下载PDF
Coca-Cola Beverages Florida: Streamlining Operations with Nintex Process Platform
技术
- 分析与建模 - 机器人过程自动化 (RPA)
- 基础设施即服务 (IaaS) - 公共云
适用行业
- 医疗保健和医院
- 运输
适用功能
- 物流运输
- 维护
用例
- 疾病追踪
- 最后一英里交付
服务
- 云规划/设计/实施服务
- 系统集成
挑战
佛罗里达州可口可乐饮料公司是一家初创公司,在分三个阶段收购其经营领土后,在整合其业务流程方面面临着重大挑战。该公司的制造、销售和分销业务并未完全整合,导致效率低下。尤其是运输业务,主要是手动操作,依靠纸质表格和流程来跟踪资产及其位置的关键信息。这种手动方法既耗时又麻烦,而且容易出错。同样,该公司在遗留流程存储库中存储了 600 多个流程,其中大部分是 PDF、视频、图片和电子表格的集合。这使得访问、管理和维护存储库变得困难,从而导致成本高昂,并降低了对关键流程的可见性和控制。
关于客户
可口可乐饮料佛罗里达有限责任公司是一家位于美国的消费品行业的初创公司。该公司在分三个阶段收购的领土上运营,这导致其业务流程缺乏整合。其业务涵盖制造、销售和分销。该公司在整合运营、管理流程存储库以及实施健康检查解决方案以应对 COVID-19 大流行方面面临挑战。该公司的企业转型办公室致力于发现和解决可能阻碍业务增长的问题。
解决方案
为了应对这些挑战,可口可乐饮料佛罗里达州实施了 Nintex Process Platform,这是一套产品,其中包括 Nintex Workflow Cloud、Nintex Workflow for Office 365、Nintex Forms、Nintex Promapp®、DocGen® 和 Nintex RPA®。该平台实现了整个公司运营的端到端集成,实现工作流程自动化,并用数字流程取代纸质流程。该公司的运输业务是最先受益于 Nintex 能力的业务之一。该公司还使用 Nintex Forms 和 Nintex Promapp® 建立了一个易于访问的存储库,提供对关键流程的可见性和控制,鼓励协作并增强责任感。为了应对 COVID-19 大流行,该公司利用其在 Nintex Forms、Workflow、Nintex Promapp 和 Nintex RPA 方面的经验,为其员工实施了快速、轻松的健康评估解决方案。
运营影响
数量效益
相关案例.
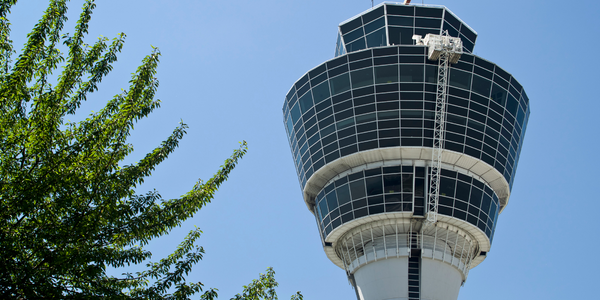
Case Study
Airport SCADA Systems Improve Service Levels
Modern airports are one of the busiest environments on Earth and rely on process automation equipment to ensure service operators achieve their KPIs. Increasingly airport SCADA systems are being used to control all aspects of the operation and associated facilities. This is because unplanned system downtime can cost dearly, both in terms of reduced revenues and the associated loss of customer satisfaction due to inevitable travel inconvenience and disruption.
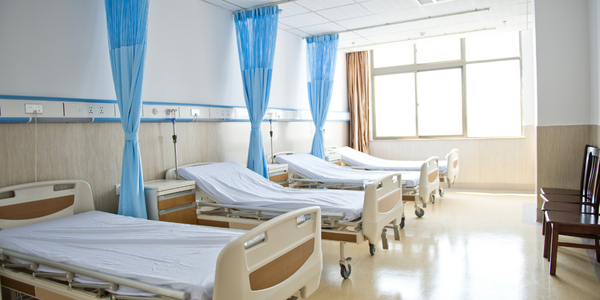
Case Study
Hospital Inventory Management
The hospital supply chain team is responsible for ensuring that the right medical supplies are readily available to clinicians when and where needed, and to do so in the most efficient manner possible. However, many of the systems and processes in use at the cancer center for supply chain management were not best suited to support these goals. Barcoding technology, a commonly used method for inventory management of medical supplies, is labor intensive, time consuming, does not provide real-time visibility into inventory levels and can be prone to error. Consequently, the lack of accurate and real-time visibility into inventory levels across multiple supply rooms in multiple hospital facilities creates additional inefficiency in the system causing over-ordering, hoarding, and wasted supplies. Other sources of waste and cost were also identified as candidates for improvement. Existing systems and processes did not provide adequate security for high-cost inventory within the hospital, which was another driver of cost. A lack of visibility into expiration dates for supplies resulted in supplies being wasted due to past expiry dates. Storage of supplies was also a key consideration given the location of the cancer center’s facilities in a dense urban setting, where space is always at a premium. In order to address the challenges outlined above, the hospital sought a solution that would provide real-time inventory information with high levels of accuracy, reduce the level of manual effort required and enable data driven decision making to ensure that the right supplies were readily available to clinicians in the right location at the right time.
