下载PDF
Customer Success Story: Mesa Laboratories, Inc.
技术
- 应用基础设施与中间件 - 数据交换与集成
- 功能应用 - 企业资源规划系统 (ERP)
- 功能应用 - 产品生命周期管理系统 (PLM)
适用行业
- 食品与饮料
- 医疗保健和医院
- 药品
适用功能
- 商业运营
- 质量保证
用例
- 过程控制与优化
- 监管合规监控
- 远程协作
服务
- 系统集成
- 培训
挑战
Mesa Labs realized that its legacy software systems could no longer support a growing business. Mesa labs relied on a manual system to manage the change control process. “We used ‘red folders’ containing all the change documents, and these were sent to the appropriate departments for approval. We also had to rely on timely updates to the ERP system. This led to ordering materials at the wrong revision level. It was also possible to have the same part number in different facilities for different items,” said Alcala. For any company regulated by the FDA and desiring to maintain ISO compliance, strict change control and adherence to documented procedures is paramount. “We had a couple of audits that were a cause for concern for FDA and ISO auditors. Management recognized that we needed to address this issue immediately.”
关于客户
Mesa Laboratories, Inc. is a growing, highly profitable public company based in Denver, Colorado. Mesa develops, manufactures, and markets high-quality process validation and monitoring instruments, and consumables. From Fortune 500 companies to high tech start-ups, Mesa Lab’s products are used to assure product quality, control manufacturing processes, and to solve problems in niche markets in healthcare, industrial, pharmaceutical, medical, and food processing applications. Mesa Lab’s products are characterized by technical excellence and superior industry reputations.
解决方案
In October 2015, Mesa labs introduced Autodesk® Fusion Lifecycle PLM integrated with NetSuite® ERP to manage document and change order control more efficiently. Both systems operate in the Cloud and made use of Jitterbit software integration to break down communication barriers between normally-siloed functions. Mesa Labs undertook a six-month implementation process. “On Autodesk’s recommendation, we hired Razorleaf, a local implementation consulting company,” said Alcala. “The first step involved Razorleaf, mapping out our existing processes. This was invaluable in order that they could understand our business and our frustrations. Next, Razorleaf, mapped out a new workflow in Fusion Lifecycle. We documented our procedures and trained the users over a three-week period. In addition, we brought in an outside consultant to validate the system.” Mesa Labs transferred the BOMs and documentation from their old systems into Fusion Lifecycle. “After spending three weeks cleaning up the data, we went live with Fusion Lifecycle. We ran both systems in parallel for two months. Following this, we stopped using the ‘red folders’ completely. The reaction from the users has been very positive. A key factor was having a ‘super user’, a go-to person that became a Fusion Lifecycle expert.”
运营影响
数量效益
相关案例.
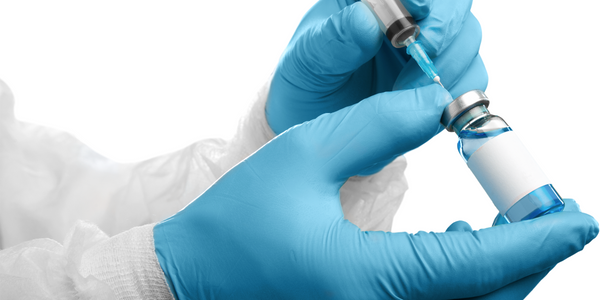
Case Study
Case Study: Pfizer
Pfizer’s high-performance computing software and systems for worldwide research and development support large-scale data analysis, research projects, clinical analytics, and modeling. Pfizer’s computing services are used across the spectrum of research and development efforts, from the deep biological understanding of disease to the design of safe, efficacious therapeutic agents.
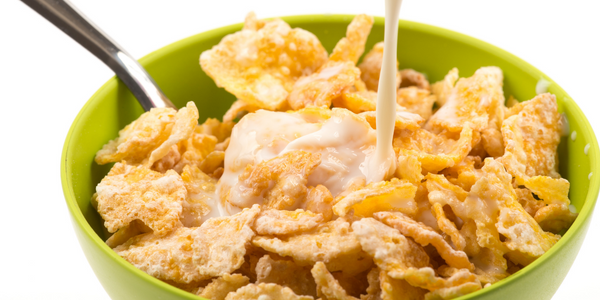
Case Study
The Kellogg Company
Kellogg keeps a close eye on its trade spend, analyzing large volumes of data and running complex simulations to predict which promotional activities will be the most effective. Kellogg needed to decrease the trade spend but its traditional relational database on premises could not keep up with the pace of demand.
