new engine plant in Yaroslavl, Russia. The new plant offers a capacity to manufacture diesel engines for the Russian market, for locally produced Sprinter Classic. In addition to engines for the local market, the Yaroslavl plant will also produce spare parts. Mercedes-Benz Russia and his partner needed a service partner in order to ensure the operation of these lines in a maintenance partnership arrangement. The challenges included coordinating the entire maintenance management operation, in particular inspections, corrective and predictive maintenance activities, and the optimizing spare parts management. Siemens developed a customized maintenance solution that includes all electronic and mechanical maintenance activities (Integral Plant Maintenance).
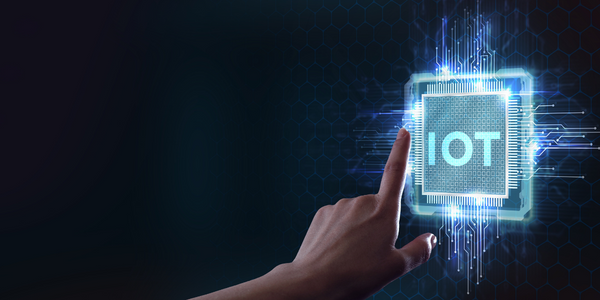
Case Study
Leading Tools Manufacturer Transforms Operations with IoT
Stanley Black & Decker required transparency of real-time overall equipment effectiveness and line productivity to reduce production line change over time.The goal was to to improve production to schedule, reduce actual labor costs and understanding the effects of shift changes and resource shifts from line to line.

Case Study
Asset Management and Predictive Maintenance
The customer prides itself on excellent engineering and customer centric philosophy, allowing its customer’s minds to be at ease and not worry about machine failure. They can easily deliver the excellent maintenance services to their customers, but there are some processes that can be automated to deliver less downtime for the customer and more efficient maintenance schedules.