下载PDF
Cloud-based High-Performance Computing for Aerodynamic and Thermal Analyses
技术
- 基础设施即服务 (IaaS) - 云计算
- 传感器 - 红外传感器
适用行业
- 建筑与基础设施
- 可再生能源
适用功能
- 产品研发
用例
- 时间敏感网络
- 交通模拟
服务
- 云规划/设计/实施服务
挑战
西班牙工程公司 KeelWit Technology 的任务是建造一座拥有欧洲最高风室的垂直风洞。挑战在于分析复杂的空气动力学环境并设计一条节能风洞,为客户提供最佳体验。垂直风洞规模庞大且复杂,每次设计变更都要创建物理原型,成本高昂且耗时。模拟气压、热损失和风速等变量需要大型网格和密集的计算机计算。KeelWit 寻求从其本地工作站扩展到云端的高性能计算 (HPC) 资源。
关于客户
KeelWit Technology 是一家西班牙工程公司,成立于 2011 年,总部位于马德里。该公司采用深厚的技术方法设计、开发和实施项目。 KeelWit 专注于三个主要领域:能源效率、CFD 分析和环保移动解决方案。通过风洞项目,他们成为 EYDISA 风洞的合作伙伴,并在马德里建造了他们的第一个设施。
解决方案
KeelWit 与云服务提供商 Gompute 合作,后者提供了即用型 HPC 软件环境,包括可视化、作业提交和数据管理。这种合作关系使 KeelWit 能够运行更高保真度的模拟并更有效地管理波动的项目工作负载。通过使用基于云的 HPC 和 ANSYS Fluent,KeelWit 能够分析和优化客户实施的实际设计,以提高系统性能。他们现在正致力于利用 ANSYS Workbench 和 DesignXplorer 的强大功能来自动化云中的工作流程,并在更短的时间内为其所有项目找到更好的设计。
运营影响
数量效益
相关案例.
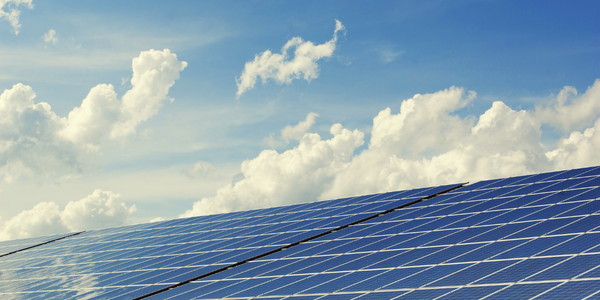
Case Study
Remote Monitoring & Predictive Maintenance App for a Solar Energy System
The maintenance & tracking of various modules was an overhead for the customer due to the huge labor costs involved. Being an advanced solar solutions provider, they wanted to ensure early detection of issues and provide the best-in-class customer experience. Hence they wanted to automate the whole process.
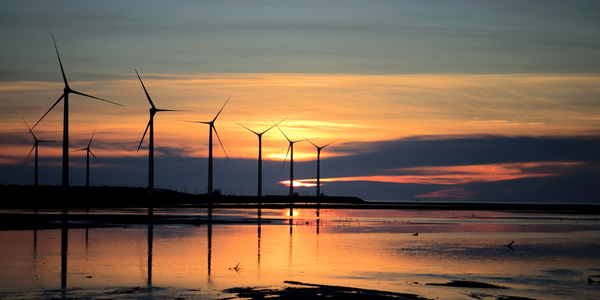
Case Study
Vestas: Turning Climate into Capital with Big Data
Making wind a reliable source of energy depends greatly on the placement of the wind turbines used to produce electricity. Turbulence is a significant factor as it strains turbine components, making them more likely to fail. Vestas wanted to pinpoint the optimal location for wind turbines to maximize power generation and reduce energy costs.
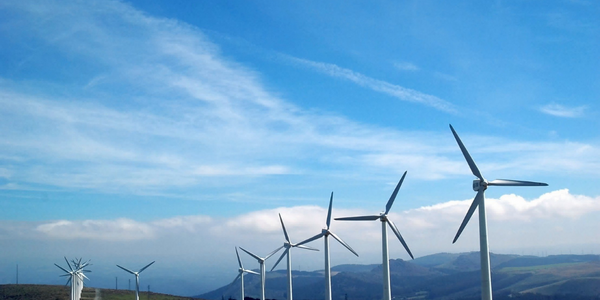
Case Study
Siemens Wind Power
Wind provides clean, renewable energy. The core concept is simple: wind turbines spin blades to generate power. However, today's systems are anything but simple. Modern wind turbines have blades that sweep a 120 meter circle, cost more than 1 million dollars and generate multiple megawatts of power. Each turbine may include up to 1,000 sensors and actuators – integrating strain gages, bearing monitors and power conditioning technology. The turbine can control blade speed and power generation by altering the blade pitch and power extraction. Controlling the turbine is a sophisticated job requiring many cooperating processors closing high-speed loops and implementing intelligent monitoring and optimization algorithms. But the real challenge is integrating these turbines so that they work together. A wind farm may include hundreds of turbines. They are often installed in difficult-to-access locations at sea. The farm must implement a fundamentally and truly distributed control system. Like all power systems, the goal of the farm is to match generation to load. A farm with hundreds of turbines must optimize that load by balancing the loading and generation across a wide geography. Wind, of course, is dynamic. Almost every picture of a wind farm shows a calm sea and a setting sun. But things get challenging when a storm goes through the wind farm. In a storm, the control system must decide how to take energy out of gusts to generate constant power. It must intelligently balance load across many turbines. And a critical consideration is the loading and potential damage to a half-billion-dollar installed asset. This is no environment for a slow or undependable control system. Reliability and performance are crucial.