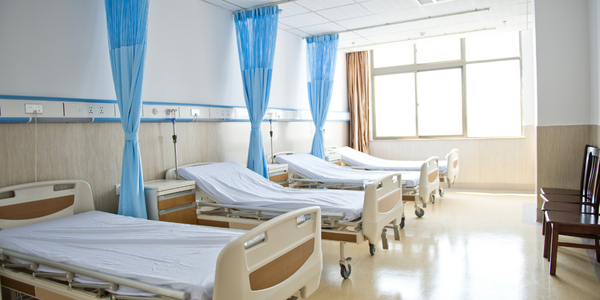
Case Study
Hospital Inventory Management
The hospital supply chain team is responsible for ensuring that the right medical supplies are readily available to clinicians when and where needed, and to do so in the most efficient manner possible. However, many of the systems and processes in use at the cancer center for supply chain management were not best suited to support these goals. Barcoding technology, a commonly used method for inventory management of medical supplies, is labor intensive, time consuming, does not provide real-time visibility into inventory levels and can be prone to error. Consequently, the lack of accurate and real-time visibility into inventory levels across multiple supply rooms in multiple hospital facilities creates additional inefficiency in the system causing over-ordering, hoarding, and wasted supplies. Other sources of waste and cost were also identified as candidates for improvement. Existing systems and processes did not provide adequate security for high-cost inventory within the hospital, which was another driver of cost. A lack of visibility into expiration dates for supplies resulted in supplies being wasted due to past expiry dates. Storage of supplies was also a key consideration given the location of the cancer center’s facilities in a dense urban setting, where space is always at a premium. In order to address the challenges outlined above, the hospital sought a solution that would provide real-time inventory information with high levels of accuracy, reduce the level of manual effort required and enable data driven decision making to ensure that the right supplies were readily available to clinicians in the right location at the right time.
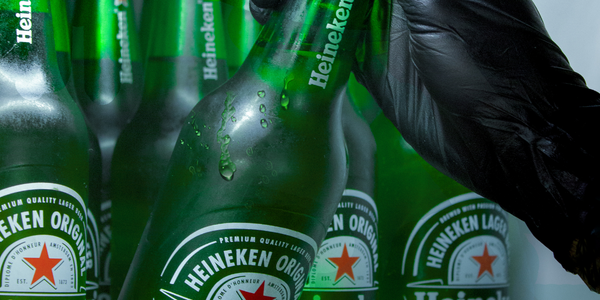
Case Study
HEINEKEN Uses the Cloud to Reach 10.5 Million Consumers
For 2012 campaign, the Bond promotion, it planned to launch the campaign at the same time everywhere on the planet. That created unprecedented challenges for HEINEKEN—nowhere more so than in its technology operation. The primary digital content for the campaign was a 100-megabyte movie that had to play flawlessly for millions of viewers worldwide. After all, Bond never fails. No one was going to tolerate a technology failure that might bruise his brand.Previously, HEINEKEN had supported digital media at its outsourced datacenter. But that datacenter lacked the computing resources HEINEKEN needed, and building them—especially to support peak traffic that would total millions of simultaneous hits—would have been both time-consuming and expensive. Nor would it have provided the geographic reach that HEINEKEN needed to minimize latency worldwide.
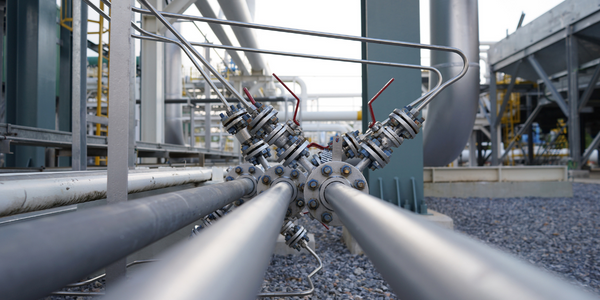
Case Study
Gas Pipeline Monitoring System for Hospitals
This system integrator focuses on providing centralized gas pipeline monitoring systems for hospitals. The service they provide makes it possible for hospitals to reduce both maintenance and labor costs. Since hospitals may not have an existing network suitable for this type of system, GPRS communication provides an easy and ready-to-use solution for remote, distributed monitoring systems System Requirements - GPRS communication - Seamless connection with SCADA software - Simple, front-end control capability - Expandable I/O channels - Combine AI, DI, and DO channels
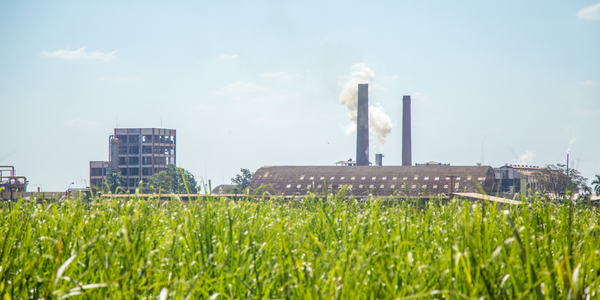
Case Study
Energy Management System at Sugar Industry
The company wanted to use the information from the system to claim under the renewable energy certificate scheme. The benefit to the company under the renewable energy certificates is Rs 75 million a year. To enable the above, an end-to-end solution for load monitoring, consumption monitoring, online data monitoring, automatic meter data acquisition which can be exported to SAP and other applications is required.