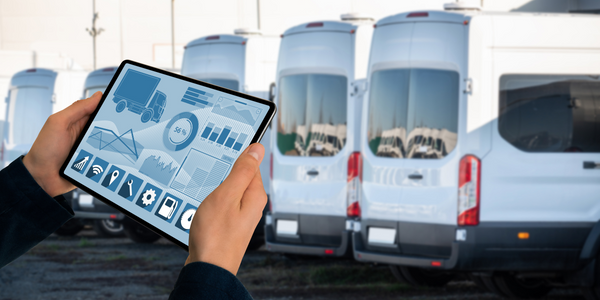
Case Study
IoT-based Fleet Intelligence Innovation
Speed to market is precious for DRVR, a rapidly growing start-up company. With a business model dependent on reliable mobile data, managers were spending their lives trying to negotiate data roaming deals with mobile network operators in different countries. And, even then, service quality was a constant concern.
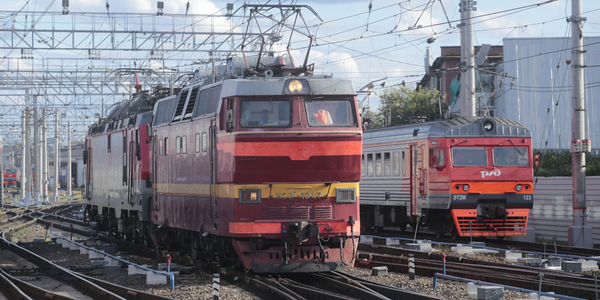
Case Study
Digitize Railway with Deutsche Bahn
To reduce maintenance costs and delay-causing failures for Deutsche Bahn. They need manual measurements by a position measurement system based on custom-made MEMS sensor clusters, which allow autonomous and continuous monitoring with wireless data transmission and long battery. They were looking for data pre-processing solution in the sensor and machine learning algorithms in the cloud so as to detect critical wear.

Case Study
Cold Chain Transportation and Refrigerated Fleet Management System
1) Create a digital connected transportation solution to retrofit cold chain trailers with real-time tracking and controls. 2) Prevent multi-million dollar losses due to theft or spoilage. 3) Deliver a digital chain-of-custody solution for door to door load monitoring and security. 4) Provide a trusted multi-fleet solution in a single application with granular data and access controls.
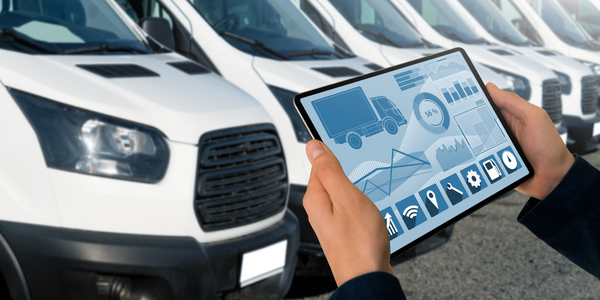
Case Study
Vehicle Fleet Analytics
Organizations frequently implement a maintenance strategy for their fleets of vehicles using a combination of time and usage based maintenance schedules. While effective as a whole, time and usage based schedules do not take into account driving patterns, environmental factors, and sensors currently deployed within the vehicle measuring crank voltage, ignition voltage, and acceleration, all of which have a significant influence on the overall health of the vehicle.In a typical fleet, a large percentage of road calls are related to electrical failure, with battery failure being a common cause. Battery failures result in unmet service agreement levels and costly re-adjustment of scheduled to provide replacement vehicles. To reduce the impact of unplanned maintenance, the transportation logistics company was interested in a trial of C3 Vehicle Fleet Analytics.