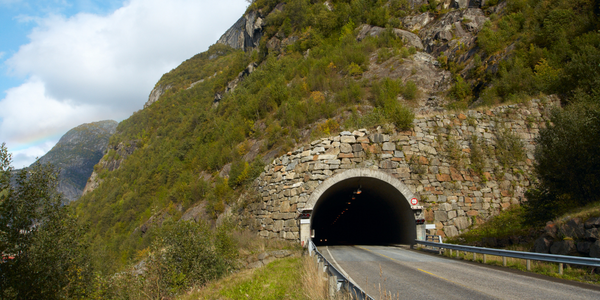
Case Study
IoT System for Tunnel Construction
The Zenitaka Corporation ('Zenitaka') has two major business areas: its architectural business focuses on structures such as government buildings, office buildings, and commercial facilities, while its civil engineering business is targeted at structures such as tunnels, bridges and dams. Within these areas, there presented two issues that have always persisted in regard to the construction of mountain tunnels. These issues are 'improving safety" and "reducing energy consumption". Mountain tunnels construction requires a massive amount of electricity. This is because there are many kinds of electrical equipment being used day and night, including construction machinery, construction lighting, and ventilating fan. Despite this, the amount of power consumption is generally not tightly managed. In many cases, the exact amount of power consumption is only ascertained when the bill from the power company becomes available. Sometimes, corporations install demand-monitoring equipment to help curb the maximum power demanded. However, even in these cases, the devices only allow the total volume of power consumption to be ascertained, or they may issue warnings to prevent the contracted volume of power from being exceeded. In order to tackle the issue of reducing power consumption, it was first necessary to obtain an accurate breakdown of how much power was being used in each particular area. In other words, we needed to be able to visualize the amount of power being consumed. Safety, was also not being managed very rigorously. Even now, tunnel construction sites often use a 'name label' system for managing entry into the work site. Specifically, red labels with white reverse sides that bear the workers' names on both sides are displayed at the tunnel work site entrance. The workers themselves then flip the name label to the appropriate side when entering or exiting from the work site to indicate whether or not they are working inside the tunnel at any given time. If a worker forgets to flip his or her name label when entering or exiting from the tunnel, management cannot be performed effectively. In order to tackle the challenges mentioned above, Zenitaka decided to build a system that could improve the safety of tunnel construction as well as reduce the amount of power consumed. In other words, this new system would facilitate a clear picture of which workers were working in each location at the mountain tunnel construction site, as well as which processes were being carried out at those respective locations at any given time. The system would maintain the safety of all workers while also carefully controlling the electrical equipment to reduce unnecessary power consumption. Having decided on the concept, our next concern was whether there existed any kind of robust hardware that would not break down at the construction work site, that could move freely in response to changes in the working environment, and that could accurately detect workers and vehicles using radio frequency identification (RFID). Given that this system would involve many components that were new to Zenitaka, we decided to enlist the cooperation of E.I.Sol Co., Ltd. ('E.I.Sol') as our joint development partner, as they had provided us with a highly practical proposal.
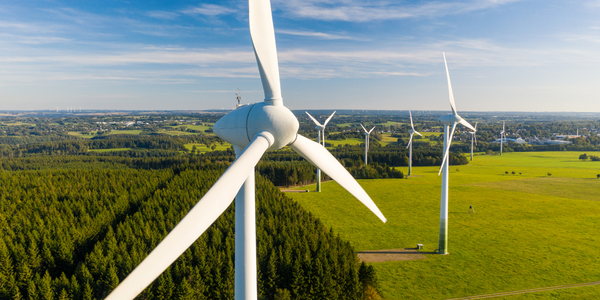
Case Study
Remote Monitoring and Control for a Windmill Generator
As concerns over global warming continue to grow, green technologies are becoming increasingly popular. Wind turbine companies provide an excellent alternative to burning fossil fuels by harnessing kinetic energy from the wind and converting it into electricity. A typical wind farm may include over 80 wind turbines so efficient and reliable networks to manage and control these installations are imperative. Each wind turbine includes a generator and a variety of serial components such as a water cooler, high voltage transformer, ultrasonic wind sensors, yaw gear, blade bearing, pitch cylinder, and hub controller. All of these components are controlled by a PLC and communicate with the ground host. Due to the total integration of these devices into an Ethernet network, one of our customers in the wind turbine industry needed a serial-to-Ethernet solution that can operate reliably for years without interruption.
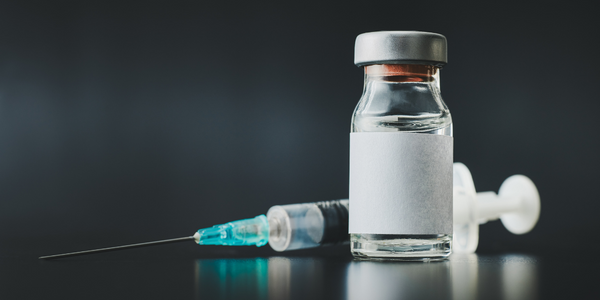
Case Study
Temperature monitoring for vaccine fridges
Dulas wanted a way to improve the reliability of the cold chain, facilitating maintenance and ensuring fewer vaccines are spoiled. Dulas wanted an M2M solution which would enable them to record and report the temperature inside vaccine refrigerators.